- Home
- › Indice Ricarica
- › Ricottura Colletto
Ricottura ad Induzione del Colletto
Ricarica
Bench Rest - Carabina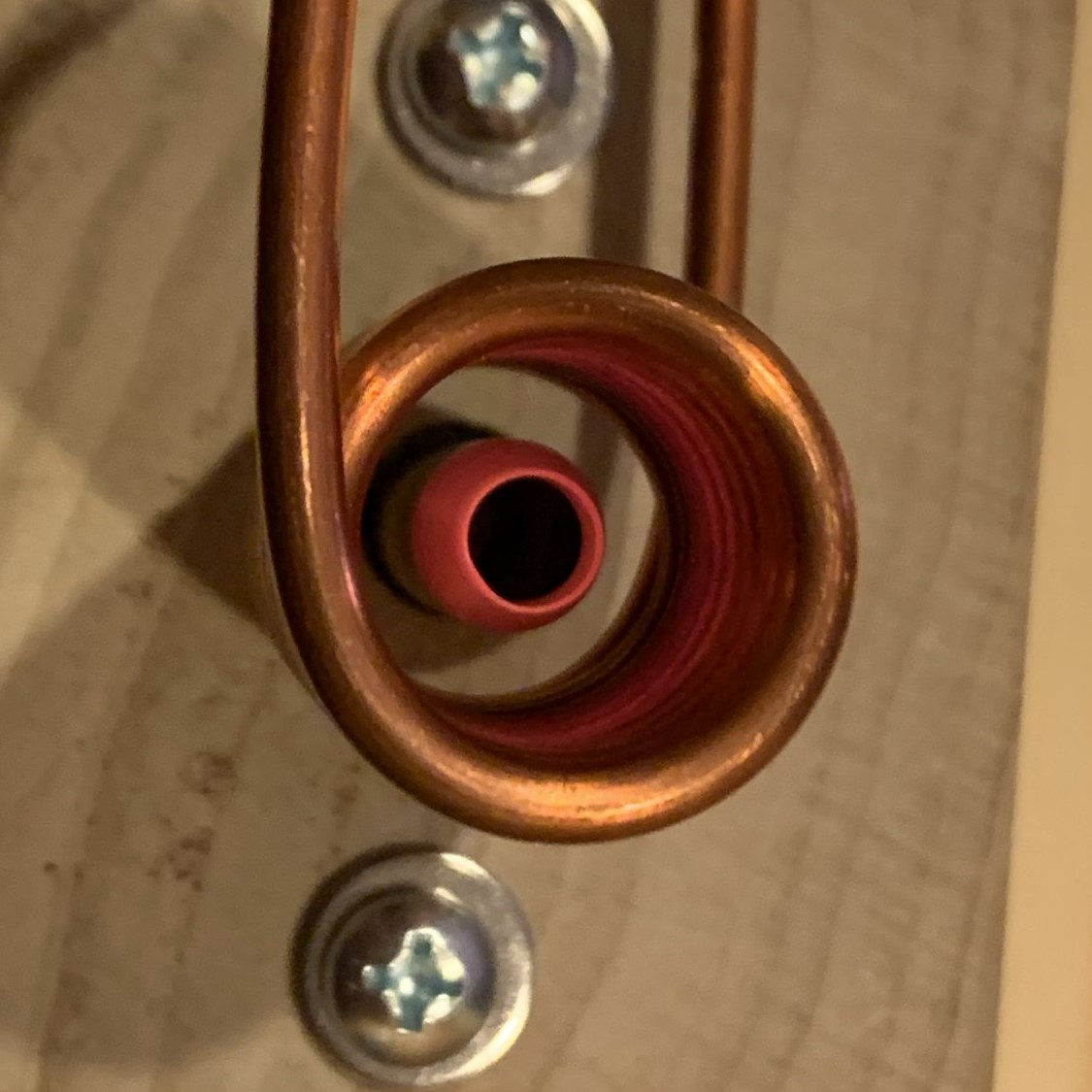
Ricottura ad Induzione
L'uso di un Sistema ad Induzione consente di ottenere una Ricottura Uniforme attraverso il preciso controllo di Temperatura & Tempo.
Con questo metodo il riscaldamento di oggetti, elettricamente conduttivi, viene realizzato attraverso Correnti Parassite (Induzione Elettromagnetica).
Il Processo di Induzione viene realizzato mediante un Oscillatore Elettronico in cui una Corrente Alternata ad Alta Frequenza, transitando in un Elettromagnete, produce delle Correnti Parassite.
Tali Correnti conducono al Riscaldamento dell'Oggetto penetrato dal Campo Magnetico Alternato.
Il Calore sarà direttamente generato all'interno del metallo senza l'uso di una fonte esterna di conseguenza non si avrà alcuna Contaminazione da Contatto.
Il Sistema ad Induzione consente anche la Fusione di Metalli Refrattari che richiedono Temperature Elevate.
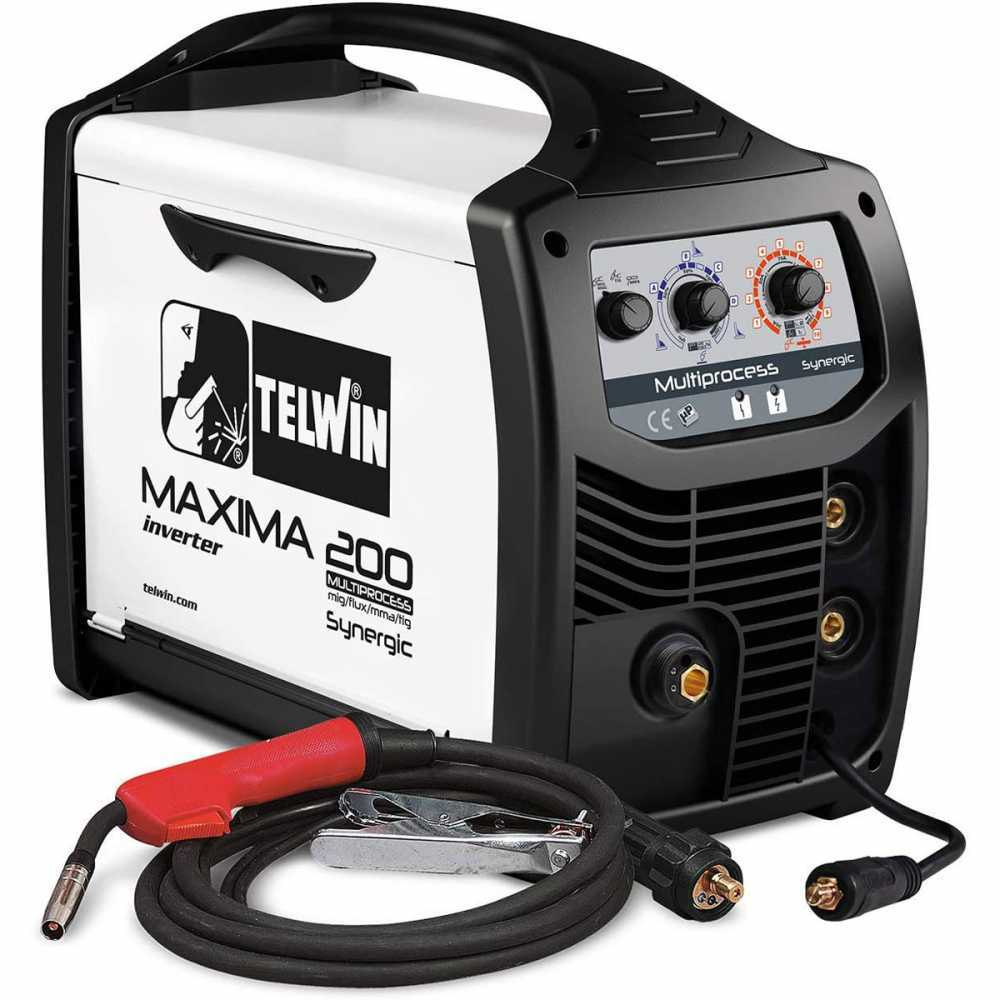
Saldatrice ad Inverter IGBT
Navigando in Rete sono disponibili vari Progetti per convertire una Saldatrice ad Invert IGBT come Annealer per Metalli.
Ho deciso di scartare questa soluzione poiché non volevo modificare la Scheda PCB per controllare il Tempo di Ricottura come avviene negli Annealer Professionali.
Tale problema avrebbe impedito di ottenere un uniformità nel Processo di Ricottura sul Colletto.
Medesimo Problema riscontrabile convertendo una Piastra da Cucina ad Induzione; argomento non trattato in questo Documento.
Commercialmente questa soluzione viene comunemende adottata dalla totalità dei Produttori di Annealer per la Ricarica vista l'ampia disponibilità sul Mercato di Schede PCB adattabili per tale scopo.
Al fine di semplificare la struttura vengono spesso impirgate delle Bobine a Nucleo Ferro Magnetico che non richiedono l'implementazione di un Sistema di Raffreddamento a Liquido.
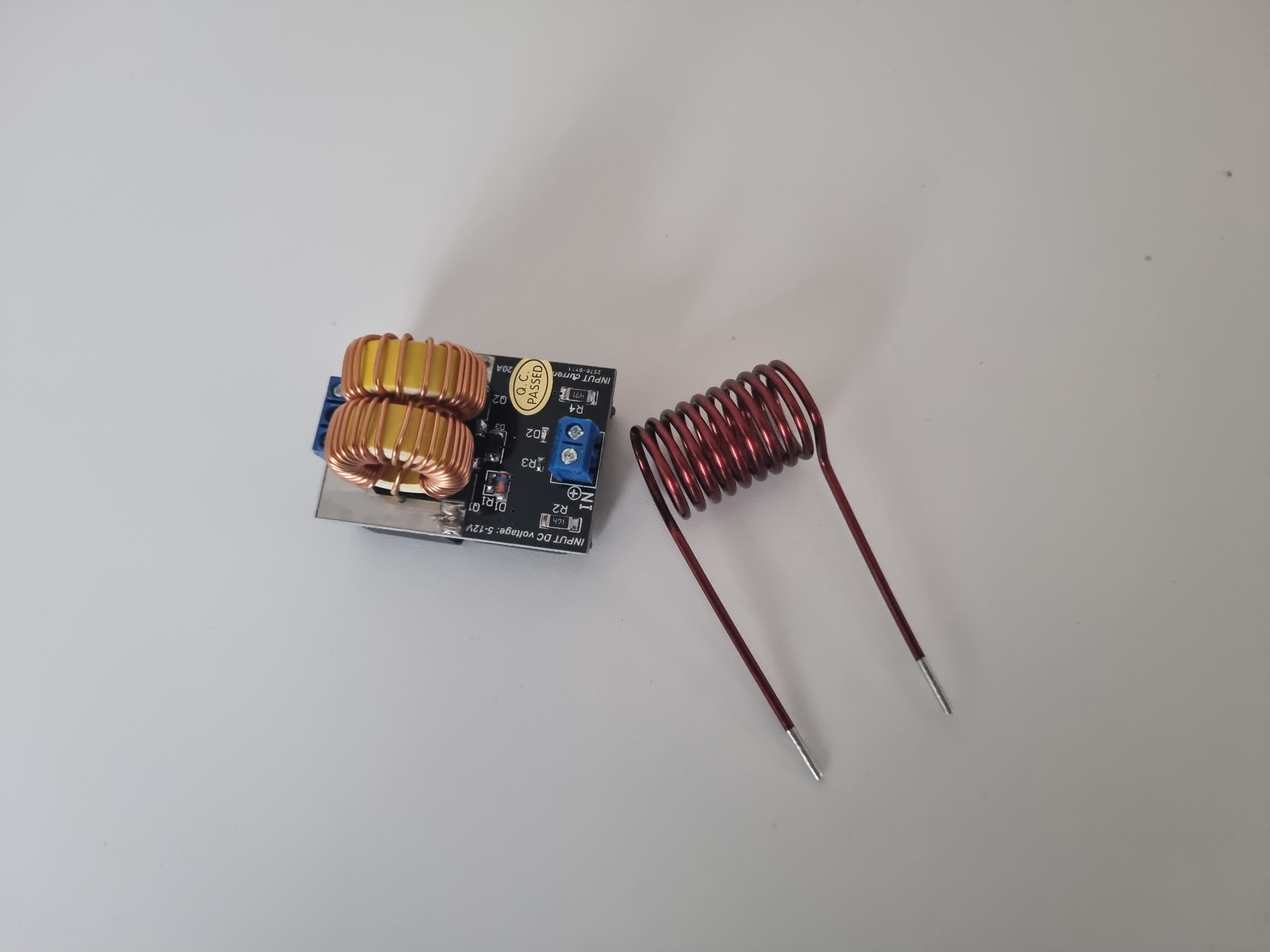
Mini PCB da 120W
Al fine di valutare la possibilità di realizzare un Annealer ad Induzione ho eseguito alcuni Test con una Micro Scheda PCB avente Potenza Massima di 120W.
Questo Dispositivo, tramite l’impiego di un Circuito Tipo ZVS (Zero Voltage Switching), permette di portare al Riscaldamento, ed eventualmente alla Fusione, Materiali Elettricamente Conduttori (Ferromagnetici).
Pur essendo richiesta un Tensione in Continua compresa fra 5 e 12 viene consigliata una Alimentazione di 12Vcc con Potenza non inferiore a 120W.
In relazione a queste Caratteristiche Tecniche ho optato per un Alimentatore da 12Vcc 10A.
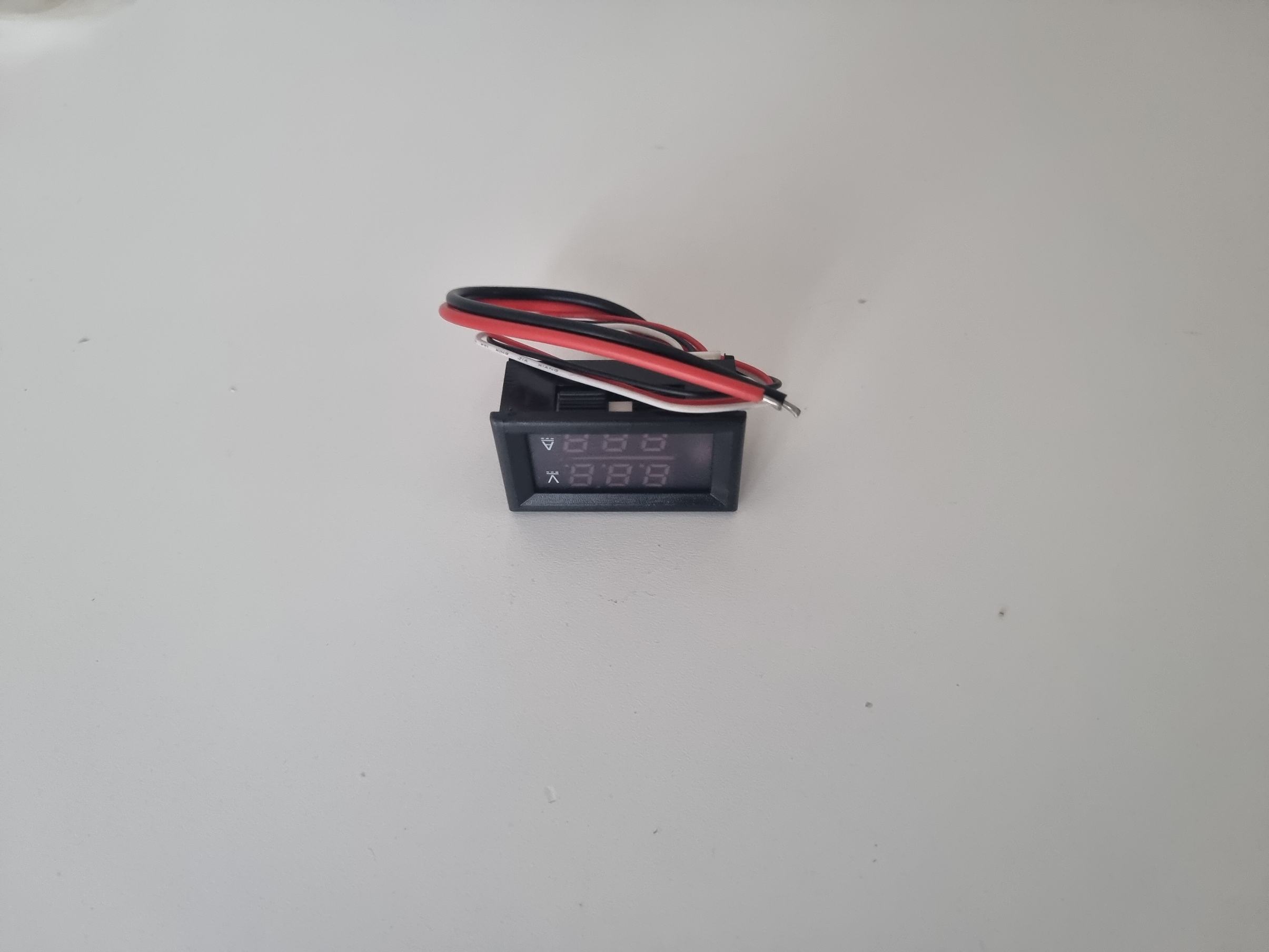
Sistema di Monitoraggio della Corrente Assorbita con Volmetro & Amperometro
Avvertenze: In talune Condizioni la Potenza assorbità potrebbe raggiungere anche i 150W.
Predisporre un Sistena per il Controllo & Monitoraggio della Corrente Assorbita (Volmetro & Amperometro) al fine di prevenirne possibili Guasti.
Nelle caratteristiche il Costruttore indica una Corrente di Risonanza per la Bobina di circa 100KHz con un Assobimento a Riposo di 30W (12Vcc).
Attenzione: Il ZVS Induction Heater potrebbe provocare disturbi ai Dispositivi Elettronici in relazione all’elevato Campo Magnetico prodotto di circa 10mT alla Frequenza di 100 kHz.
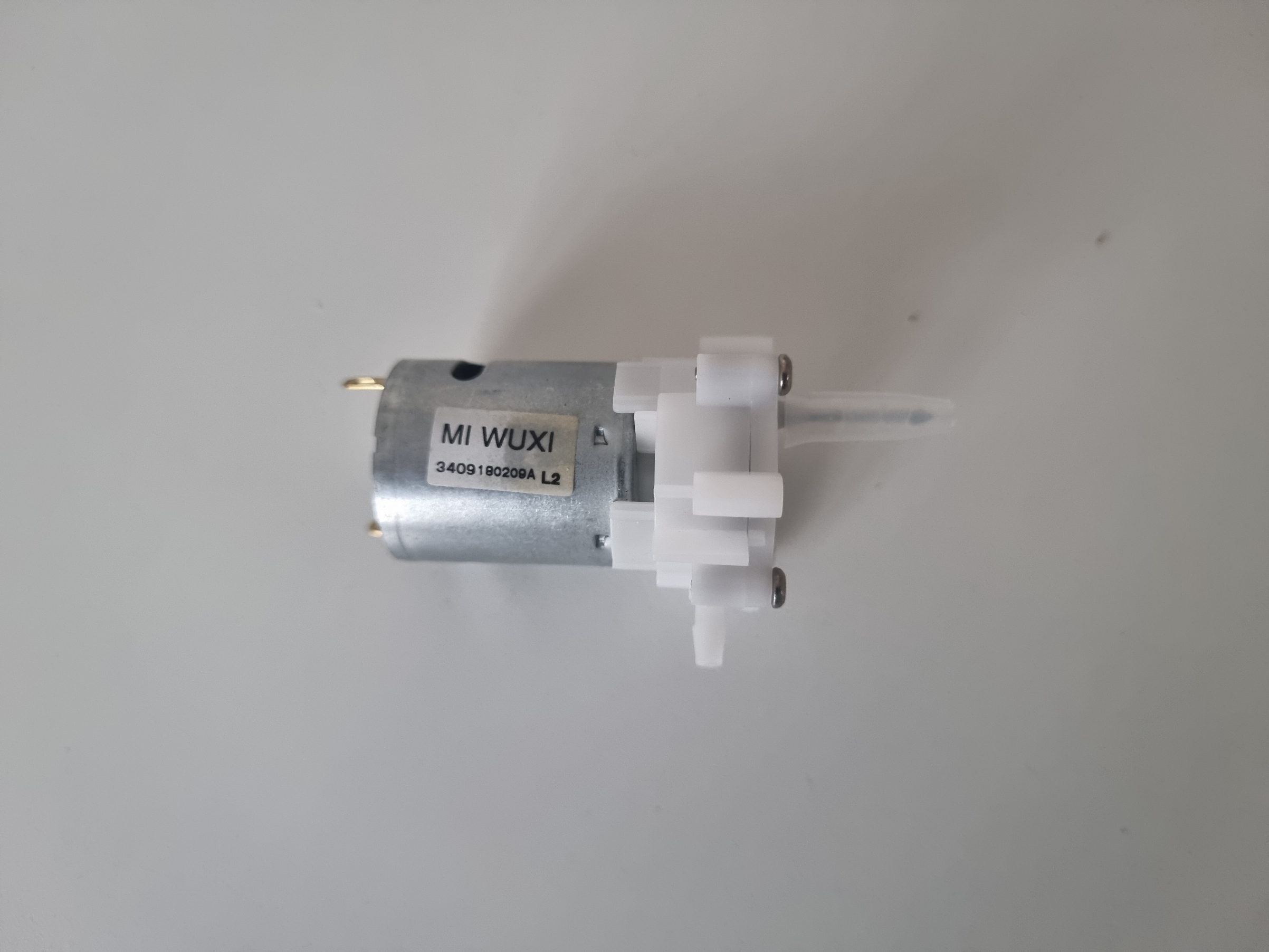
Pompa di Raffreddamento Bobina
Poiché l'Operazione di Ricottura sul Ottone produce un elevata Dissipazione Termica ho realizzato un Micro Circuito di Raffrendamento con una Micro Pompa e una Bottiglia/Serbatoio.
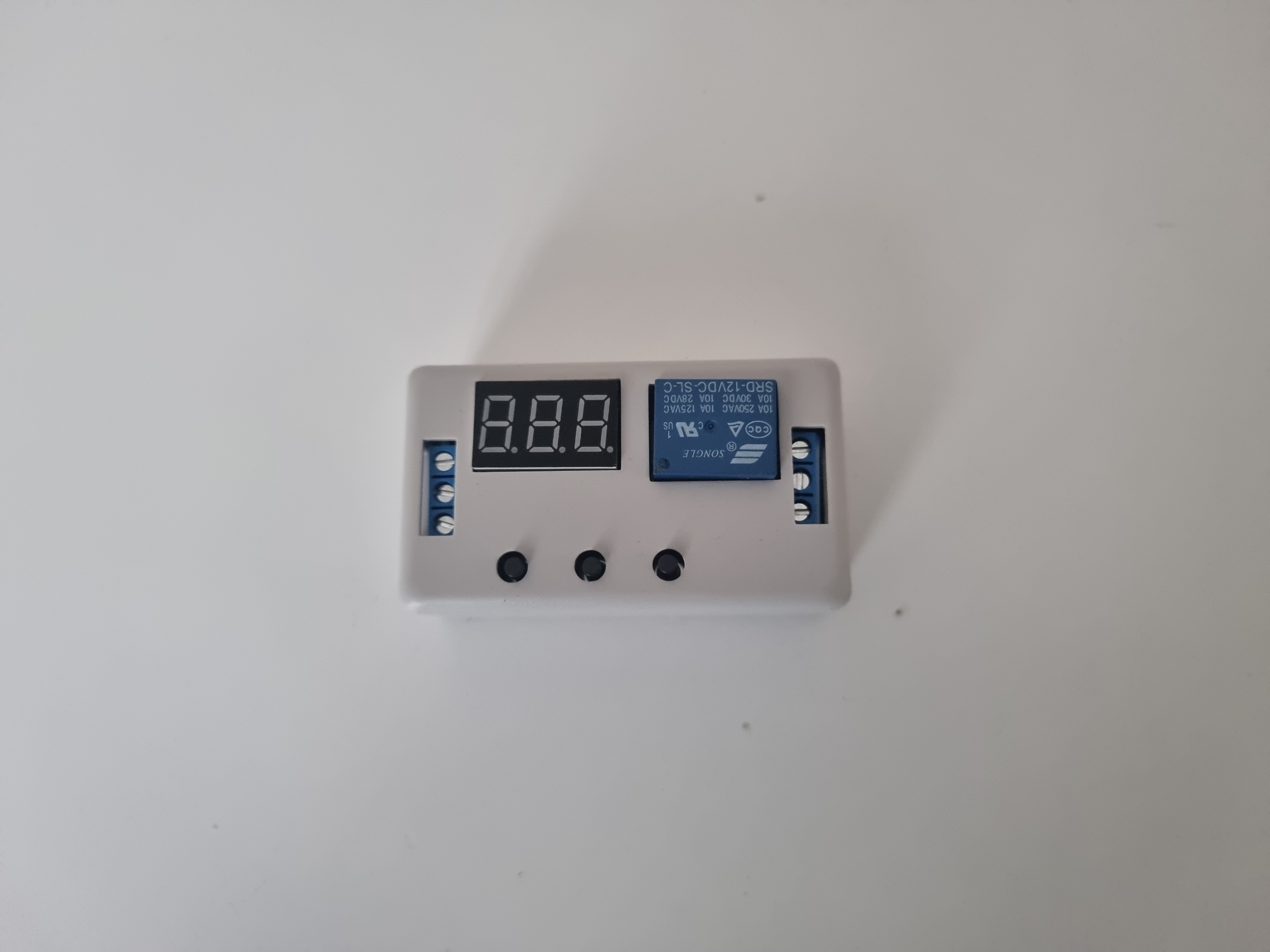
Timer 12V con Relè
Per il Controllo sul Tempo di Ricottura ho optato per un Timer a 12V con Relè Integrato in grado di gestire direttamente la Corrente Assorbita dalla Scheda PCB.
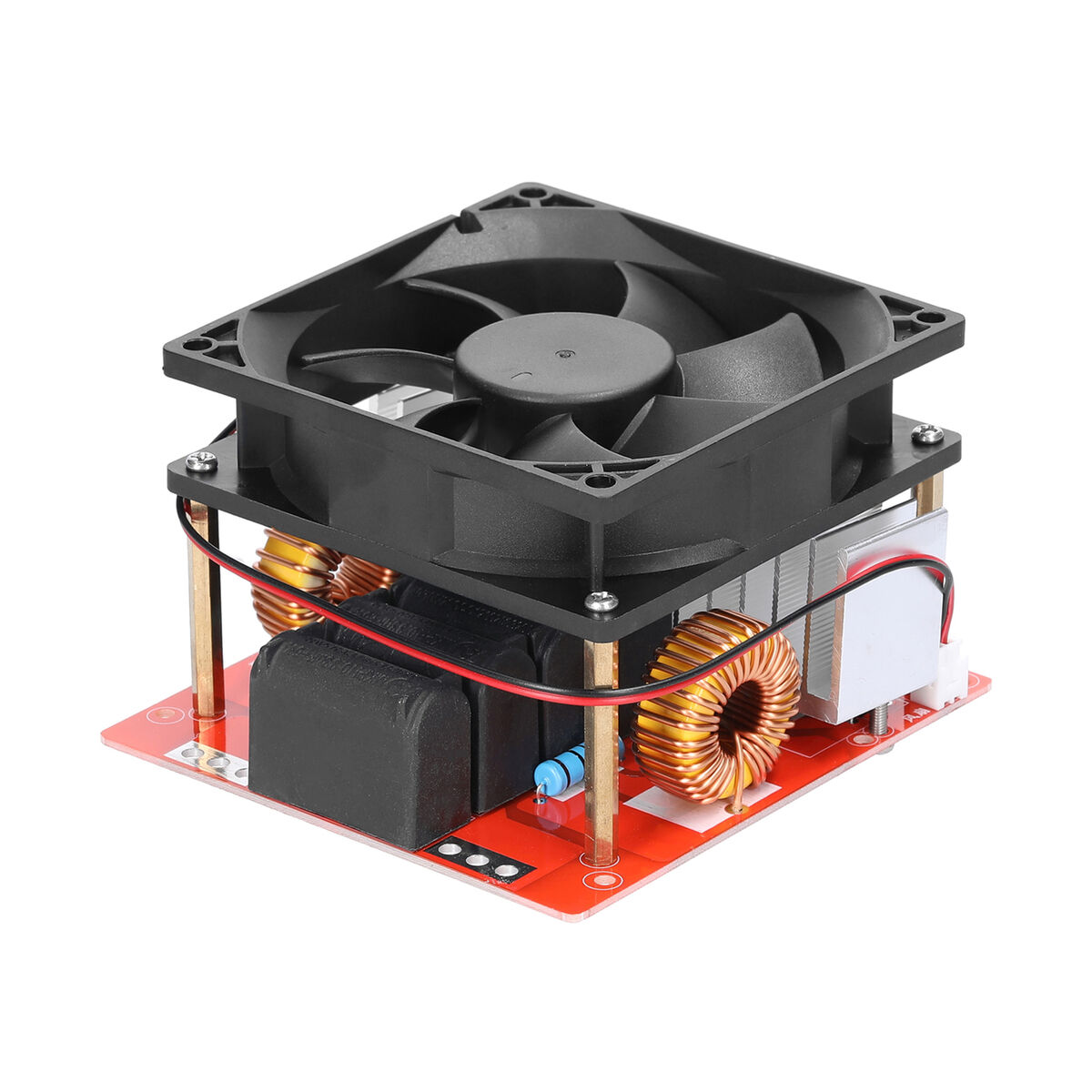
Scheda PCB da 720W per Ricottura ad Induzione
Al termine della Fase di Test ho selezionato una Scheda PCB da 720W avente le seguenti caratteristiche:
- Tensione d'Ingresso: 12V-36V (24V consigliata)
- Requisiti di Alimentazione:
Inferiore a 12V ≥ 5A
Superiore a 15V ≥ 10A (20A consigliata)
Secondo le Specifiche Tecniche viene solitamente richiesto un Alimentatore da 24V DC 20A (480W) per le Operazioni su Materiali Ferrosi mentre per i Materiali Non Ferrosi viene consigliato un Alimentatore da 36V DC 20A.
Senza Carico, con Tensione di 24V, avremo un Assorbimento Massimo di circa 3A di conseguenza con una Tensione Maggiore si avrà un migliore Redimento.
Naturalmente con l'aumentare della Tensione si avrà anche un maggiore Riscaldamento sulla Scheda PCB..
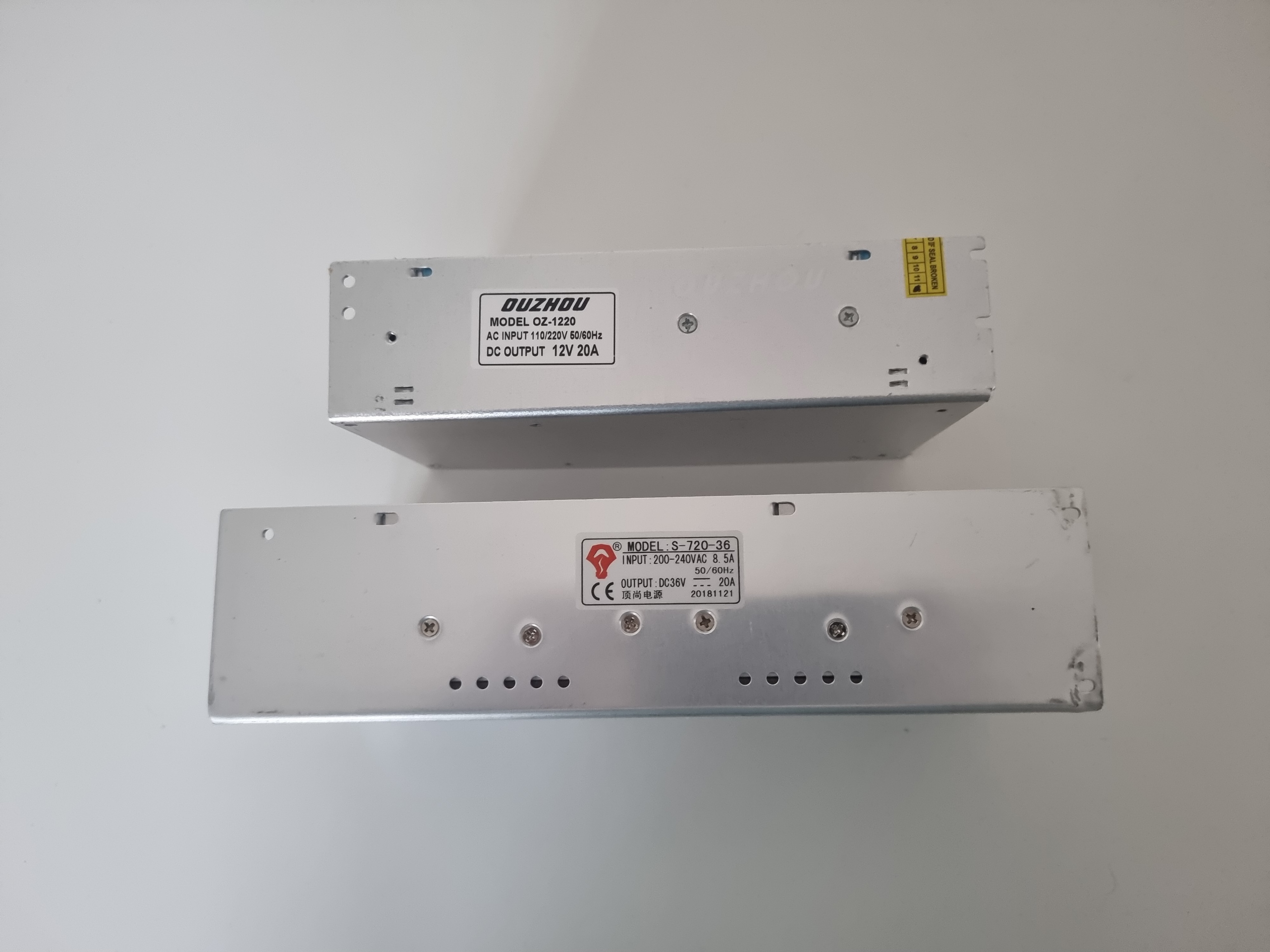
Alimentatore Principale 36V 20A & Secondario 12V 20A
Alla luce di queste considerazioni ho optato per un Alimentatore da 36V DC 20A in grado di erogare una Potenza Massima di 720W ideale per la Ricottura dell'Ottone.
Viene spesso sconsigliato un Alimentatore da 48V DC 15A in grado di garantire una maggiore velocità durante le Operazioni di Ricottura.
Pur avendo considerato il Modello a 48V ho optato per una Tensione Limite Inferiore per evitare il danneggiamento della Scheda PCB.
AVVERTENZA: In Fase di Accensione a Freddo, non alimentare la Scheda PCB finché non venga raggiunta la stabilizzazione della Tensione di Esercizio per evitarne danneggiamento.
Con Alimentatori ad Alta Potenza di Tipo Switching, ad avvio lento, attendere sempre la Stabilizzazione poiché una Tensione Insufficiente per l'innesco della Risonanza produce alla conduzione simultanea dei MOS fino alla loro fusione.
Applicare un Volmetro sulla Linea di Alimentazione della Scheda PCB per monitorarne la Tensione in Ingresso.
In ragione alla limitata Potenza questa Scheda PCB viene spesso utilizzata nelle Operazioni di Tempra, Ricottura o Fusione al di sotto di una Temperatura Massima di 1100°C.
Per la Fusione sarà necessario utilizzare un Crogiolo in Grafite 30x30mm, in grado di garantire un Riscaldamento Uniforme, e Alimentatore da 36V 25A.
Nelle Operazioni di Fusione non eccedere i 15A anche se la Scheda PCB riesce a tollerare Correnti in Ingresso comprese fra 20A e 30A.
Per la Fusione dell'Alluminio (660°C) viene richiesto un Alimentatore da 24V con Potenza compresa fra 350W (15A) e 500W (20A) mentre per Rame (1083°C), Oro (1065°C), Argento (962°C) viene richiesto un Alimentatore da 36V con Potenza compresa fra 700W (20A) e 900W (25A).
Solitamente la Scheda PCB viene fornita dal Produttore con Bobina in Rame senza un Sistema di Raffreddamento a Liquido.
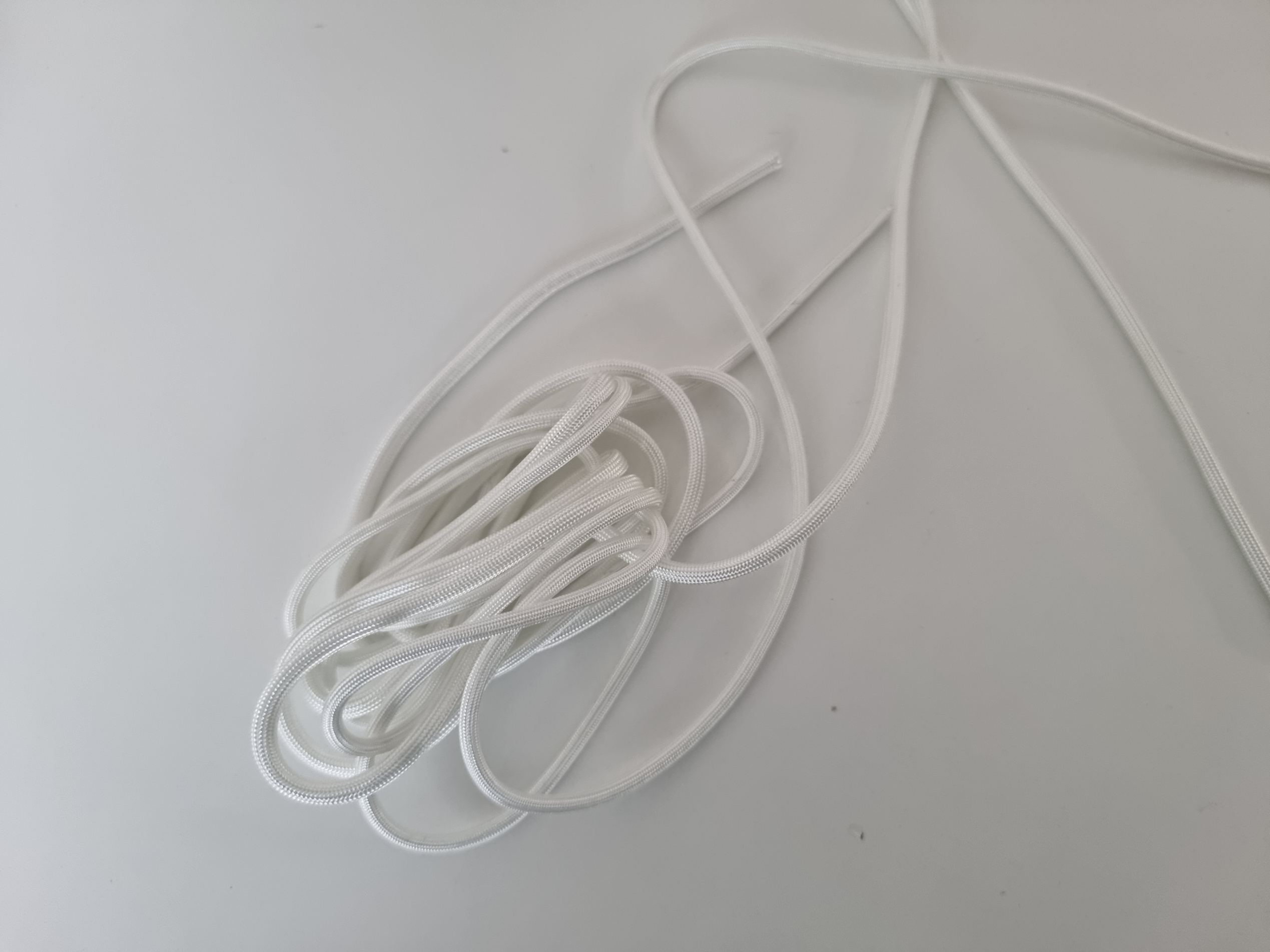
Guaina in Fibra di Vetro per Bobina
Avvertenza: Per evitare eventuali Cortocircuiti coprire la Bobina mediante una Guaina in Fibra di Vetro in grado di resistere fino a 600°C.
Nota: Le Operazioni di Ricottura sull'Ottone producendo un eccessivo Riscaldamento richiedono l'uso di un Sistema di Raffreddamento a Liquido.
Senza un Sistema di Raffreddamento si avrà la sola Brasatura dell'Ottone.
Alcuni Kit vengono forniti a corredo con Tubo in PVC, Sezione Max da 4mm lunghezza di circa 2 metri, da utilizzare in combinazione con una Pompa.
La Scheda, realizzata su un Circuito Stampato a Doppia Faccia, presenta piste in rame maggiorate per garantire una migliore efficienza al Circuito Risonate.
Con l'uso intensivo aggiungere una Ventola Supplementare per il Raffreddamento sui Condensatori di Risonanza.
Il Volume Massimo riscaldabile all'Interno della Bobina non dovrà eccedere 1/5 del Volume o presentare un Diametro Inferiore di 1/3 rispetto alla Bobina al fine di non incorrere in un sovraccarico nel Circuito di Alimentazione.
Al fine di evitare problemi si consiglia di applicare un Amperometro per monitorare la Corrente Assorbita.
La Scheda PCB dispone di un Dissipatore in Alluminio ad alta efficienza con spessore maggiorato a 8,5mm e Sistema per il Fissaggio della Bobina con Supporti da M4.
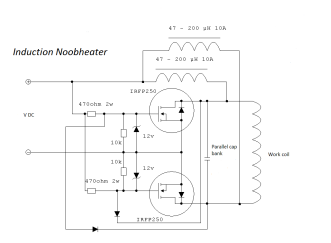
Diagramma Scheda PCB
Caratteristiche Tecniche della Scheda PCB:
- Tensione di Funzionamento: DC 24-36V
- Corrente di Lavoro: Maggiore di 15A Minore di 30A (Alimentatore Consigliato 24V 15A 350W)
- Stadio di Potenza: IRFP260N (50A 200V)
- Potenza d'Uscita: compresa fra 350W e 500W
- Dimensioni: 100 x 100 x 85mm
- Dimensione Bobina in Rame: Diametro Interno 40mm/1,57", Altezza 45mm
- Diametro Crogiolo in Grafite: 30x30mm o 30x40mm;
- Diametro Interno: 35mm.
Avvertenza: Prestare molta attenzione nel Cablaggio fra Anodo & Catodo sulla Scheda PCB poiché un eventuale Errore potrebbe causare un incendio.
Inoltre collegare la Bobina in Rame prima di alimentare la Scheda PCB per evitare la formazione di un Arco Elettrico.
Nota: Con Alimentazione a Batteria utilizzare un Circuito di Protezione per limitare l'Assorbimento Massimo della Corrente a 23A.
Rapporto fra Corrente Assorbita & Dissipazione Termica ulla Scheda PCB:
- 00 ≥ 35 ℃ ≈ 30A
- 35 ≥ 45 ℃ ≈ 27A
- 45 ≥ 55 ℃ ≈ 25A
- 55 ≥ 65 ℃ ≈ 23A
- 65 ≥ 75 ℃ ≈ 20A
Al fine di migliorare l'efficienza della Scheda PCB consiglio la sostituzione della Bobina in Rame, fornita a corredo, con un Tubetto in Rame avente un Diametro Esterno compreso fra 3 o 4 mm.
Avvertenza: La Bobina non dovrà presentare un Diametro (D) non Superiore a 1+1/8" (30 mm) e una Proporzione fra Diametro & Altezza prossima a 1.
Prima di procedere alla realizzazione della nuova Bobina calcoliamo la Frequenza di Risonanza (fr) derivandola dalla Bobina Originale fornita a corredo con la Scheda PCB, utilizzando la seguente formula:
L = 0.001*n*2*D/((228*D/2) + 254*l)
Dove:
- L = Induttanza del Circuito di Risonanza in H;
- n = Numero di Spire sulla Bobina,
Bobina Originale n.6 Spire; - D = Diametro della Bobina in mm (misurato al Centro del Conduttore),
Bobina Originale 45mm; - l = Lunghezza (Altezza) della Bobina in mm,
Bobina Originale 29 mm.
Applicando la Formula avremo un'Induttanza (L) di 1.456 mH che ci consentirà di calcolare le Caratteristiche della nuova Bobina e la Frequenza di Risonanza (fr) sulla Scheda PCB.
fr=1/(2*pi*sqrt(L*C))
Dove:
- fr = Frequenza di Risonanza in Hz;
- C = Capacità Totale del Circuito di Risonanza in F,
n.4 Condensatori da 0.33 uF per una Capatità Totale sulla Scheda PCB di 1.32 uF; - L = Induttanza del Circuito di Risonanza in H,
Induttanza nella Bobina Originale 1.256 mH.
Applicando la Formula avremo una Frequenza di Risonanza (fr) di circa 115 KHz (114.80 KHz).
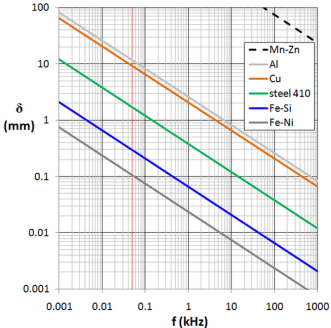
Rapporto Frequenza di Risonanza/Spessore
Nei Dispositivi Professionali la Frequenza di Risonanza (fr) risulta Inferiore rispetto alla Scheda PCB utilizzata nel progetto poiché una Minore Frequenza consente, a parità di Potenza, una migliore efficienza; i valori tipici sono:
- Ez-Annealing: 110 Khz a 600 W;
- Annie: fra 50 Khz e 90 Khz a 1200 W in ragione al Tipo di Bobina (Standard o Ferrite).
Applicando la Formula inversa procediamo al calcolo della nuova Bobina da utilizzare sulla Scheda PCB:
L = 0.001*n*2*D/((228*D/2) + 254*l)
Dove:
- L = Induttanza del Circuito di Risonanza in H,
Induttanza 1.456 mH - n = Numero di Spire sulla Bobina;
- D = Diametro della Bobina in mm (misurato al Centro del Conduttore),
Nuova Bobina 30 mm; - l = Lunghezza (Altezza) della Bobina in mm,
Nuova Bobina Originale 27.50 mm.
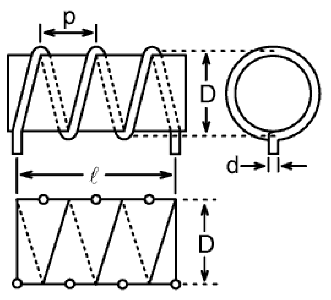
Caratteristiche della Bobina
Avendo utilizzato un Tubetto in Rame da 3 mm (d) ricoperto da una Guaina in Fibra di Vetro avremo un Diametro di circa 3.35 mm di conseguenza la Bobina presenterà le seguenti caratteristiche:
- Diametro (D) pari a 30.00 mm;
- Numero di Spire (n) pari a 8 Spire;
- Altezza (l) pari a 27.50 mm.
Attraverso queste Formule abbiamo calcolato le Caratteristiche per una Bobina perfettamente accordata alla Frequenza (fr) sulla Scheda PCB in grado di mantenere l'assorbimento di Corrente nei Parametri di Progetto impedendo un eccessivo surriscaldamento.
Avvertenza: Il Numero di Spire o una Ridotta separazione fra le Spire aumenterà la Densità del Campo Magnetico; la Separazione non dovrà mai eccedere la metà del Diametro della Spira mentre l'Altezza Massima della Bobina non dovrà mai eccedere il doppio del suo Diametro.
Nota: Il rapporto ottimale fra Diametro & Altezza in una Bobina a Singola Spira dovrebbe tendere sempre a 1:1 in questo modo la Corrente Assobità sarà concentrata in una Area ristretta.
Nelle Bobine di Grosse Dimensioni, l'Altezza non dovrà mai superare la metà del suo Diametro.
All'Aumentare del Diametro il rapporto si riduce di conseguenza una Bobina con Diametro da 2” potrà avere un Altezza Massima di 0,75” mentre con un Diametro di 4” un Altezza Massima di 1”.
Quando l'Altezza della Bobina eccede 4 o 8 volte il suo Diametro non sarà possibile garantire un riscaldamento uniforme; in tale situazione viene immergere l'Oggetto nella Bobina (Sistema a Scansione).
La Distanza per un corretto Accoppiamento (Distanza Oggetto - Bobina) dipende: dal Tipo di Riscaldamento (Statico o a Scansione) e dal Tipo di Materiale in lavorazione (Ferroso o Non Ferroso).
Nel riscaldamento superficiale di tipo Statico si raccomanda una Distanza di Accoppiamento di 0,060" (1.5 mm) mentre nel riscaldamento a Scansione viene raccomandata una distanza di 0,075" (1.9 mm) per garantire una buona Tolleranza fra il Pezzo e la Bobina.
In presenza di Materiali Magnetici, le Distanze di Accoppiamento possono essere dilatate da 0,25” a 0,38” (6.4 mm a 9.5 mm) mentre in presenza di Superfici Non Lineari la Distanza di Accoppiamento dipenderà dal Profilo.
Con Alte Frequenze di Risonanza, le Correnti saranno Ridotte, di conseguente sarà necessario Aumentare l'Accoppiamento.
Mentre con Frequenze Medie o Basse, le Correnti saranno Superiori di conseguenza sarà necessario Ridurne l'Accoppiamento.
Nella maggior parte dei casi, la Distanza di Accoppiamento Aumenta in proporzione al Diametro dell'Oggetto; i valori tipici sono:
- Con Distanza di Accoppiamento di 0.75” (19 mm) Diametro dell'Oggetto pari a 1.5” (38 mm);
- Con Distanza di Accoppiamento di 1.25” (32 mm) Diametro dell'Oggetto pari a 4” (102 mm);
- Con Distanza di Accoppiamento di 1,75” (44 mm)Diametro dell'Oggetto pari a 6” (152 mm).
Nelle Bobine il Campo Elettromagnetico viene solitamente influenzato dalla Sezione Trasversale o dalla Massa dell'Oggetto di conseguenza le Bobine non dovranno mai eccedere la Lunghezza del Oggetto perché le Spire che si estendono oltre le estremità daranno luogo ad un maggiore riscaldamento.
Per impedire un eccessivo riscaldamento alle Estremità, la Bobina dovrà presentare, oltre ad una Minore Lunghezza, un Profilo con un Diametro Maggiore alle estremità rispetto alla Sezione Centrale perché la Riduzione dell'Accoppiamento eviterà un eccessivo riscaldamento in quell'Area Specifica.
Solitamente il Campo Elettromagnetico applicato in fori e scanalature tenderà a generare un eccessivo riscaldamento di conseguenza, al fine di evitare l'insorgere di questa problematica, vengono utilizzati degli Inserti in Rame in grado di mitigare il fenomeno riducendo la possibile distorsione dei fori in fase di raffreddamento.
Con la presenza di tagli e scanalature lungo la superficie in lavorazione, nella Bobina sia avrà un maggiore assorbimento di corrente rispetto ad una superficie lineare con un conseguente aumento di temperatura.
Nel caso in cui due Oggetti vengano riscaldati dalla medesima Bobina potrebbe accadere che, il Campo Magnetico generato dalle Spire Adiacenti, vada a sovrapporsi causando un eccessivo riscaldamento.
Per evitare questo Problema parte delle Spire dovranno essere avvolte nella Direzione Contraria in questo modo il Campo Intermedio sarà in grado di mitigare il fenomeno.
Un altra possibile soluzione consiste nel Cortocircuitare le Spire Attive in questo modo il Corto consente la Riduzione del Campo Magnetico in eccesso.
In presenza di Corto fra le Spire sarà necessario predisporre un Sistema di Raffreddamento a Liquido adeguato per Dissipare il Calore.
La Soluzione con Bobine in Corto viene solitamente utilizzata per impedire un eccessivo Riscaldamento in Bobine di Grosse Dimensioni in cui il Campo Magnetico potrebbe riscaldare anche le strutture adiacenti.
Il Numero di Cortocircuiti sulle Bobine vengono comunemente calcolati in Fase di Calibrazione in questo modo eventuali Giri Supplementari saranno facilmente Aggiunti o Rimossi mediante l'applicazione di Graffette in Rame.
A causa della Ridotta Resistenza & Alta Conduttività il Rame viene solitamente utilizzato per la fabbricazione delle Bobine.
Tali Tubi in Rame, tipicamente di Forma Circolare, sono disponibili sul Mercato con un Diametro Minimo di 0,125” (3.2 mm) in modo da consentire la realizzazione di un Sistema di Raffreddamento a Liquido.
Tipicamente una Bobina presenta una Perdita di 12R (Copper Loss) imputabile alla Resistività del Rame.
Qualora la Bobina non disponga di un adeguato Sistema di Raffreddamento la Resistività del Rame potrebbe aumentare in ragione alla Calore assorbito dall'Oggetto in Lavorazione.
Con il Termine “Copper Loss” viene comunemente indicato il Calore prodotto dalle Correnti Elettriche negli Avvolgimenti dei Trasformatori di conseguenza un Trasferimento Indesiderato di Energia darà origine a Correnti Indotte.
In Bobine di Grosse Dimensioni potrebbe essere necessario, al fine di realizzare un Sistema di Raffreddamento Efficiente, spezzare l'Impianto in varie Sezioni.
I fattori che influenzano la scelta, relativamente alla Sezione del Tubo in Rame nella Bobina, dipende: dalla Correte, dalla Frequenza di Risonanza e dalla Resistività del Rame.
Per determinare lo Spessore del Rame, in relazione alla Frequenza, fate riferimento alla seguente Tabella:
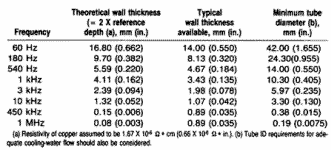
Tabella Spessore/Frequenza
La limitata Perdita di Efficienza nella Bobina consente l'uso di Tubi aventi uno Spessore fino a 2 volte inferiore rispetto ai valori di progetto.
L'uso di Tubi con Sezione quadrata offreno il vantaggio di un migliore Accoppiamento fra le Spire oltre ad una migliore Sagomatura sulla Bobina.
In Fase di Sagomatura della Bobina il Rame deformandosi potrebbe Incrudirsi di conseguenza, al fine di evitarne la rottura, procedere alla Ricottura.
In presenza di Sagomature Complesse riempire il Tubo con Sabbia o Sale per prevenirne il Collasso.
Nella Produzione Industriale l'uso di Leghe con Punto di Fusione inferiore ai 212°F (100°C) sono spesso utilizzate in sostituzione a Sabbia o Sale.
In presenza di Correnti Elettriche estremamente elevate potrebbero svilupparsi delle Forze Elettromagnetiche in grado di causare lo spostamento della Bobina.
Procedere eventualmente al Rinforzo delle Spire per evitarne il Cortocircuito o la Modifica del Profilo sulla Bobina.
In presenza di Circuiti con Risonanza a Bassa Frequenza, la Bobina potrebbe generare un Rumore Acustico come avviene in un Altoparlante; per limitare il fenomeno procedere al Rinforzo delle Spire.
Nelle Bobine ad Alta Tensione, fino a 12000V, l'Isolante utilizzato per Rinforzo deve soddisfare, oltre alle Caratteristiche Elettriche della Scheda PCB, il Profilo della Bobina e Calore Irradiato dall'Oggetto.
Per garantire una maggiore Rigidità & Protezione procedere alll'incapsulamento della Bobina in un Materiale Plastico o Refrattario in grado di soddisfare le esigenze di Isolamento Termico ed Elettrico.
Nelle Applicazioni a Bassa Temperatura vengono comunemente utilizzate delle Resine Epossidiche mentre per le Alte Temperature dei Materiali Refrattari come la Ceramica.
Poichè la Bobina utilizzata nel nostro progetto non necessità di Cavi di Alimentazione per Lavorazioni a Distanza dalla Scheda PCB non saranno prese in considerazione le problematiche relative ad Isolamento & Dimensionamento.
Con Bobine ad Elevata Induttanza (Numero di Spire o Diametro), la Lunghezza dei Cavi di Alimentazione risulterà meno critica di conseguenza sarà buona norma mantenere una Spaziatura Sufficiente per evitare l'innesco dell'Arco Elettrico.
Nei Sistemi a Bassa Tensione, Inferiore agli 800V, vengono solitamente utilizzati dei Tubi di Rame con Raffreddamento a Liquido, Isolamento ad Aria e Rinforzi in Nylon per Distanziare le Spire in modo da garantire la massima efficienza.
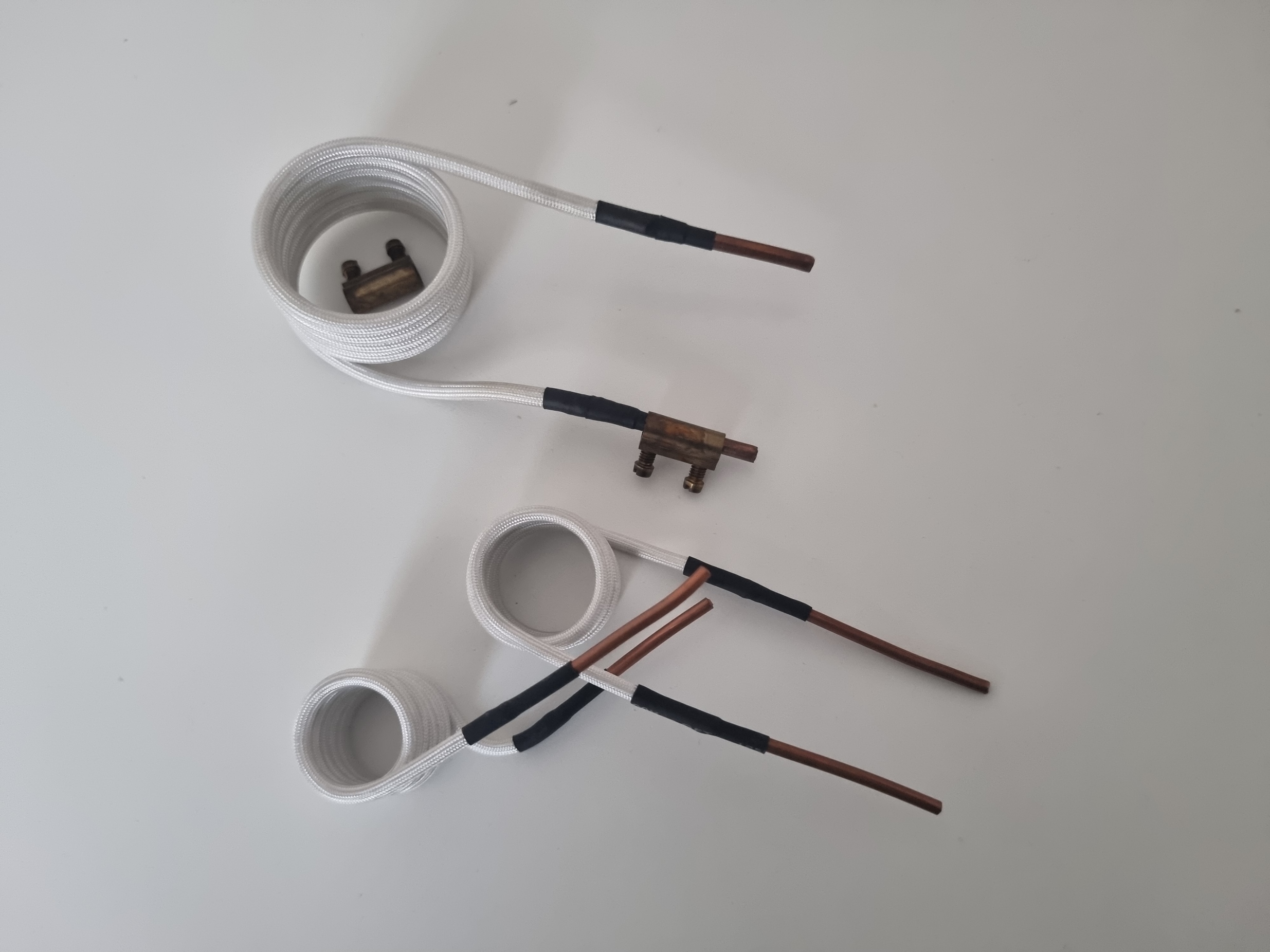
Bobine Standard Isolate con Guaina in Fibra di Vetro
In presenza di un Alimentatore senza Circuito di Protezione ricoprire le Spire della Bobina con una Guaina in Fibra di Vetro per prevenire il danneggiamento della Scheda PCB in caso di contatto accidentale con gli Oggetti in Lavorazione.
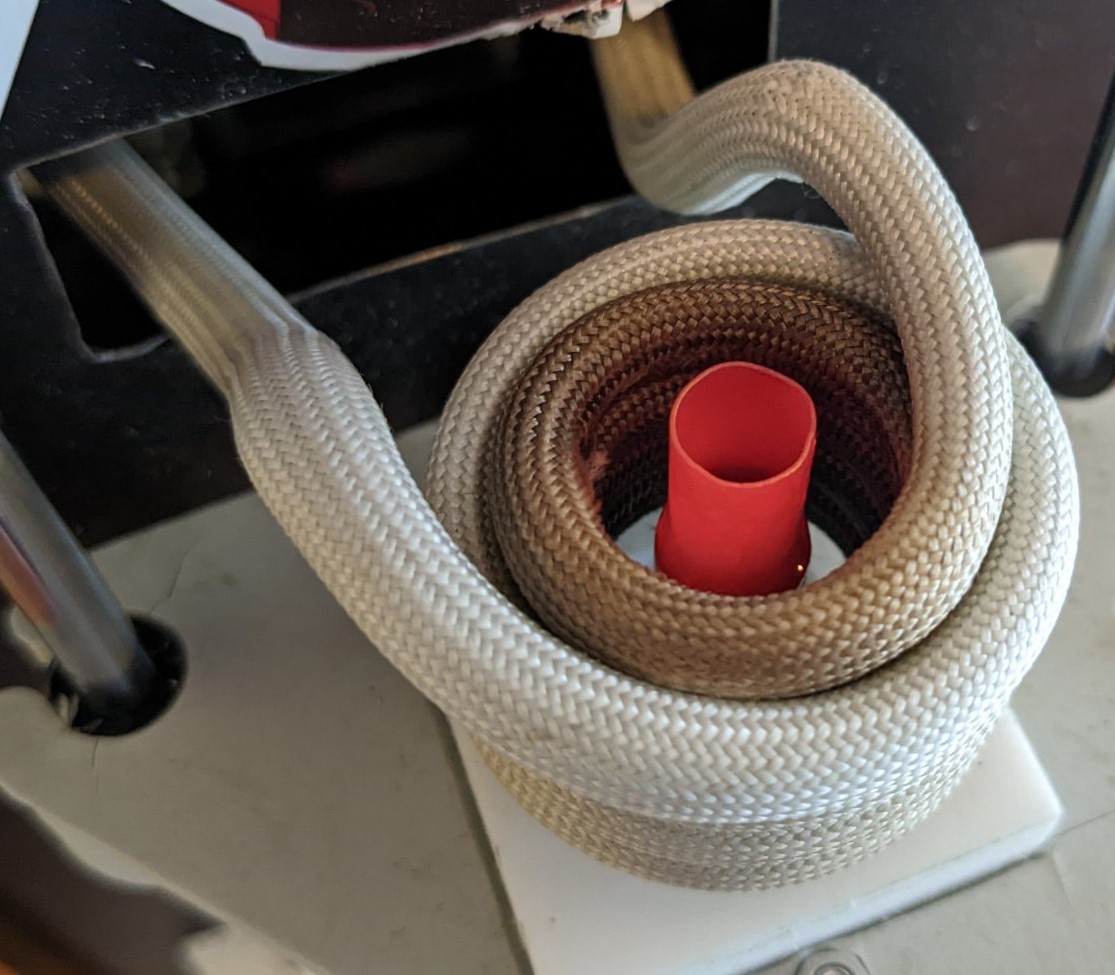
Bobina Isolata con Doppio Avvolgimento
Al fine di incrementarne le prestazioni sostituire la Bobina Standard con un Modello a Doppio Avvolgimento.
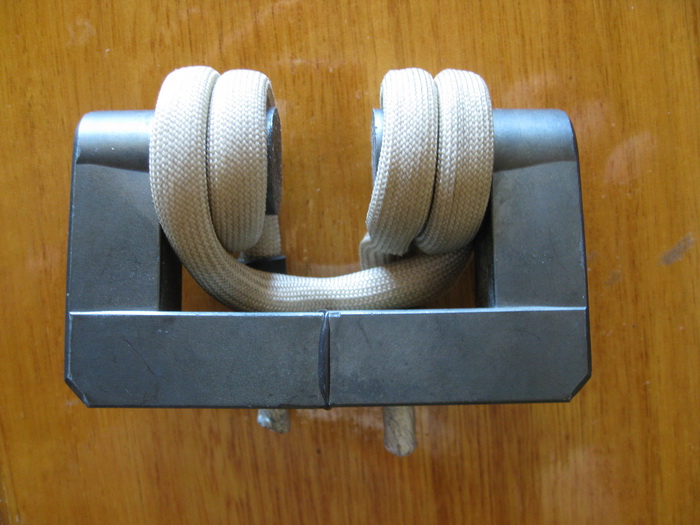
Bobina Isolata con Nucleo di Ferite
In alternativa alla Bobina a Doppio Avvolgimento utilizzare un Modello con Nucleo Ferro Magnetico.
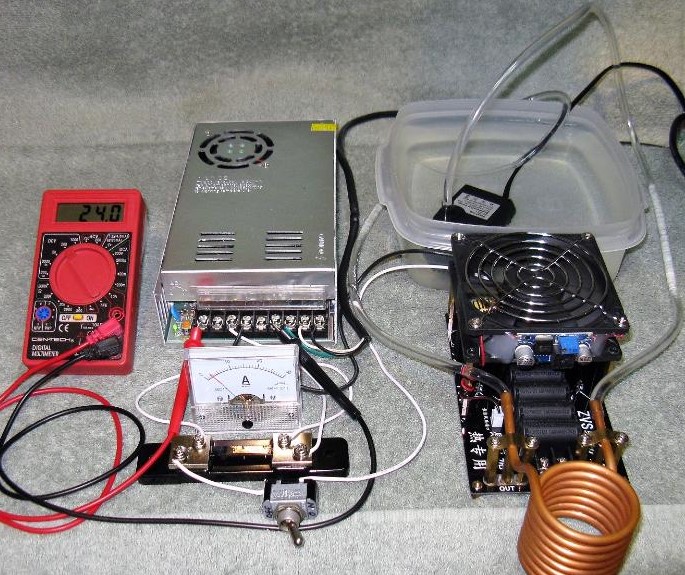
Prototipo in Fase di Test
Alla luce delle considerazioni espresse nei Paragrafi precedenti ho realizzato un Prototipo per testare i componenti Base: Alimentatore 36V DC 20A & Scheda PCB.
Durante questa fase ho implementato un semplice Circuito di Raffreddamento utilizzando una Pompa per Acquari al fine garantire una protezione alla Scheda PCB.
Per il Monitoraggio della Tensione ho utilizzato un Tester mentre per la Corrente ho utilizzato un Circuito con shunt.
In questa fase ho verificato l'efficienza del Sistema testando ripetutamente vari Metalli prima di utilizzare Bossoli in Ottone.
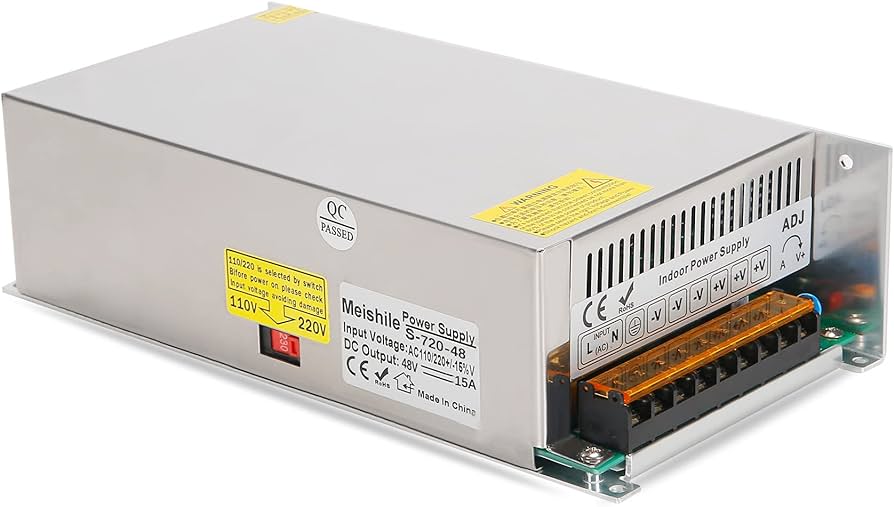
Alimentatore 48V 15A
Durante le Operazioni di Ricottura su Bossoli in Ottone ho riscontrato un dilatamento dei Tempi rispetto a Sistemi con Alimentazione a 48V.
La scelta conservativa a 36V potrebbe risultare inefficiente in presenza di Intense Operazioni di Ricottura.
In tale Fase ho potuto acquisire alcuni dati fondamentali per la Calibrazione dell'Annealer in relazione a Bossoli di Vari Calibri, come:
- Profondità di Immersione nella Bobina per la Ricottuta del Colletto;
- Tempo di Ricottura in relazione al Calibro;
Per un uso intensivo della Annealer utilizzare una Scheda PCB ottimizzata per la Ricottura dell'Ottome al fine di prevenire problemi di Surriscaldamento.
Al termine della Fase di Test sulla Scheda PCB ho iniziato la progettazione dell'Annealer utilizzando come base di partenza il seguente Diagramma Funzionale:
Partendo da questo Diagramma ho compilato uno Schema Elettrico Semplificato.
In Fase di progettazione ho deciso di realizzare un Annealer che potesse sopperire alle mie esigenze.
Pur avendo predisposto il Dispositivo per l'Upgrade al Sistema Auto-Feed utilizzo un Sistema di Alimentazione Manuale in grado di garantire una maggior Controllo e una migliore Qualità.
Alla luce di queste considerazioni ho compilato un secondo Schema Elettrico.
Per le Operazioni di Ricottura sul Colletto risulta fondamentale il Controllo del Tempo di conseguenza sarà necessario utilizzare un Timer per la gestione della Scheda PCB.
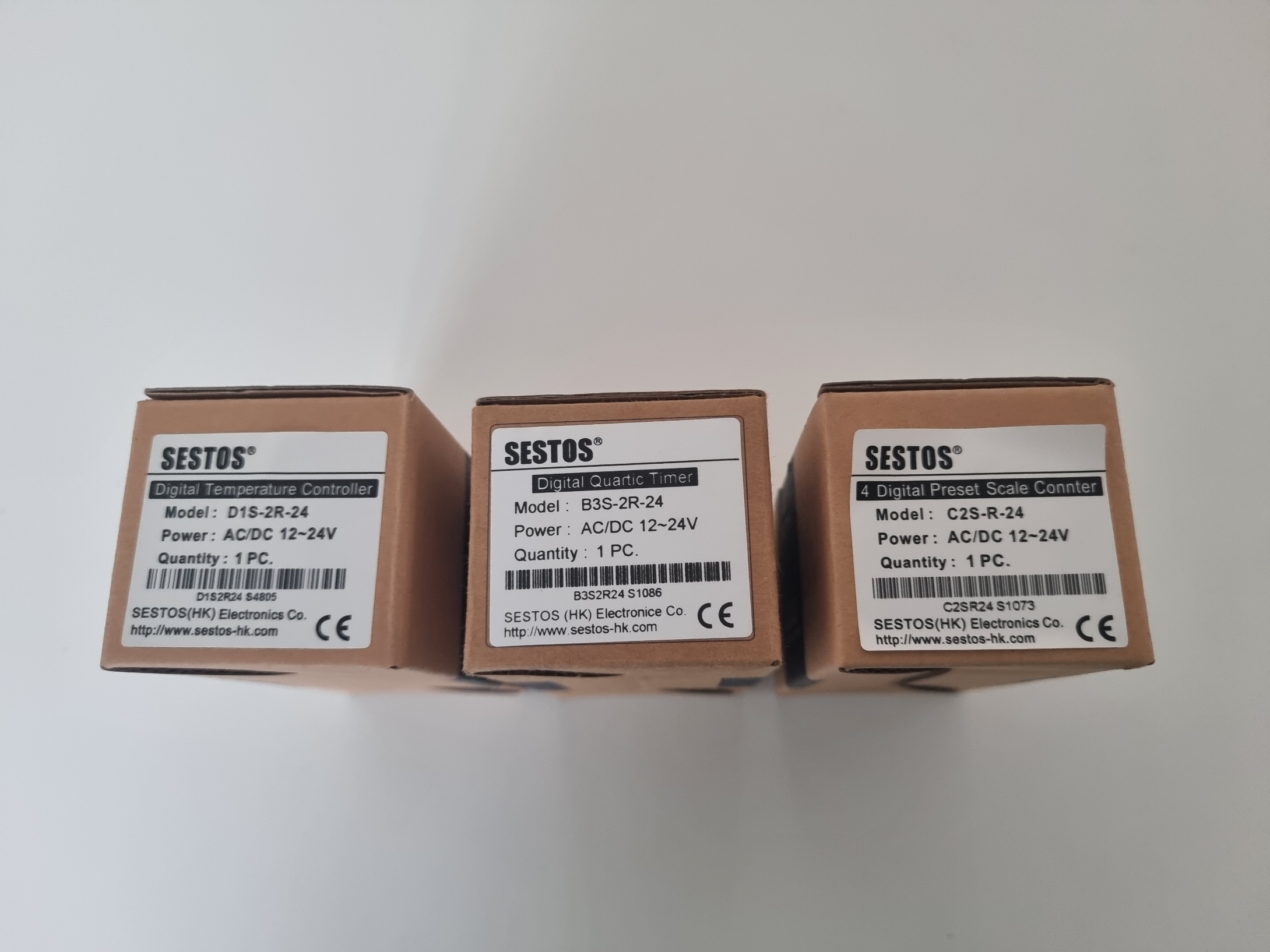
Sestos Timer - Counter - Temperature Control
In questo Progetto un Singolo Timer Industiale della Seatos Modello B3S-2R-24 consentirà di controllare l'intero Processo.
Il Modello in questine Integra n.4 Timer Indipendenti: A, B, C e D; in cui solo i Timer A & C sono equipaggiati con un Relè SPDT.
Questi Timer verranno utilizzati per svolgere le seguenti Funzioni:
Timer A:
Tempo di Ricottura
Controllo Alimentazione Scheda PCB con un Relè di Potenza.
Timer B:
Sistema Auto Feed
Ritardo Ciclo di Caricamento Bossili Sistema Auto Feed.
Impostato a "0" con il Sistema di Caricamento Manuale.
Timer C:
Scarico & Carico Bossoli
Controllo Solenoidi per i Sistemi di Scarico e/o Carico dei Bossoli; impostazione di base a .5 Secondi.
Non collegare i Solenoidi in Modo Diretto al Timer senza l'uso di un Relè.
Applicare ad ogni Solenoide un Diodo Protezione Tipo 1N4007.
Con il Sistema Auto Feed sarà solitamente utilizzato un solo Solenoide (Scarico Bossoli).
Timer D:
Tempo di Caricamento
Ritardo Ciclo di Caricamento; solitamente impostato fra 2,5 e 3,0 Secondi.
Il Timer controlla il Ritardo necessario all'Operatore per il Caricamento Manuale del Bossolo nella Bobina
In Modalità Auto l'Operazione avverrà in Modo Sequenziale.
Il Sistema di Raffreddamento sulla Bobina utilizza una Pompa 12V DC per PC dotata di Serbatoio a Loop Chiuso.
Avvertenza: Utilizzare un Refrigerante specificò per Radiatori poiché l'acqua vaporizzandosi a 100°C potrebbe creare problemi.
Sulla Scheda PCB Bobina saranno usati in combinazione diversi Sistemi di Raffreddamento:
A. Sistema a Liquido per Bobina & Scheda PCB:
1. Circuito Principale: costituito da:
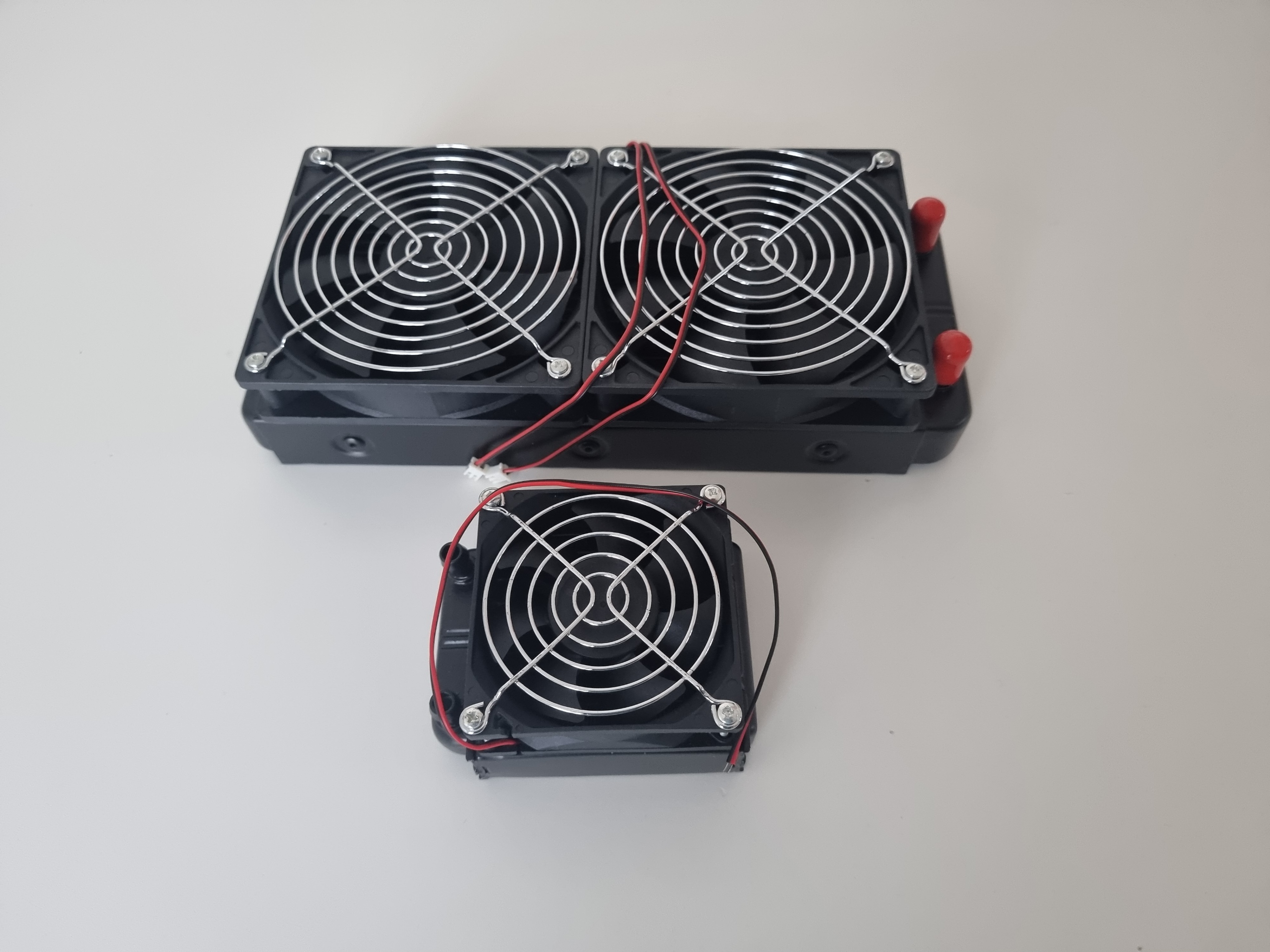
Scambiatore Principale da 240 mm & Secondario da 90 mm
a. Scambiatore 240 mm equipaggiato con n.2 Ventole Tachimetriche da 120x120.
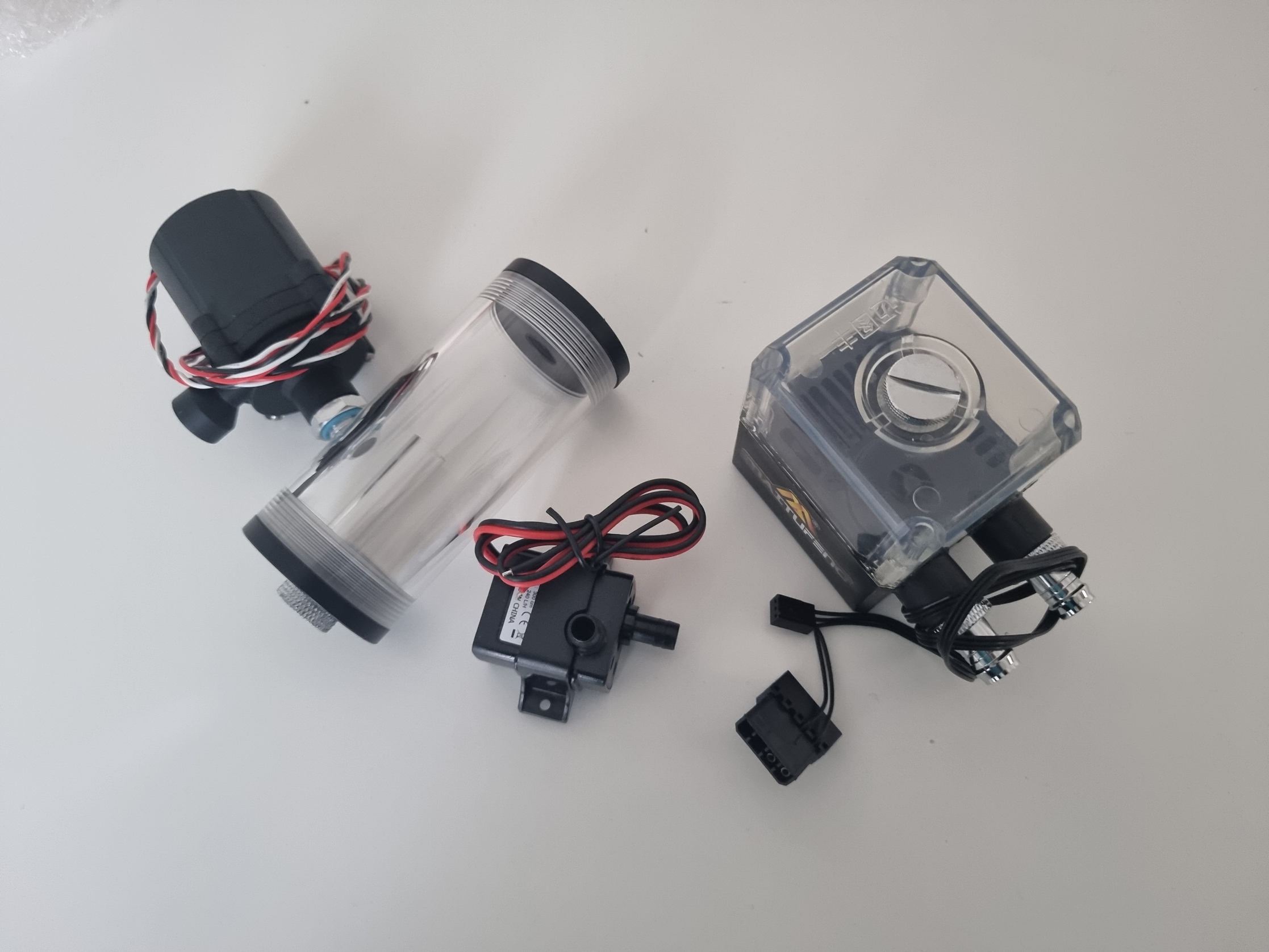
Gruppo Principale da 800 l/h con Pompa PCB & Gruppo Secondario da 650 l/h
b. Pompa di Ricircolo da 800 l/h con Serbatoio.
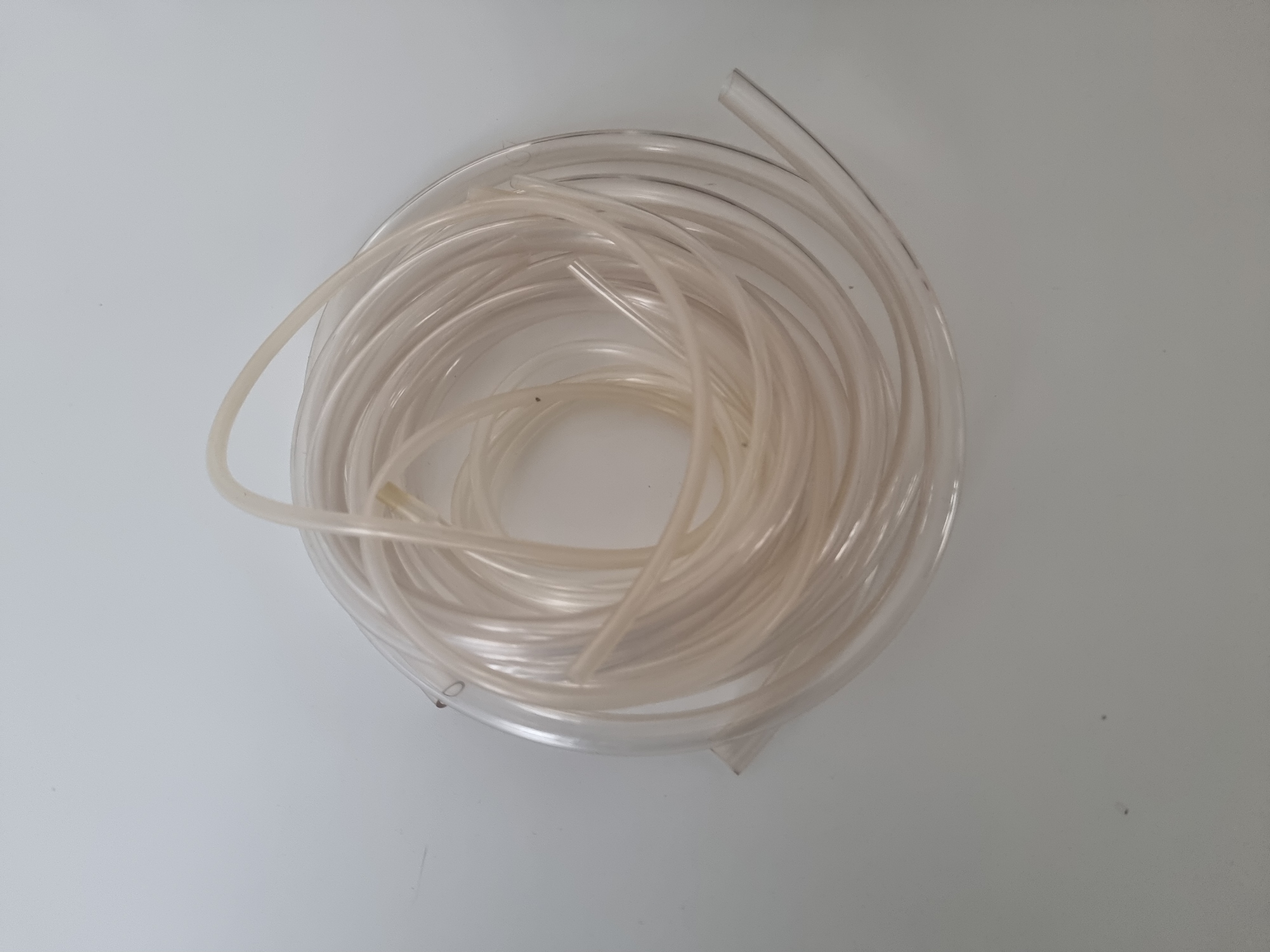
Gruppo Principale da 800 l/h con Pompa PCB & Gruppo Secondario da 650 l/h
Gli Elementi del Circuito Principale sono raccordati fra loro mediante un Tubo in PVC da 9.5 mm ad eccezione della Bobina dove sarà utilizzato un Tubetto da 4 mm.
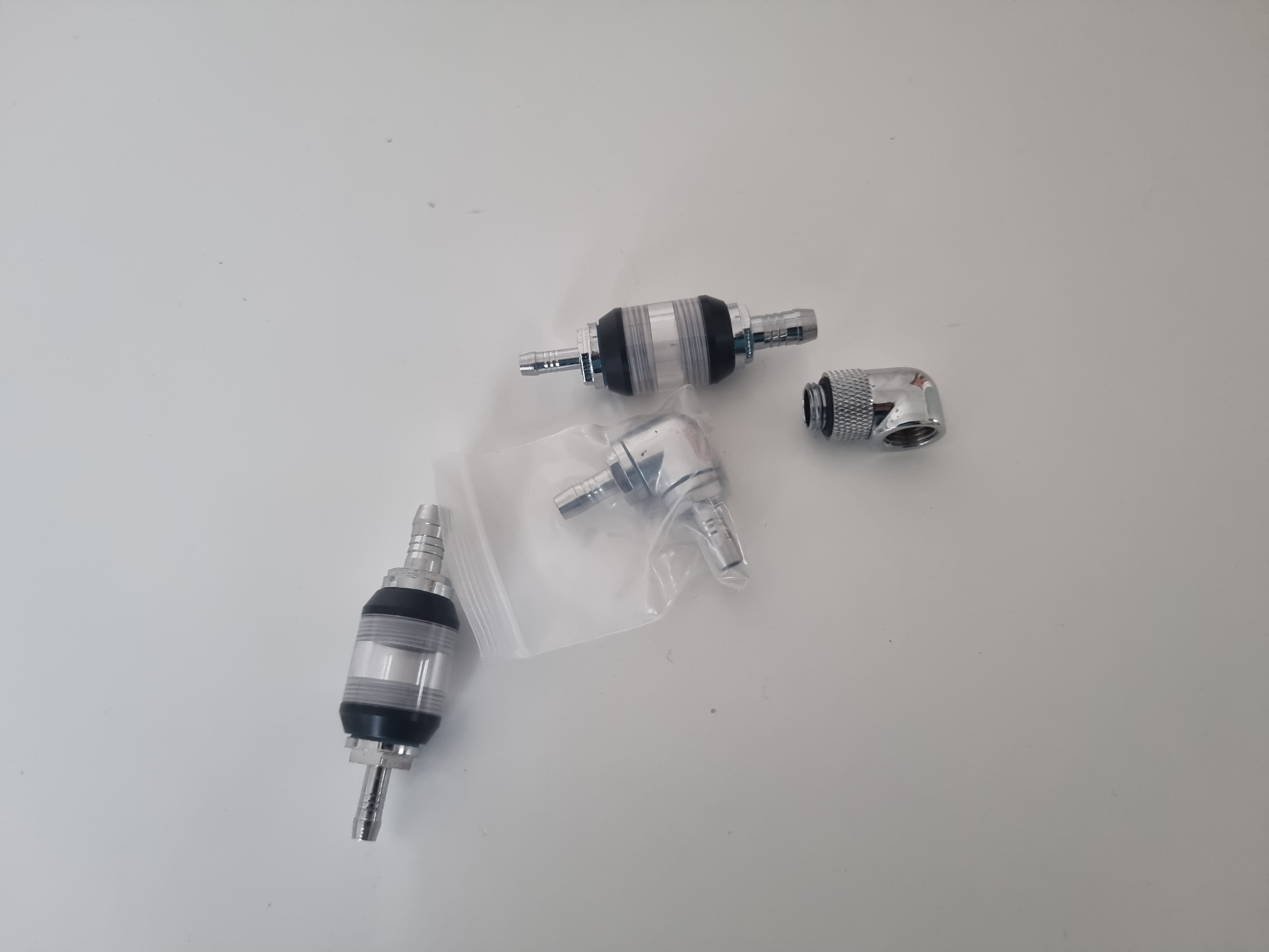
Raccordi di Transizione per Tubi in PVC da 4mm a 9,5mm
Per realizzare la Transizione fra Tubi in PVC da 4mm a 9,5mm ho utilizzato degli Speciali Raccordi con Indicatore di Flusso.
2. Circuito Secondario: costituito da:
a. Scambiatore da Scambiatore 90 mm equipaggiato con Ventola Tachimetrica da 90x90.
b. Pompa di Ricircolo da 650 l/h con Serbatoio.
Per migliorare il Raffreddamento sui Condensatori, ho applicato un Dissipatore 40x40 mentre sulla Scheda PCB (Lato Saldature) un Dissipatore 40x80 con Ventola Tachimetrica da 90x90 ed Aletta Dissipatrice 100x100.
Tali Dissipatori, integnando la Ventola presente dalla Scheda PCB, consentono incrementare la Dispersione Termica.
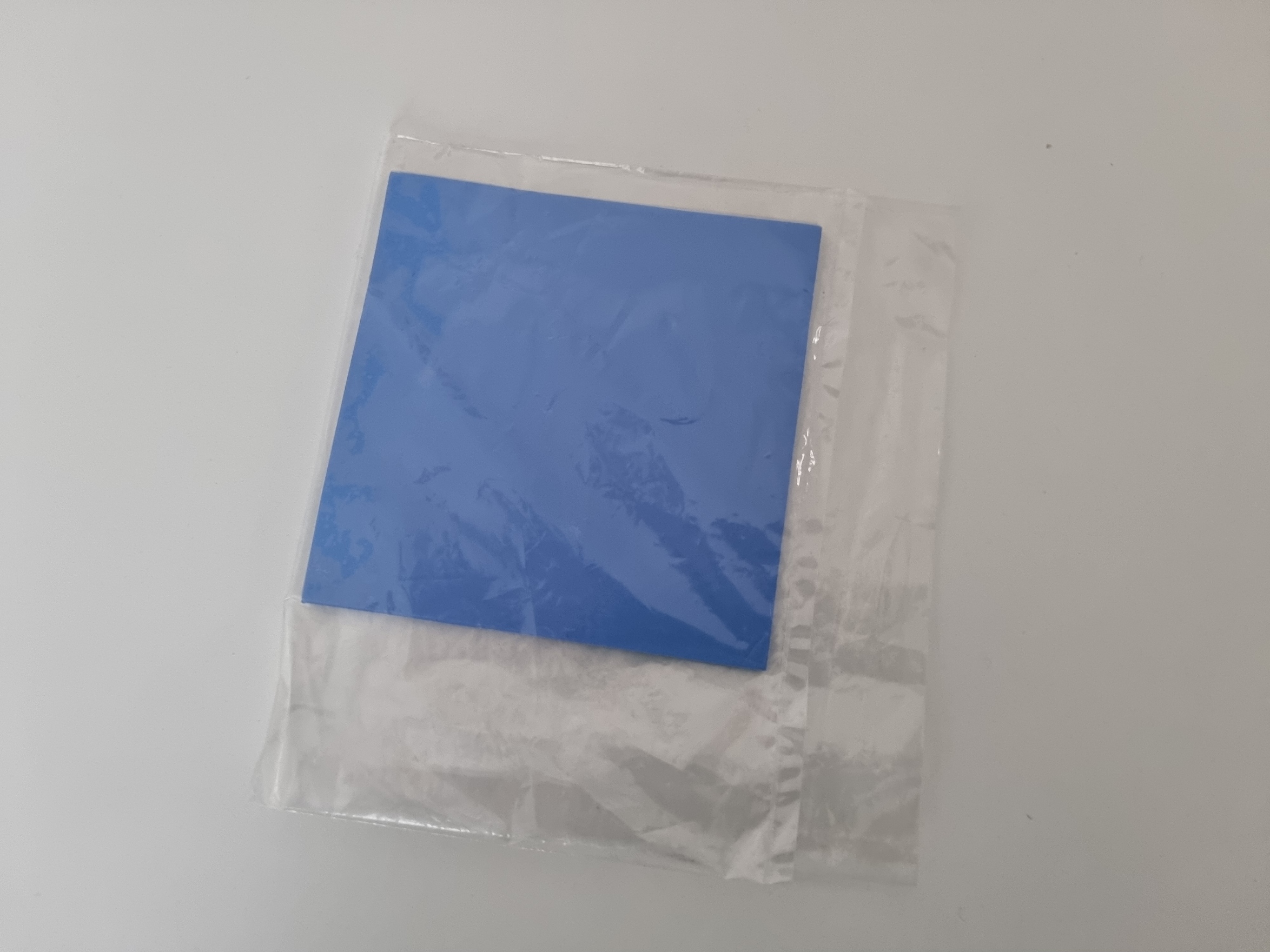
Tappetino Termo - Conduttivo
Nota: Per favorire la Dissipazione Termica fra gli Elementi del Sistema applicare un Tappetino Termo - Conduttivo in Silicone.
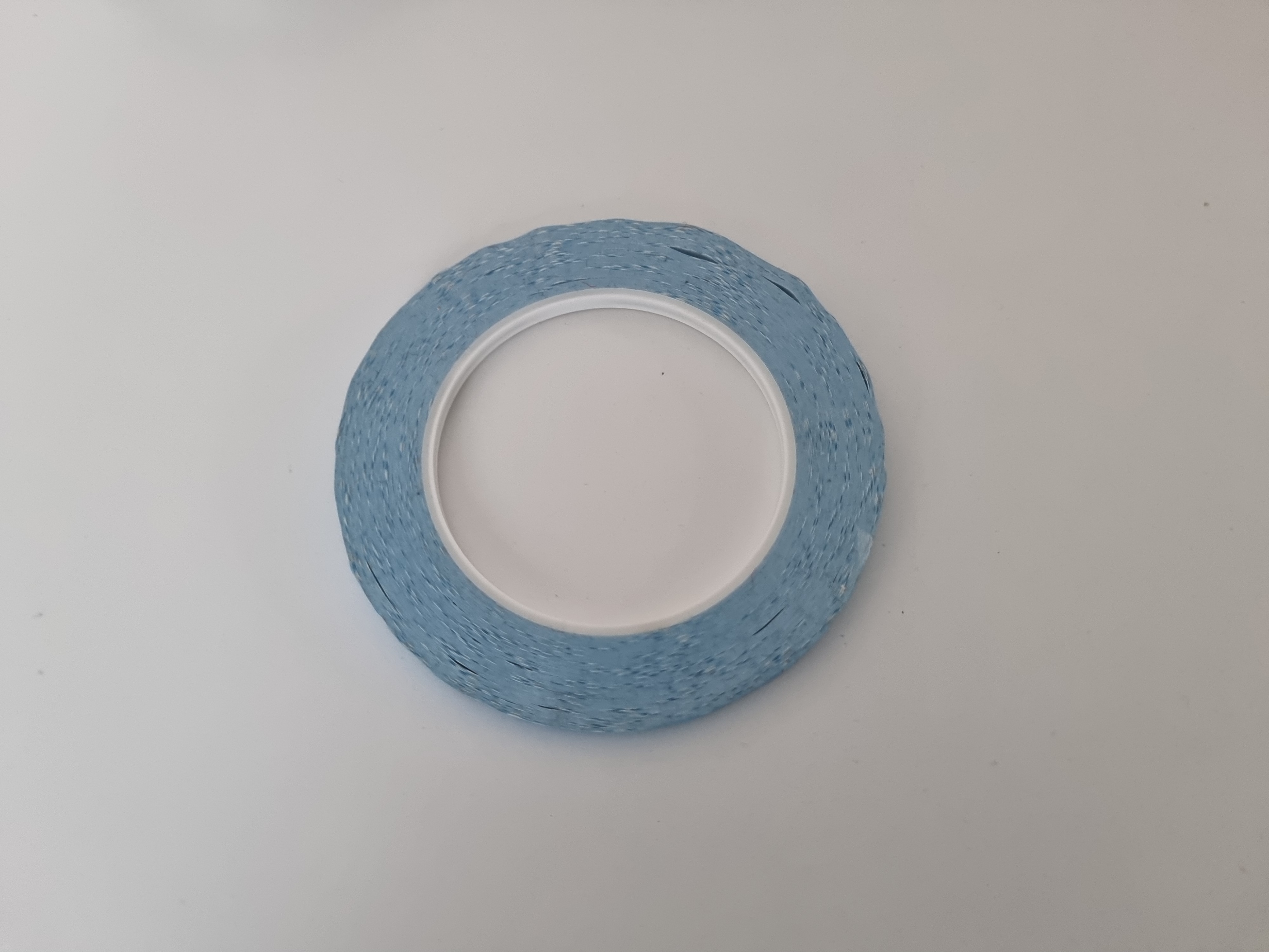
Nastro Adesivo Termo - Conduttivo
In alcune situazioni, in sostituzione del Tappetino, utilizzare un Nastro Adesivo Termo Conduttivo.
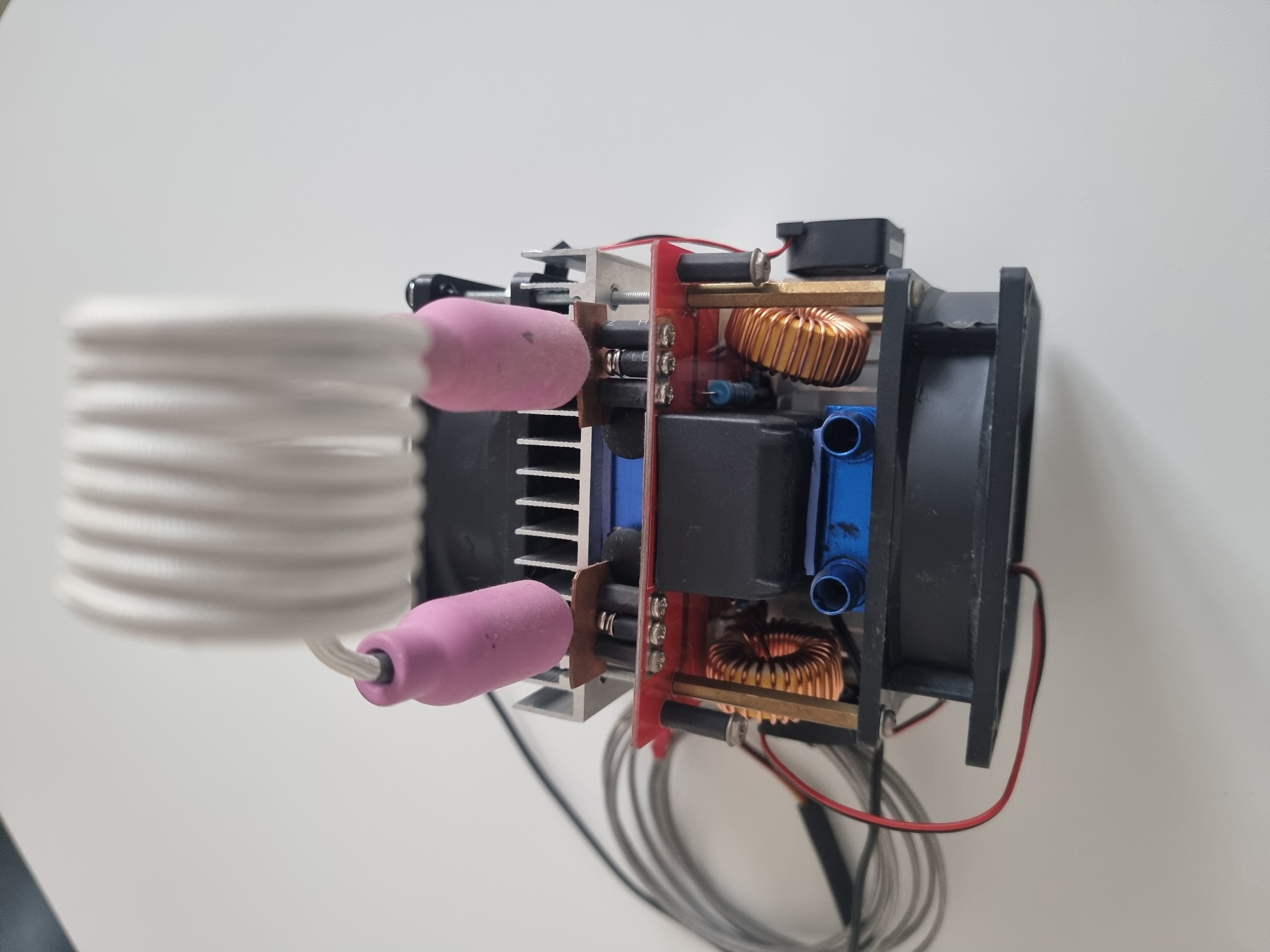
Dissipatore sulla Scheda PCB per Condensatori
1° Dissipatore per il Raffreddamento dei Condensatori.
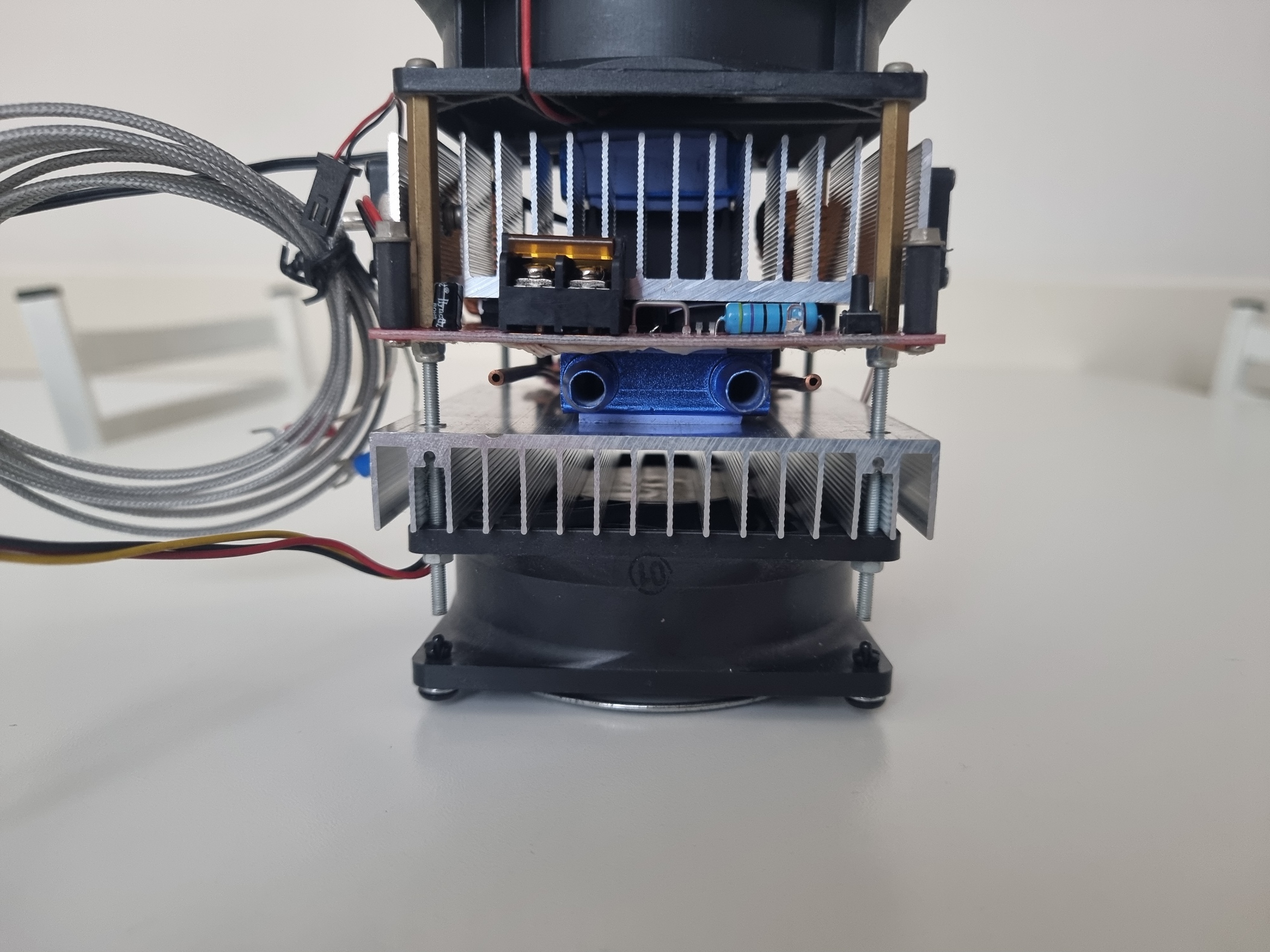
Dissipatore sulla Scheda PCB per Condensatori & MOSFET
2° Dissipatore per il Raffreddamento dei MOSFET & Condensatori.
Collocato sulla Scheda PCB (Lato Saldature) sarà integrato da un'Aletta Dissipatrice 100x100 con Ventola da 90x90 attiva in Fase di Ricottura.
Nota: Gli Elementi del Circuito Secondario sono raccordati fra loro mediante un Tubo in PVC da 9.5 mm.
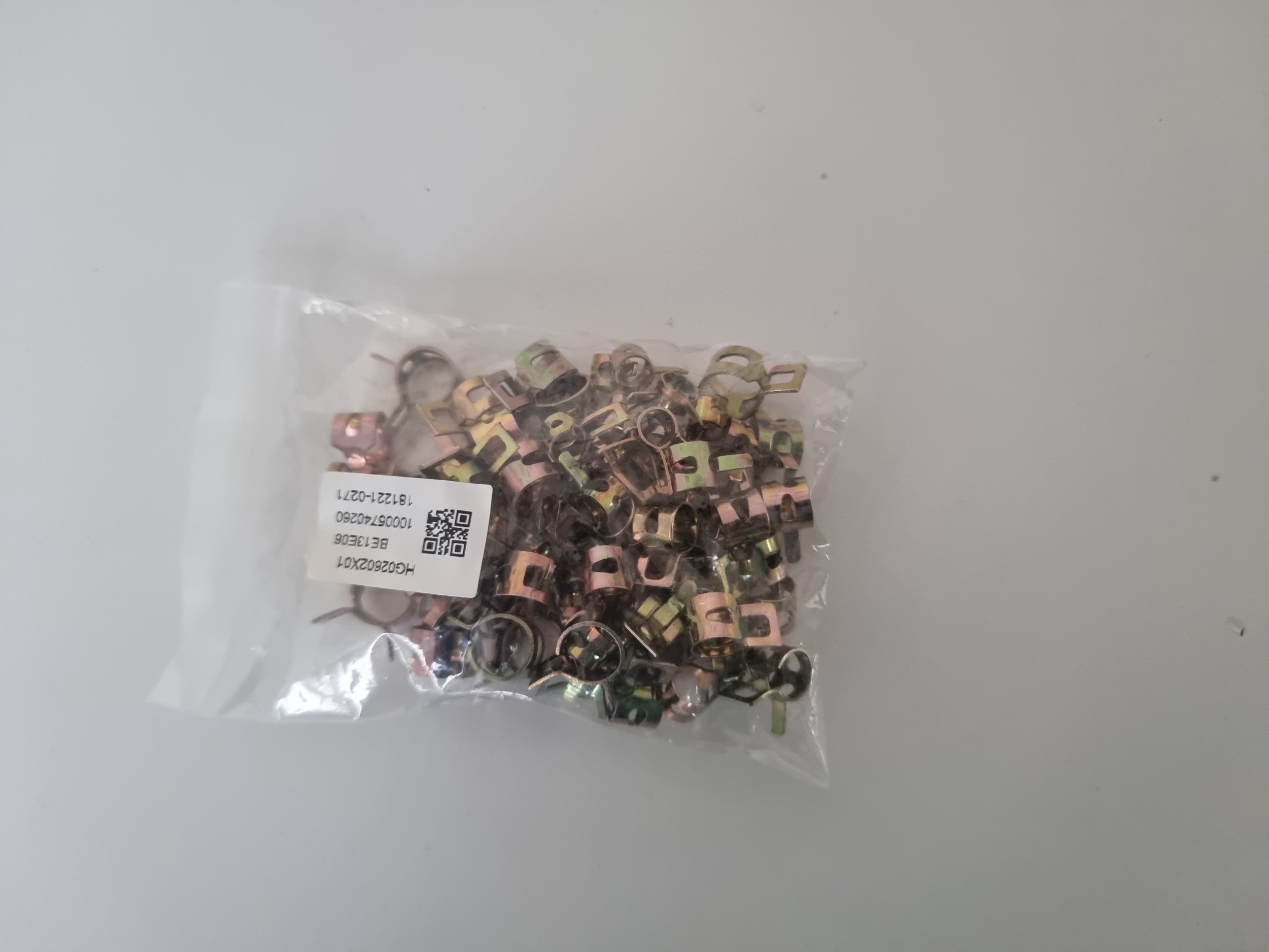
Fascette Metalliche per Tubi PVC
Avvertenza: Per garantire una migliore tenuta dei Tubi in PVC utilizzare le Fascette Metalliche Specifiche.
Durante la Fase di Test del Sistema di Raffreddamento ho riscontrato un Incremento della Restistenza al Flusso all'interno della Bobina a causa del uso di un Tubo in Rame da 3 mm che garantisce un maggiore reddimento sulla Scheda PCB.
Per mitigarne la perdita di efficienza avevo intenzione di modificare il Sistema Principale nel seguente modo:
Questa soluzione consente di Limitare la Caduta di Pressione realizzando un By-Pass.
Per realizzare questa modifica sarà necessario reperire i seguenti elementi:
- n.2 Raccordi a T;
- n.1 Rubinetto G1/4 M/F:
- n.1 Pompa 12Vcc 4W Max 300 L/h.
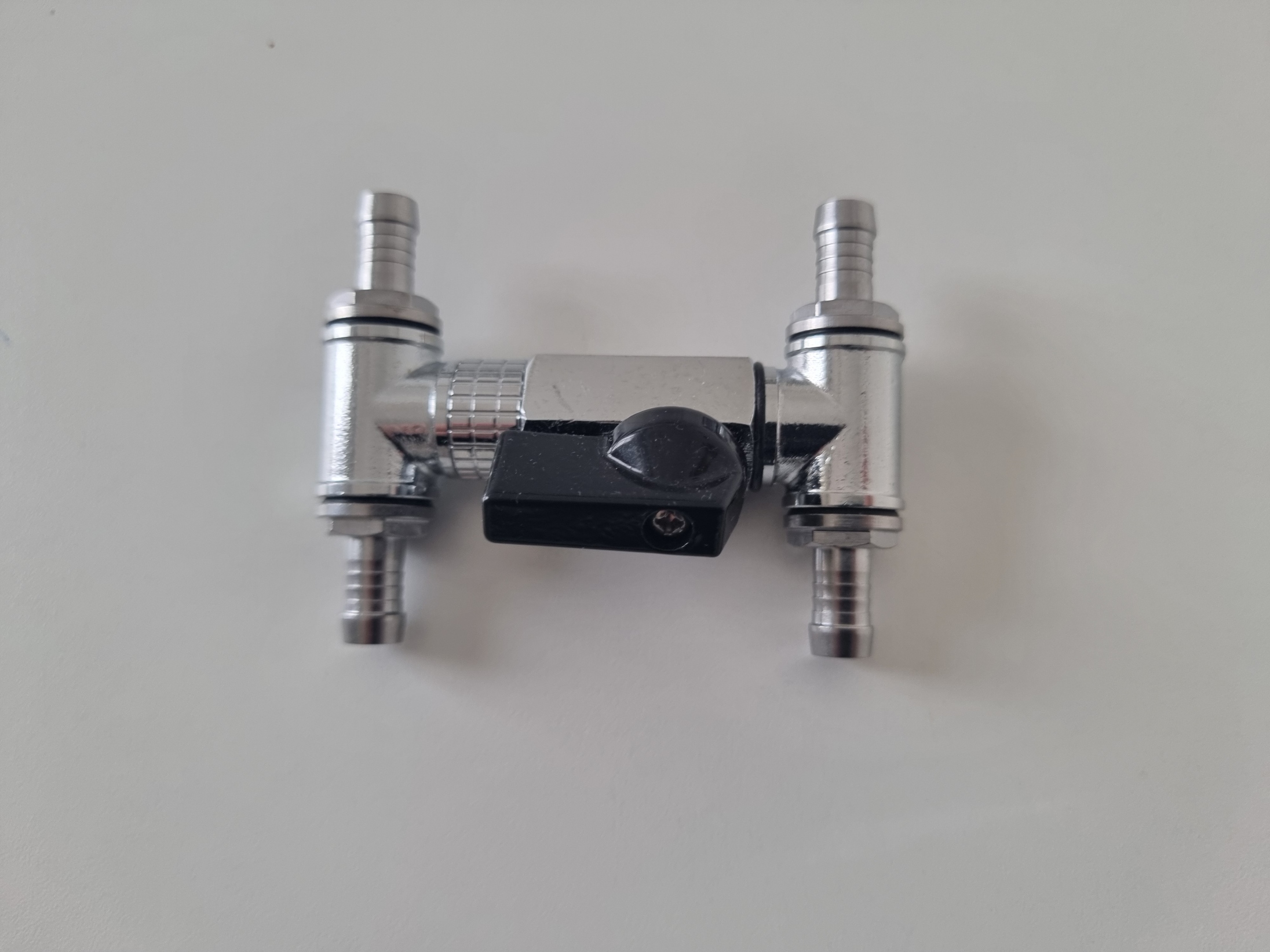
Blocco di By-Pass
Ho aggiunto al By-Pass un Rubinetto al fine di Valutarne l'efficienza della modifica introdotta.
A tal fine avevo intenzione di rimpiazzare i Raccordi a T con dei Raccordi a 4 Vie con Sensori di Temperatura.
In fase di Progetto avevo valutato la possibilità di integrare il Sistema Principale con il Secondario per incrementarne l'efficienza.
Soluzione accantonata poiché il Raffrendamento sulla Bobina presentava un peggioramento con Blocco dell'Annealer a Protezione della Scheda PCB.
Successivamente ho rimpiazzato il Rubinetto di Blocco con 2 Tappi al fine di facilitare Cambio Periodico per il Liquido di Raffreddamento.
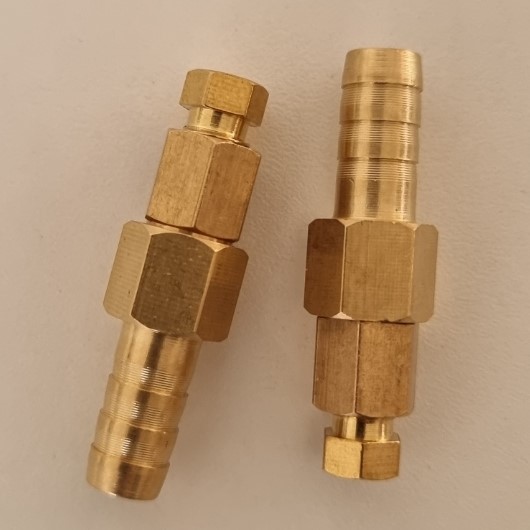
Raccordi a Compressione da 4mm con Transizione per Tubo Flessibile a 8mm
Dopo alcune Sessioni di Ricottura ho riscontrato una perdita di Liquido Refrigerante nelle Transizioni fra i Tubetti in Rame e in Plastica imputabile al Temperatura raggiunta dalla Bobina.
Al fine di prevenire il ripetersi di questa situazione pericolosa ho deciso di utilizzare dei Raccordi a Compressione in Ottone da 4mm.
Data l'impossibilità di reperire Raccordi da 1/8" ho rimpiazzato anche la Bobina realizzata con Rubetti del medesimo Diametro.
La nuova Bobina, realizzata da un Tubetto da 4mm, presenta un Profilo a Doppio Avvolgimento che consente di circoscrivere l'Operazione di Ricottura al solo Colletto.
Attualmente a scopo sperimentale ho realezzato 2 Doppie Bobine Isolate aventi le seguente Caratteristiche:
- Bobina 10.5
Bobina Isolata a Doppio Avvolgimento a 5 Spire Interne & 5 Spire Esterne con Diametro Interno di 3/4" - Bobina 8.4
Bobina Isolata a Doppio Avvolgimento a 4 Spire Interne & 4 Spire Esterne con Diametro Interno di 3/4"
Al termine della Fase di Sperimentazione, benché le 2 Soluzioni fossero sovrapponibili, ho optato per la Soluzione 8.4 per una maggiore compattezza nella Bobina.
L'implementazione di tale soluzione ha consentito l'eliminazione dei Tubi aventi un Diametro Inferiore ai 9mm in modo da migliorare l'Efficienza nel Sistema di Raffreddamento.
Per garantire una maggiore tenuta del Sistema di Raffreddamento utilizzare del Nastro al Teflon per Idraulica.
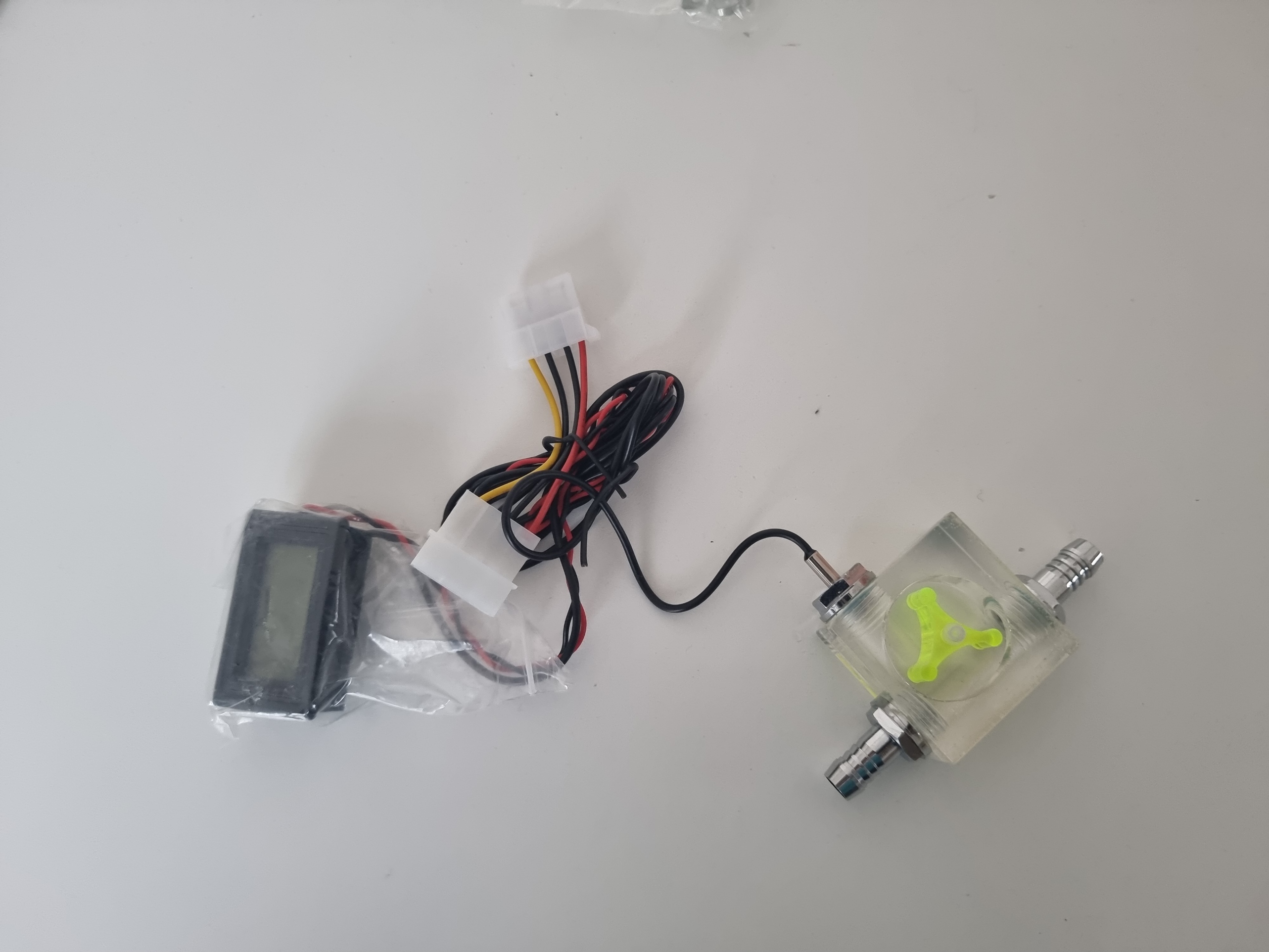
Flussometro con Sensore di Temperatura
Per monitorare l'efficienza del Sistema di Raffreddamento ho inserito nel Circuito n.2 Flussometri equipaggiati con Sensore di Temperatura.
Avvertenze: Il Serbatoi del Liquido, relativi ai Sistemi di Raffreddamendo, dovranno essere collocati ad un Livello maggiore Rispetto alla Bobina o ai Dissipatori sulla Scheda PCB.
In fase di Caricamento del Liquido Refrigerante attivare in Modo Intermittente le Pompe per eliminare le Bolle d'aria presenti nell'Impianto.
Con l'Eliminazione dell'Aria le Pompe dovrebbero presentare un'impronta sonora ridotta.
Avvertenza: In presenza di Oscillazioni Anomale nei Tubi in PVC interrompere immediatamente le Operazioni per verificare eventuali Ostruzioni o Guasti alle Pompe.
B. Sistema ad Aria sulla Scheda PCB & Chassis:
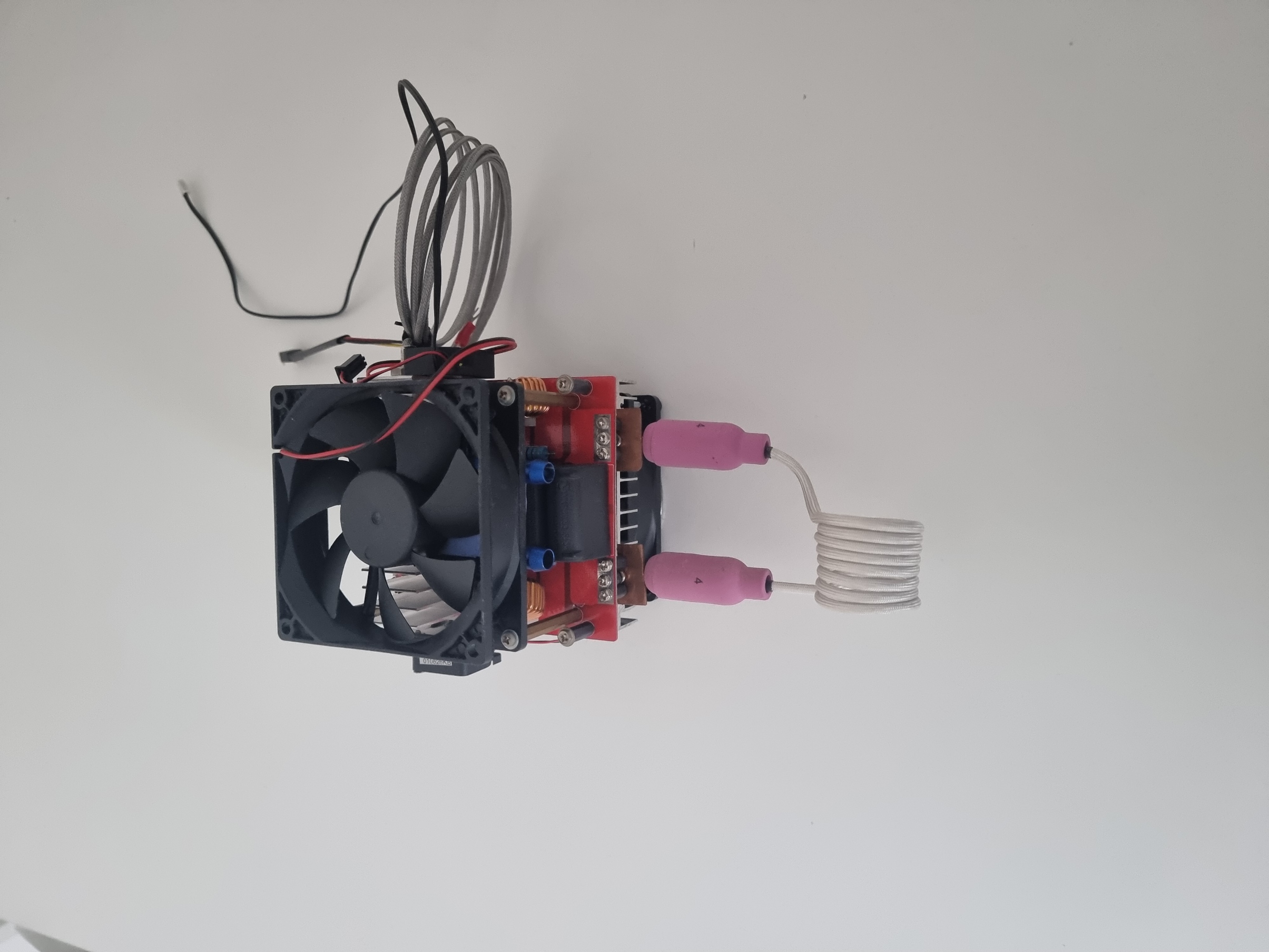
Ventola 80x80 Integrata sulla Scheda PCB
1. n.1 Ventola 80x80 integrata sulla Scheda PCB
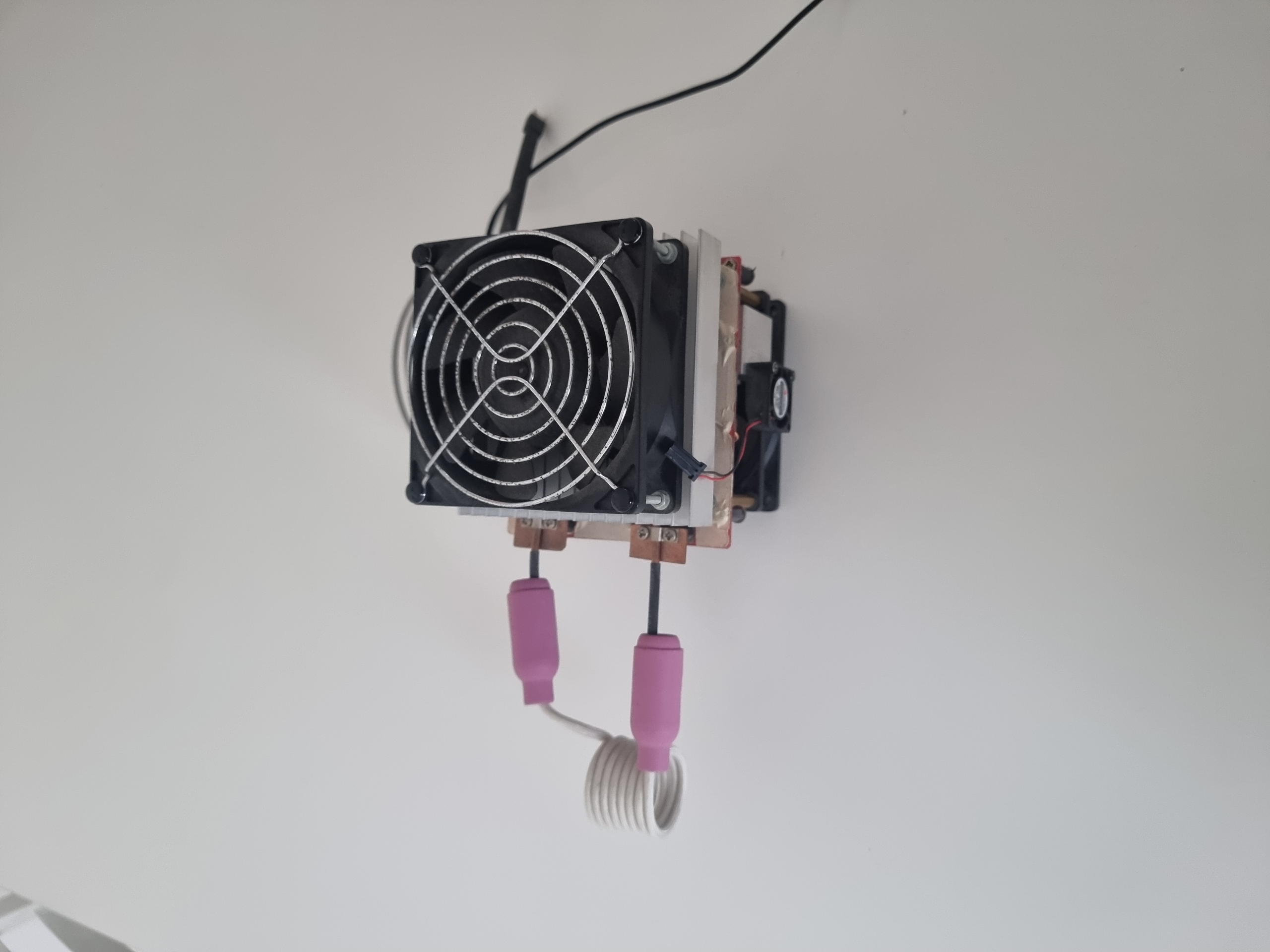
Ventole 90x90 sulla Scheda PCB
2. n.1 Ventola Tachimetrica 90x90 con Dissipatore in Alluminio.
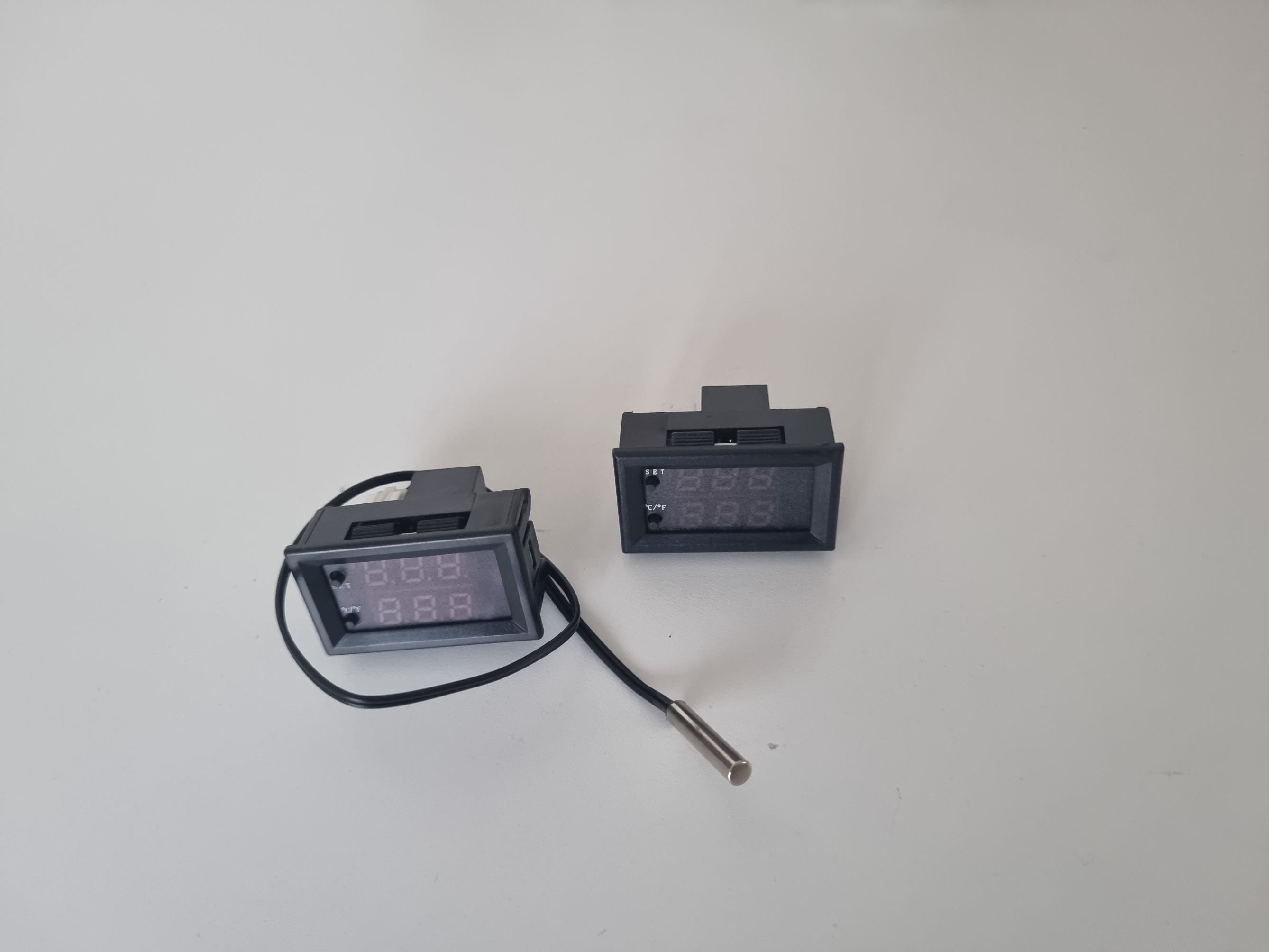
Controllo Tachimetrico Scheda PCB & Chassis
Il Controllo Tachimetrico sulla Scheda PCB sarà realizzato con un Sensore di Temperatura posto fra MOSFET & Condensatori.
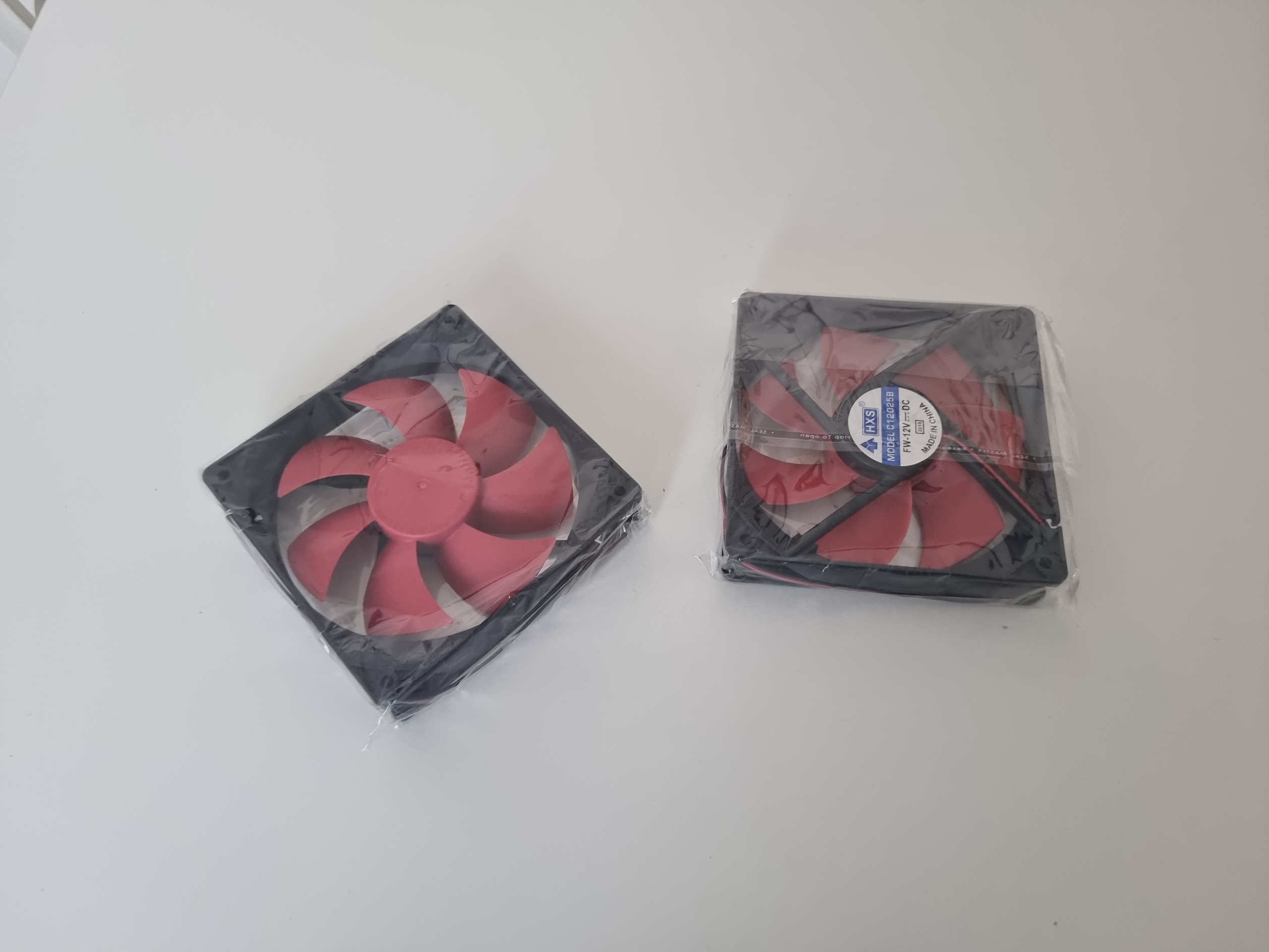
Ventole 120x120 sullo Chassis
3. n.2 Ventole Tachimetriche 120x120 con Sensore di Temperatura per prevenire il surriscaldamento dei Componenti Interni.
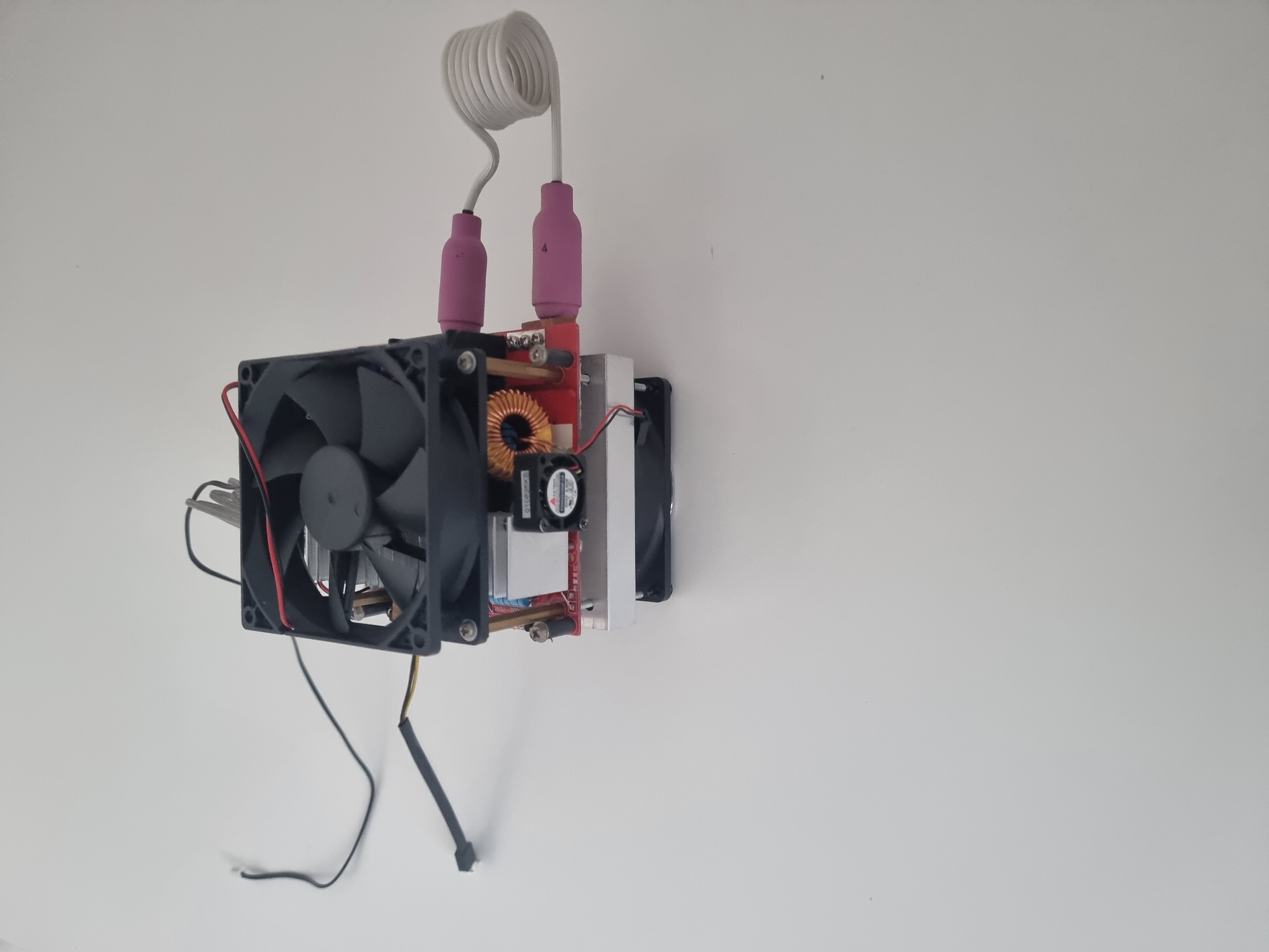
Ventole 25x25 sui MOSFET
4. n.2 Ventole 25x25 da 5V sui MOSFET.
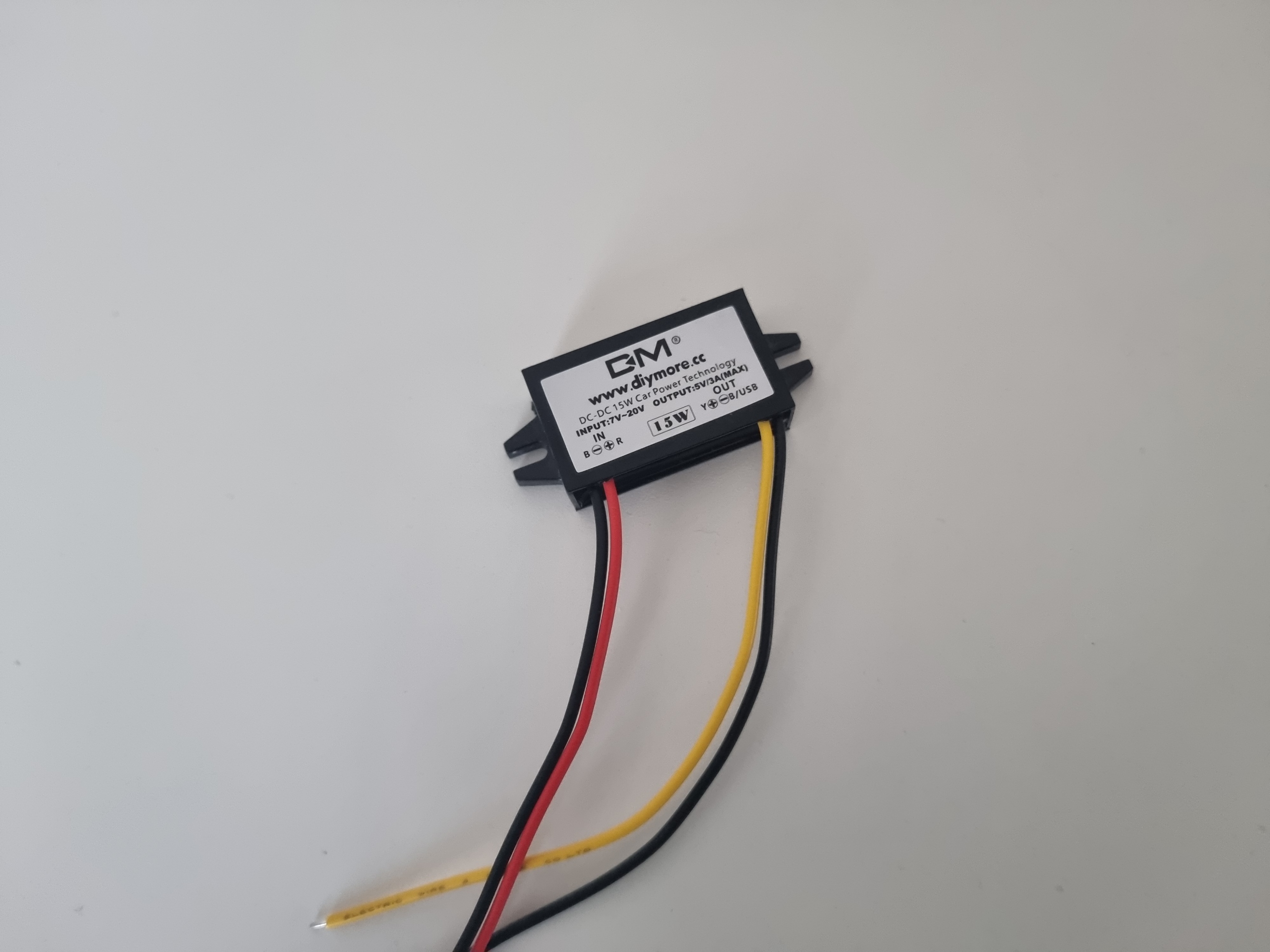
Ventole 25x25 sui MOSFET
Per l'Alimentazione delle Ventolw ho utilizzato un Convertitore di Tensione da 12V a 5V in grado di erogare fino a 3A.
5. n.2 Ventole 25x25 da 5V sui MOSFET.
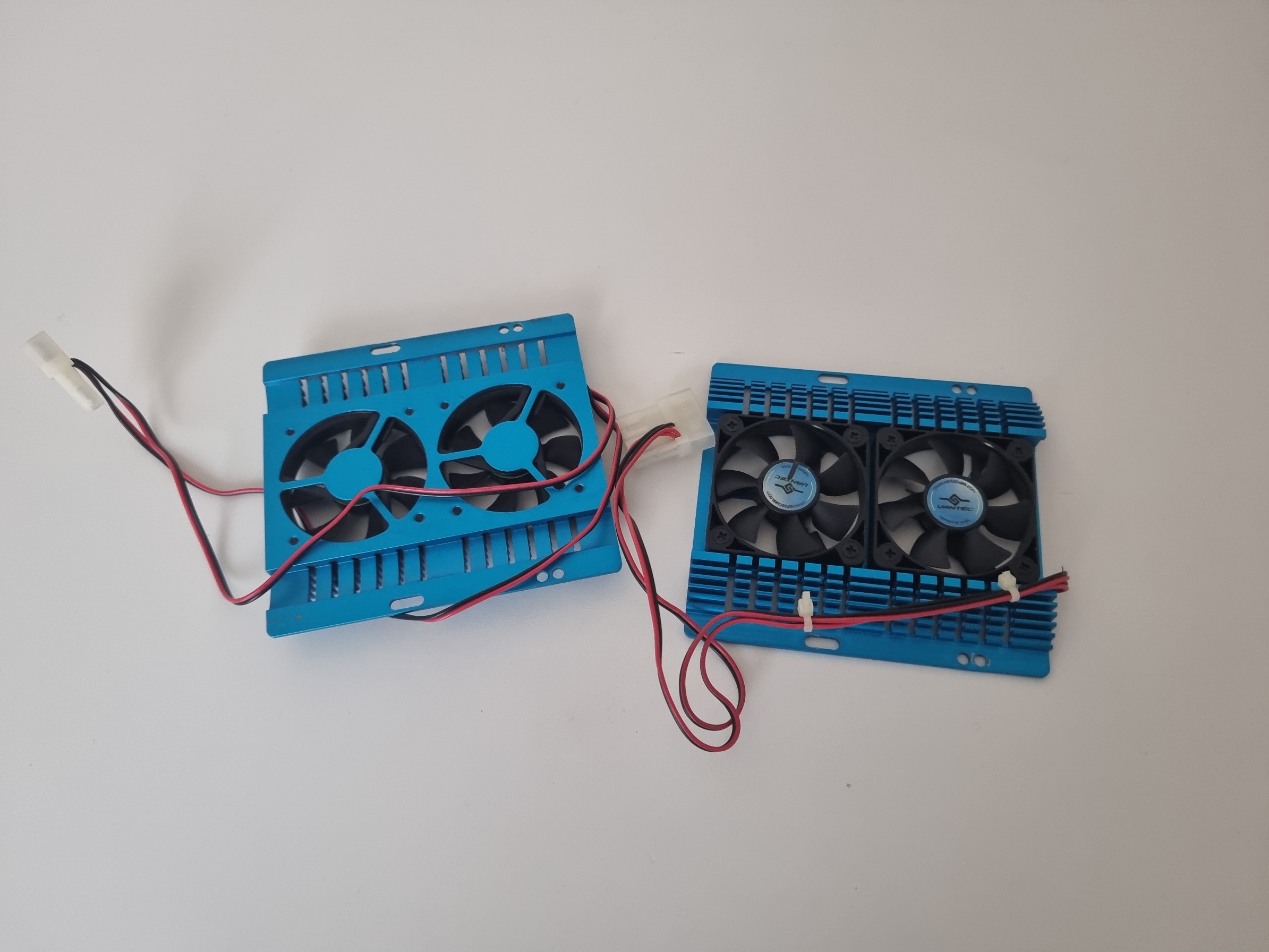
Ventole con Dissipatore per HDD
6. n.2 Ventole con Dissipatore per HDD.
Per migliorare il Raffreddamento di alcuni componenti ho riutilizzato alcune Ventole con Dissipatore utilizzate sugli HDD.
Nota: Ottima suluzione in presenza di uno Chassis in Metallo.
Avvertenza: Al fine di garantire una maggiore Protezione della Componentistica Interna impostare la Temperatura Limite a 70°C per il Blocco dell'Annealer.
In Fase Progettuale, al fine di limitare possibili problemi durante le Operazioni, sono stati inseriti ulteriori Dispositivi di Sicurezza sulla Scheda PCB come:
1. Relè di Potenza
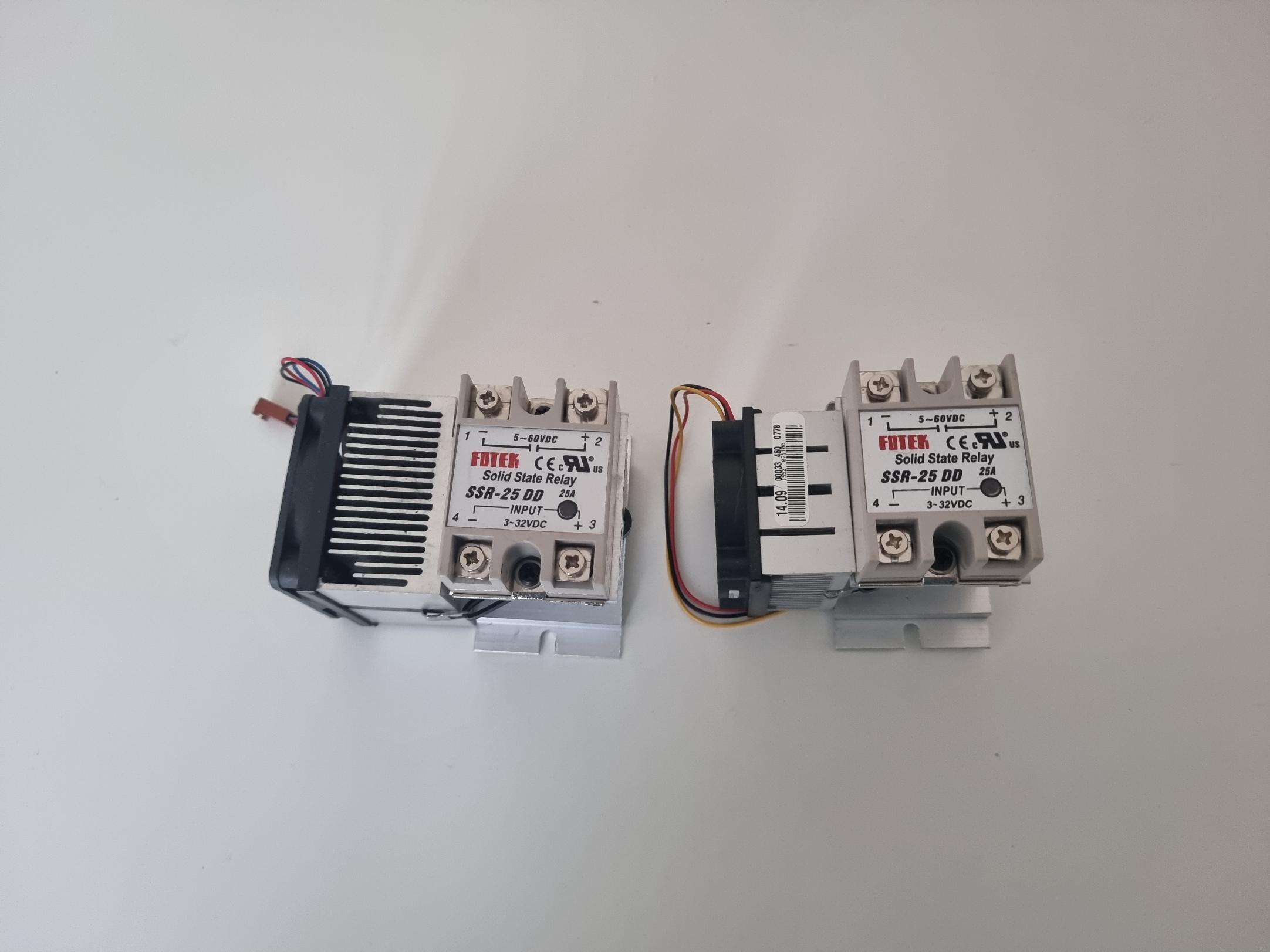
Relè Statico SSR-25DD con Dissipatore & Ventola
Come Relè di Potenza per il Controllo dell'alimentazione verso Scheda PCB sarà utilizzo un Relè Statico Modello SS-25DD che consente di gestire una Corrente Massima di 25A.
Avvertenza: Le Linee di Alimentazione fra: Alimentatore, Shunt, Relè di Potenza e Scheda PCB; dovranno presentare un Diametro adeguato, non inferiore a 1,5mm, per evitare una Caduta di Tensione.
2. Volmetro & Amperometro con Shunt
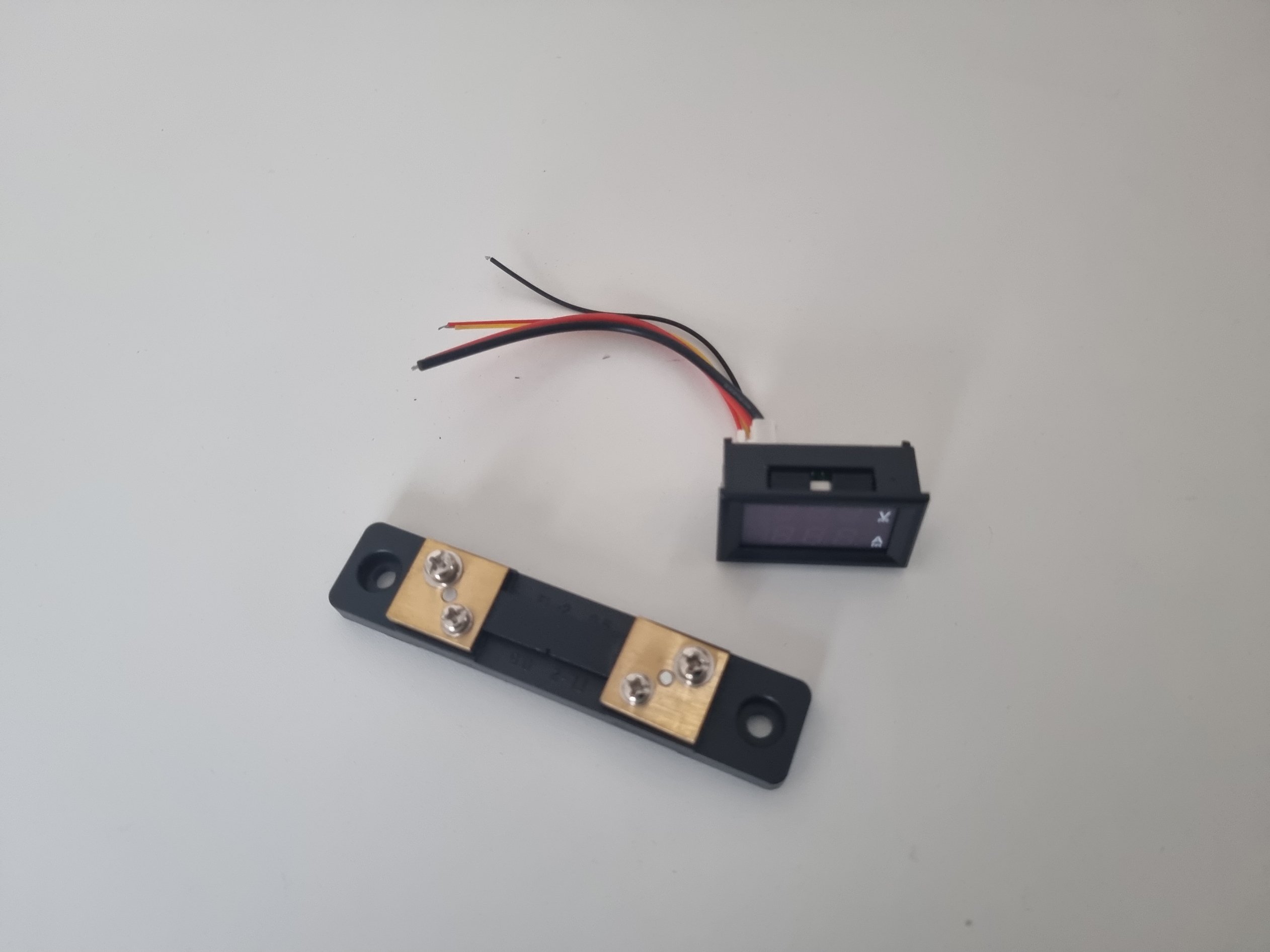
Volmetro & Amperometro con Shunt
Per garantire una maggiore sicurezza sarà installato un Volmetro/Amperometro sulla Linea di Alimentazione verso Scheda PCB allo scopo di monitorare la Corrente Assorbita dalla Bobina.
Nota: Applicato il medesimo Dispositovo anche all'Uscita dell'Alimentatore Secondario 12 20A.
3. Disgiuntore
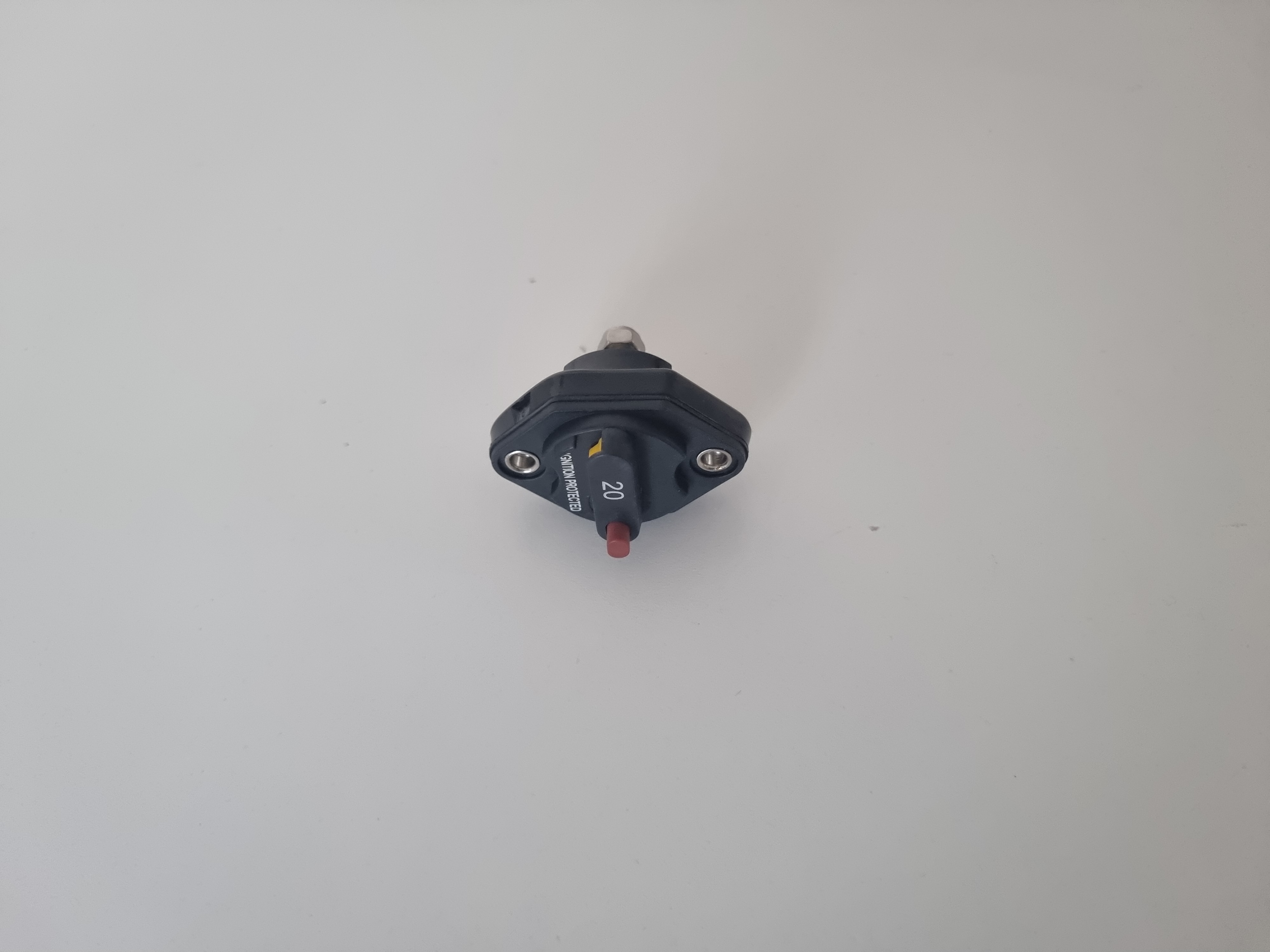
Disgiuntore da 20A per Alimentore Pricipale 36V 20A & Scheda PCB
Per limitare la Corrente Massima a 20A viene utilizzato un Disgiuntore con Reset Manuale.
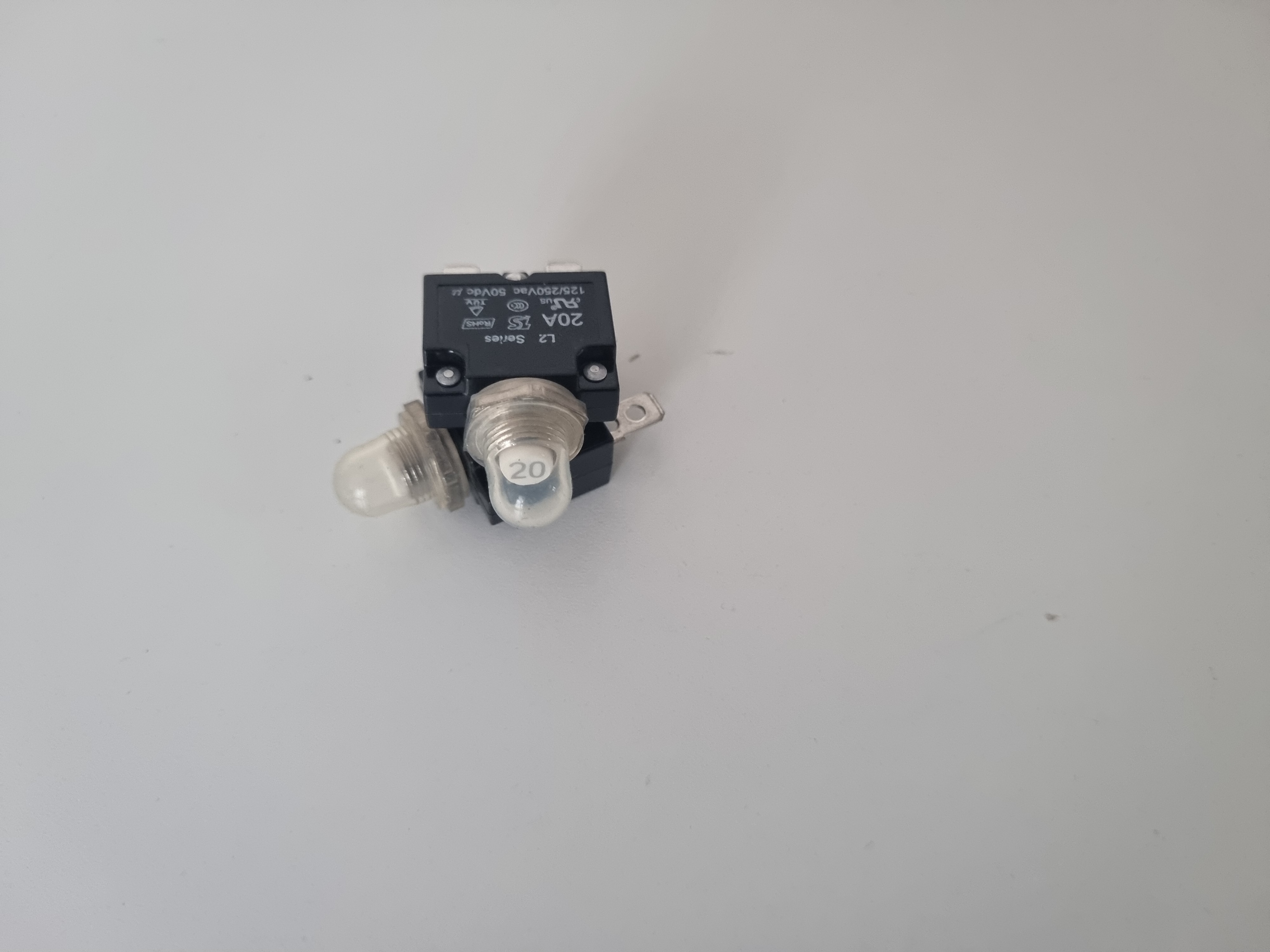
Disgiuntore da 20A per Alimentatore Sendario 12V 20A
Medesima Protezione sarà offerta anche all'Alimentatore Secondario da 12V 20A.
4. Relè di Controllo Tempertura
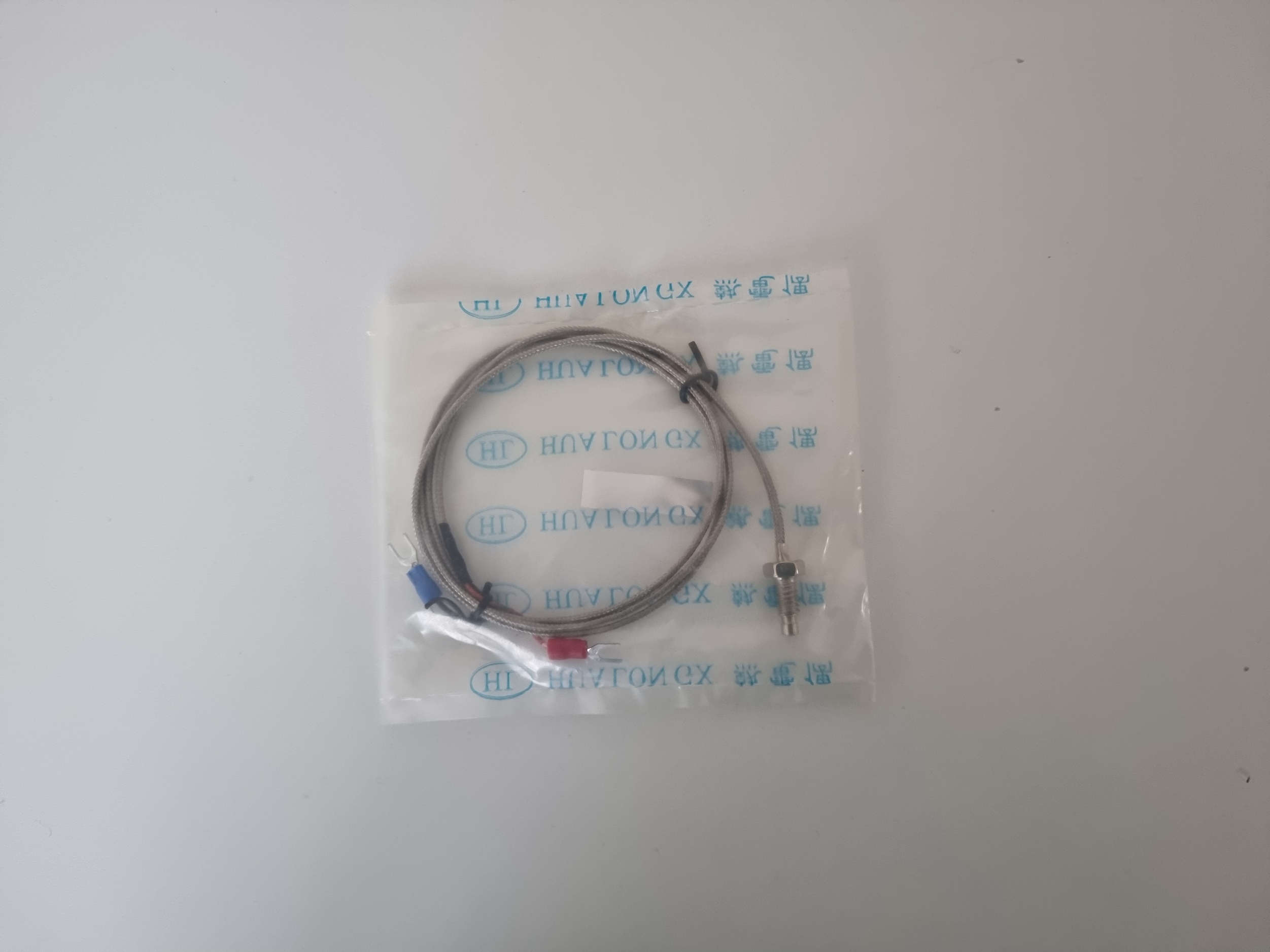
Sensor K per Sestos Temperature Control D1S-2R-24
Per garantire una maggiore sicurezza sulla Scheda PCB utilizzo un Relè con Sonda Tipo K, Modello D1S-2R-24 della Sestos, in modo da interdire l'alimentazione quando la Temperatura sui MOSFET supera un Valore Predefinito.
5. Relè Standard DPDT
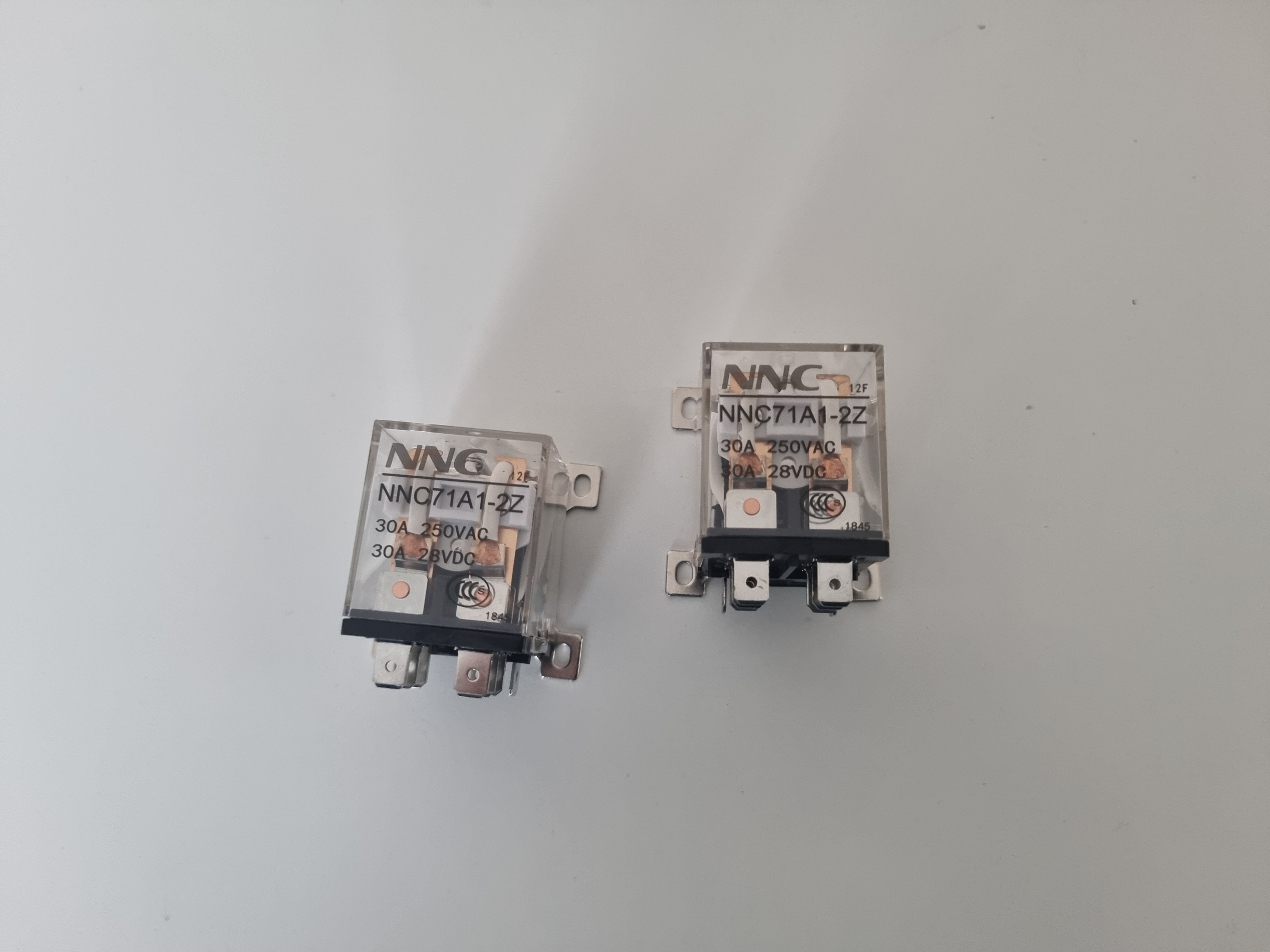
Relè Standard DPDT
I n.2 Relè Standard DPDT, nel Controllo del Sistema Auto Feed (Solenoidi & Motori), sono utilizzati per garantire Isolamento & Protezione ai Relè Seston.
6. Diodo di Protezione
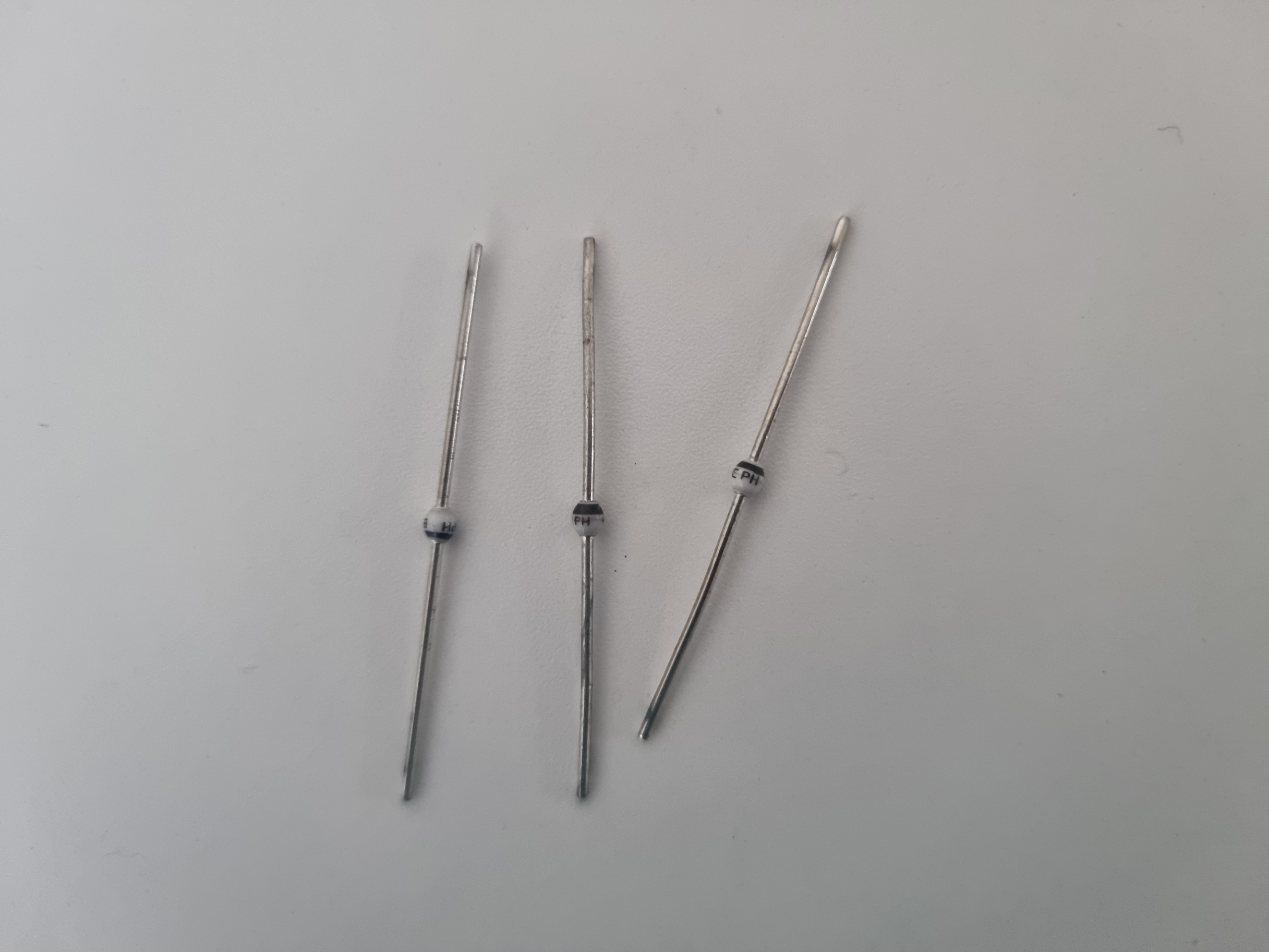
Diodo di Protezione
Sui Relè Standard DPDT & Solenoidi inserire un Diodo di Protezione.
Nota: Operazione non necessaria con Relè di Tipo Statico.
7. Isolatori in Ceramica
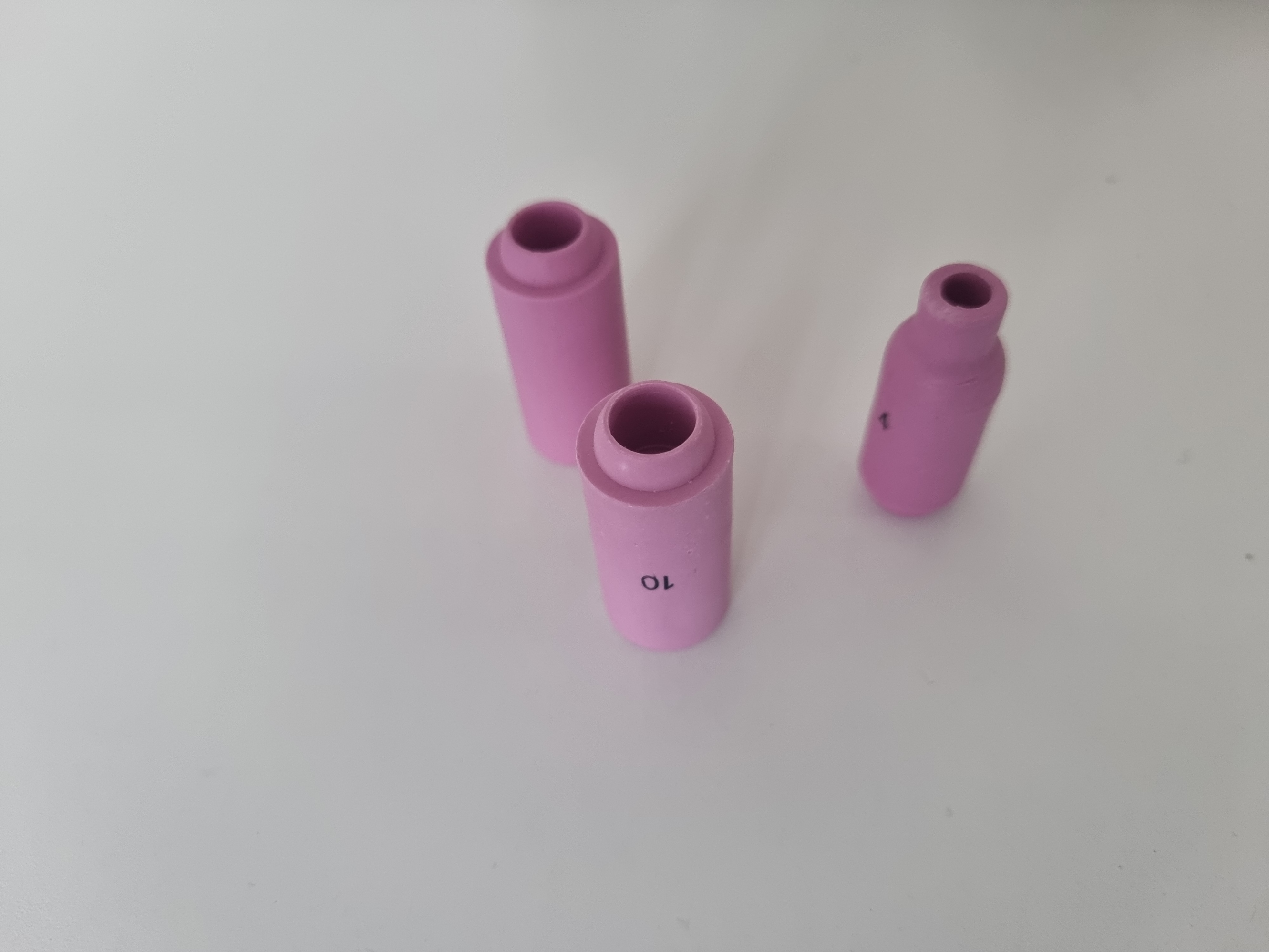
Ugelli in Ceramica TIG #8 - #10 - #12
Per l'isolamento delle superfici contatto diretto con la Bobina utilizzo dei Materiali Ceramici, come gli Ugelli per la Saldatura a TIG.
8. Filtro di Rete & Fusibili
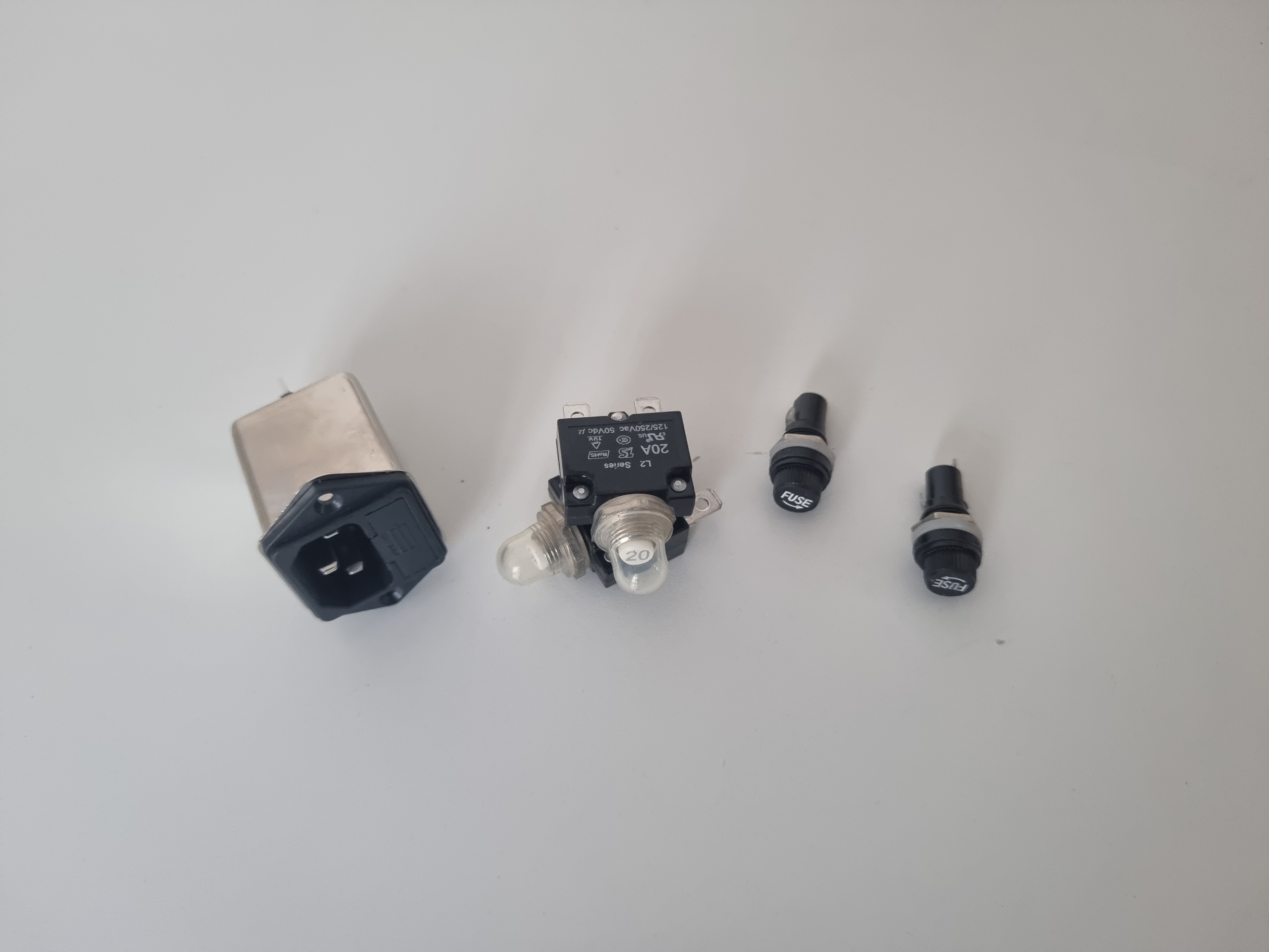
Filtro di Rete & Fusibili
Per una maggiore Protezione viene utilizzato un Filtro di Rete e Fusibili Rapidi sugli Alimentatori Primario e Secondario.
Nota: A protezione di alcuni componenti elettronici ho utilizzato anche dei Fusibili di Tipo Automibilistico.
9. Volmetro & Amperometro
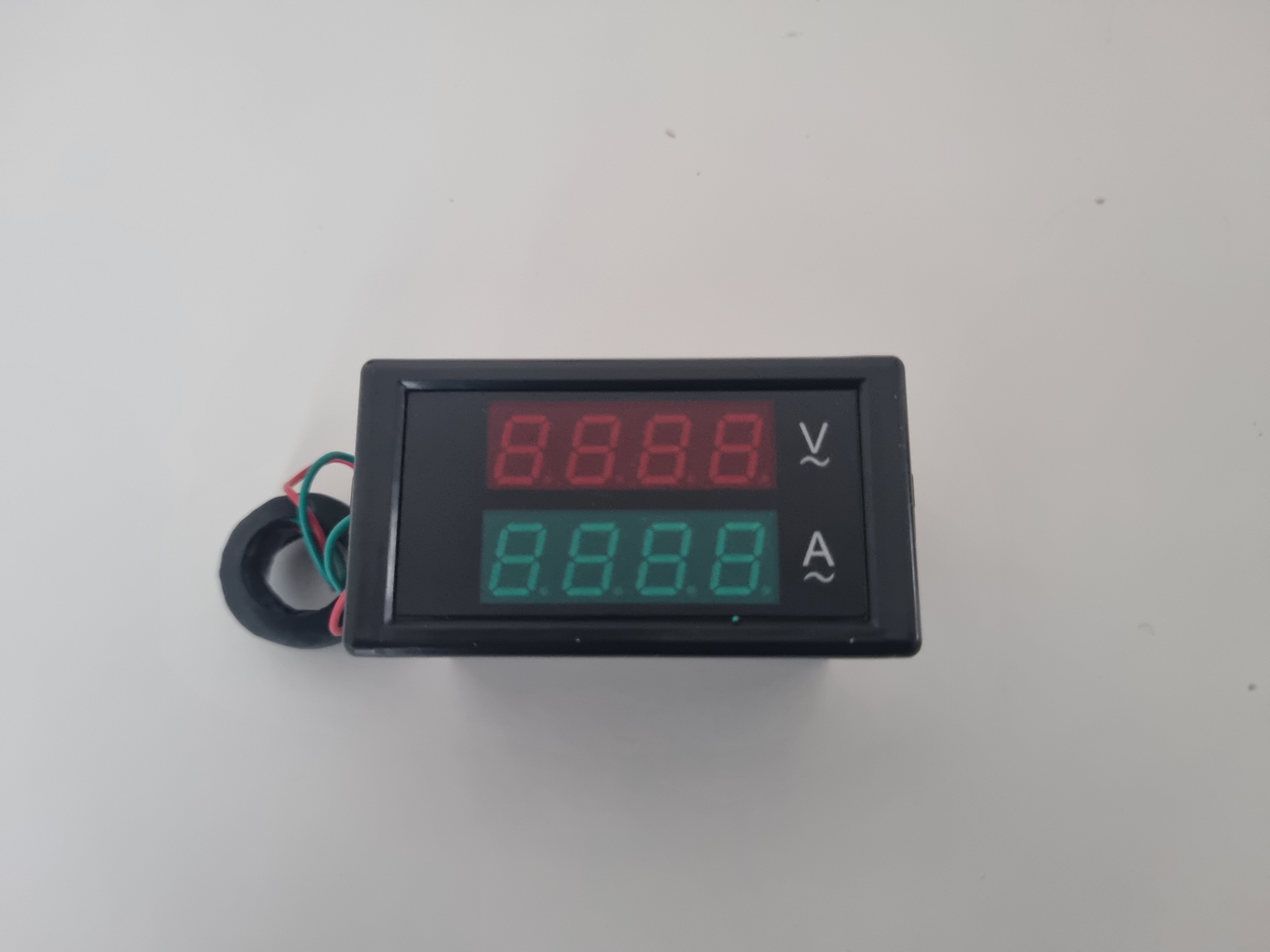
Volmetro & Amperometro sull'Ingresso di Rete
Lo Strumento ha la sola funzione di Monitorare l'Assorbimento dell'Anneale.
10. Controllo delle Ventole Tachimetrice
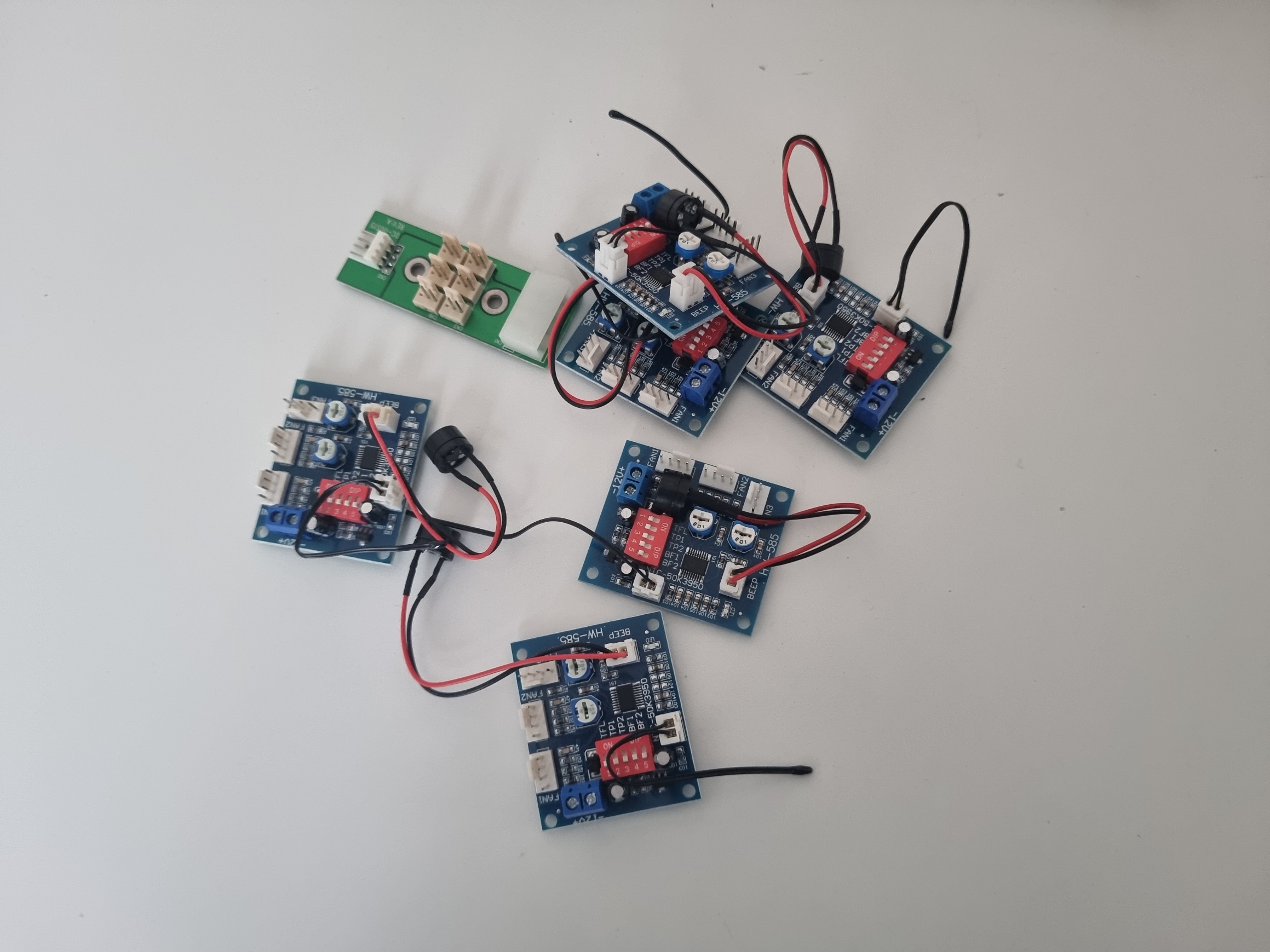
Schede per il Controllo delle Ventole Tachimetrico con Sensore di Temperatura & Cicalino
Solitamente utilizzate per Controllare le Ventole Tachimetriche utilizzate in questo Progetto.
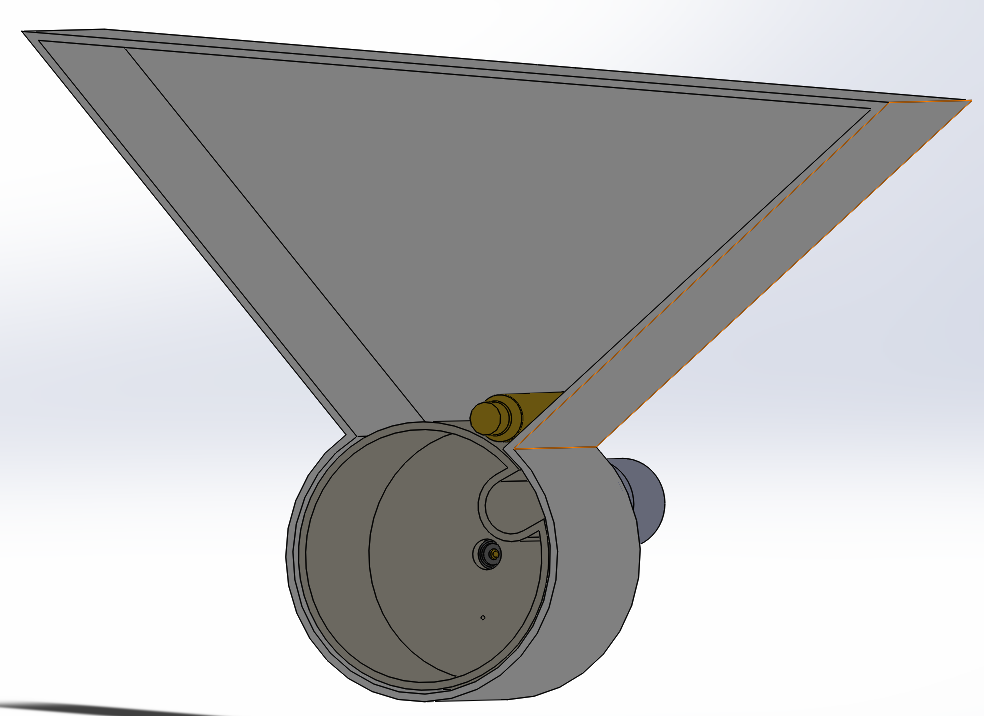
Sistema Auto Feed
Attualmente l'Annealer, pur essendo prediposto, non dispone di un Sistema Auto-Feed per Carico & Scarico in Modo Automatico dei Bossoli.
Per la predisposizione all'upgrade ho inserito i seguenti componenti:
A. n.1 Relè Counter, Modello C2S-R-24 della Sestos, integrato con il Timer Industriale consentirà il funzionamento in Modalità Automatica quando l'Annealer sarà corredato di un Sistema Auto Feed.
Nota: Nel Diagramma sono illustrati i collegamenti elettrici per l'integrazione fra Timer & Counter.
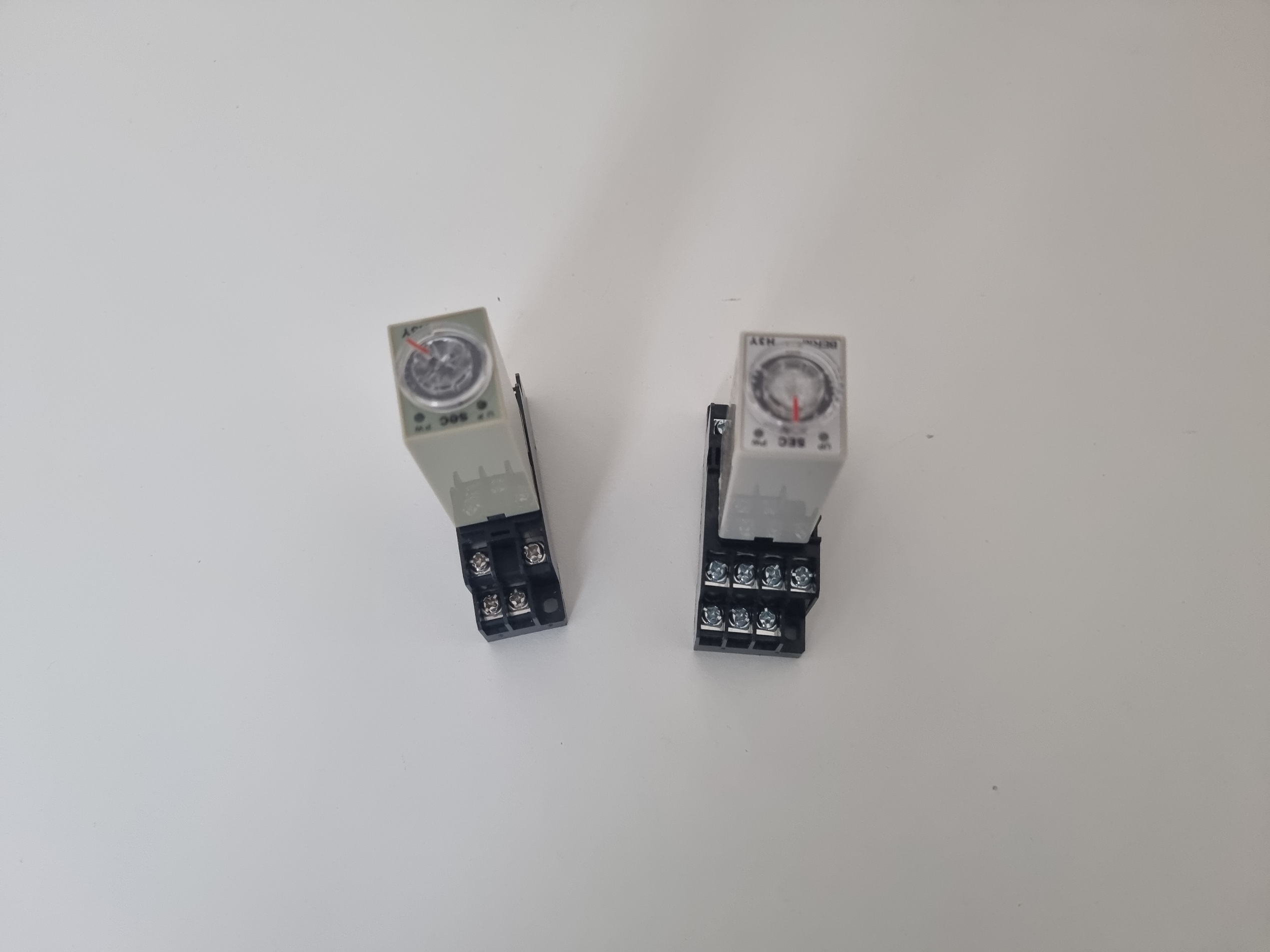
Omron Timer Delay H3Y-4 & H3Y-2
B. n.2 Relè Timer Delay, Modello H3Y-4 (H3Y-2) della Omron, per temporizzare i Motori 12V DC sull'Auto.
Questo Modello consente posticipare o anticipare il Caricamento dei Bossoli in Modalità Automatica.
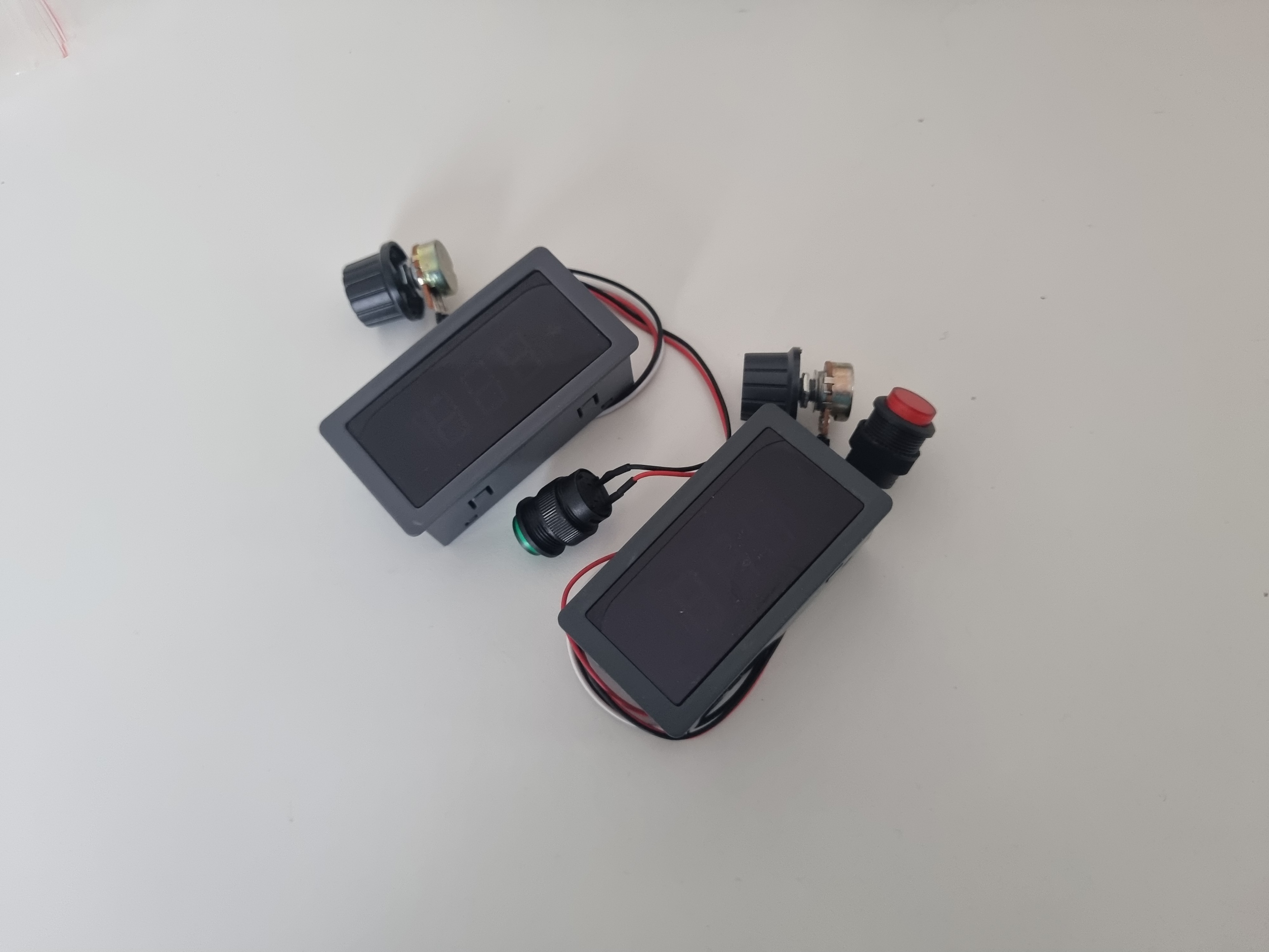
Controller DC PWM
C. n.2 Controller DC PWM per il Controllo dei Motori 12V DC sull'Auto Feed.
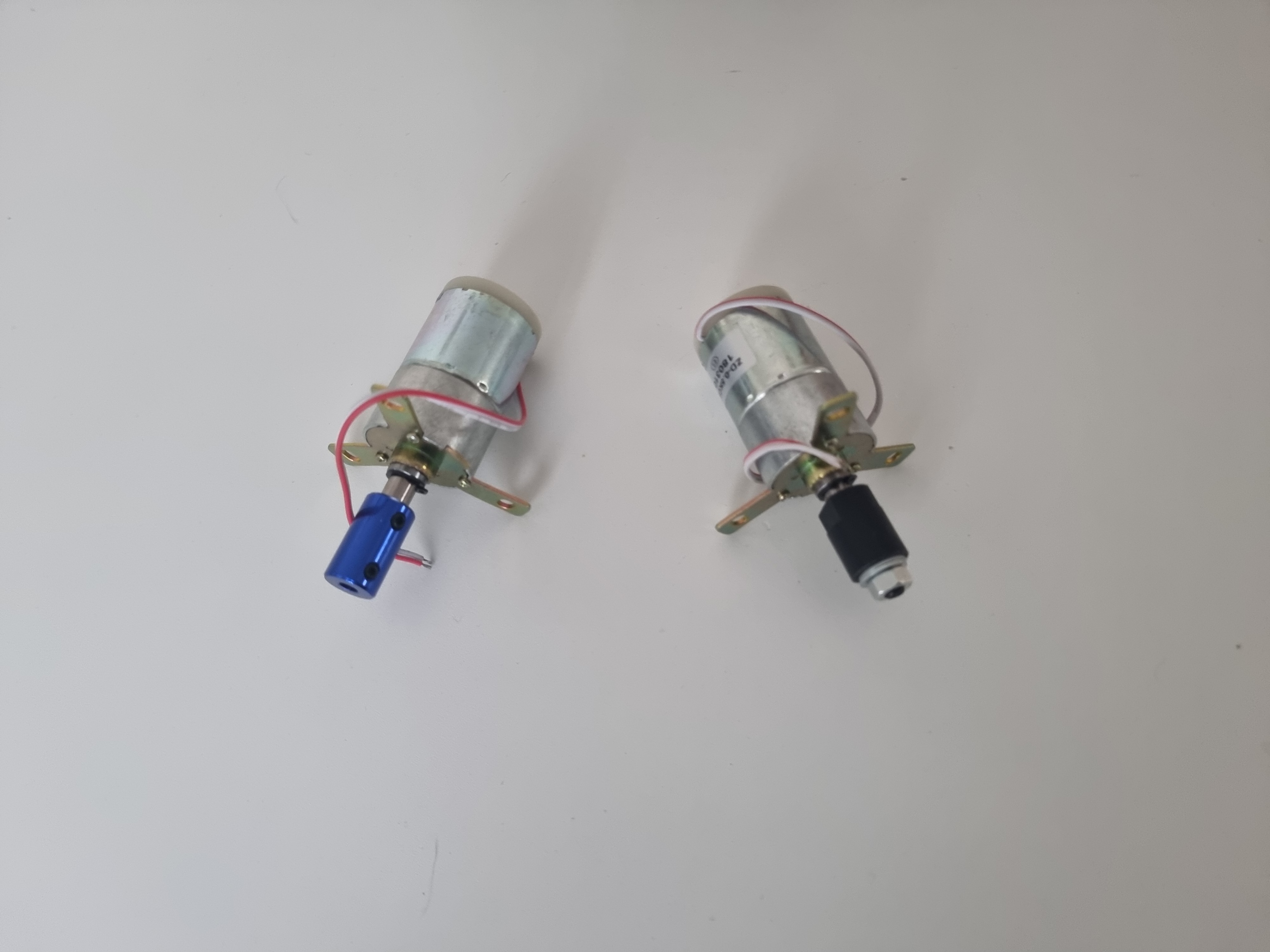
Motore 12V DC 25 RPM Max
D. n.2 Motori 12V DC, con Velocità Massima di 25 RPM, per il Caricamento dei Bossoli in Modalità Automatica sull'Auto Feed.
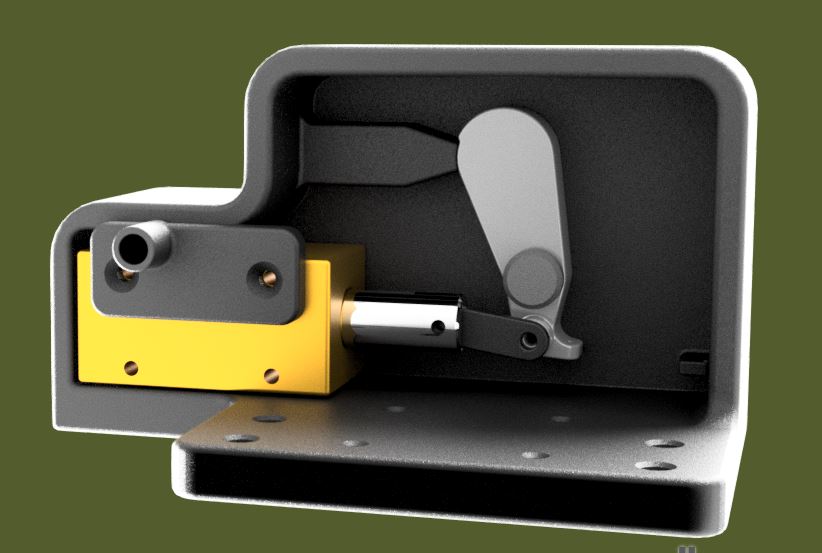
Sistema di Scarico
In combinazione con l'Auto Feed sarà necessario realizzare un Sistema di Carico & Scarico per i Bossoli dalla Bobina utilizzando i seguenti componenti:
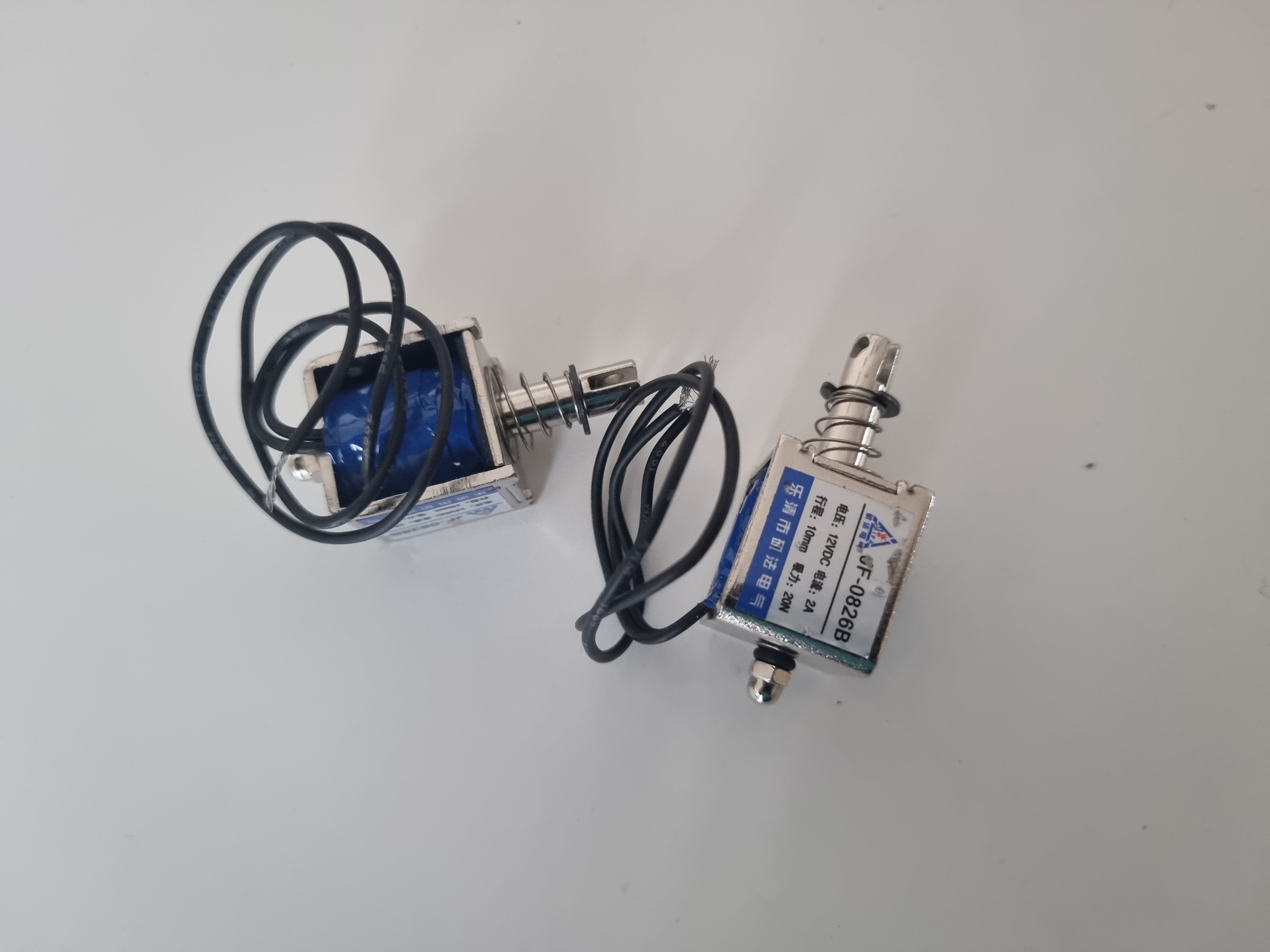
Solenoidi di Carico & Scarico
n.2 Solenoidi per Sistema di Carico & Scarico dei Bossoli nella Babina in Modalità Automatica.
Nota: Il Sistema di Scarico viene comunemente utilizzato anche in presenza di un Sistema con Caricamento Manuale allo scopo di incrementarne le prestazioni.
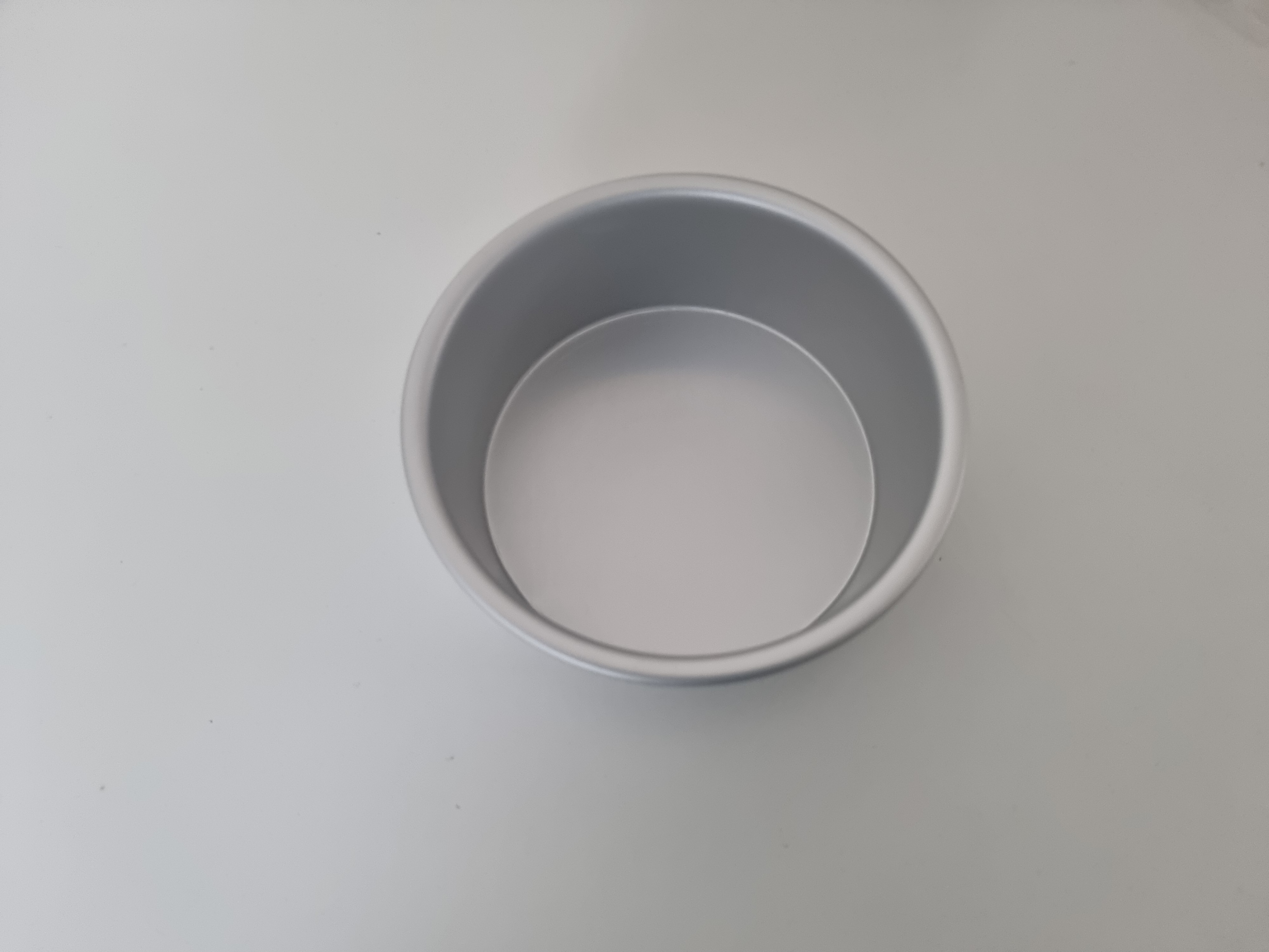
Auto Feed Annealer Gas
Avendo a disposizione il Sistema di Alimentazioni Bossoli sviluppato per l'Annealer a Gas ho deciso di adattarlo al Dispositivo ad Induzione.
In questo caso sarà necessario realizzare un Imbuto di Carico con Solenoide.
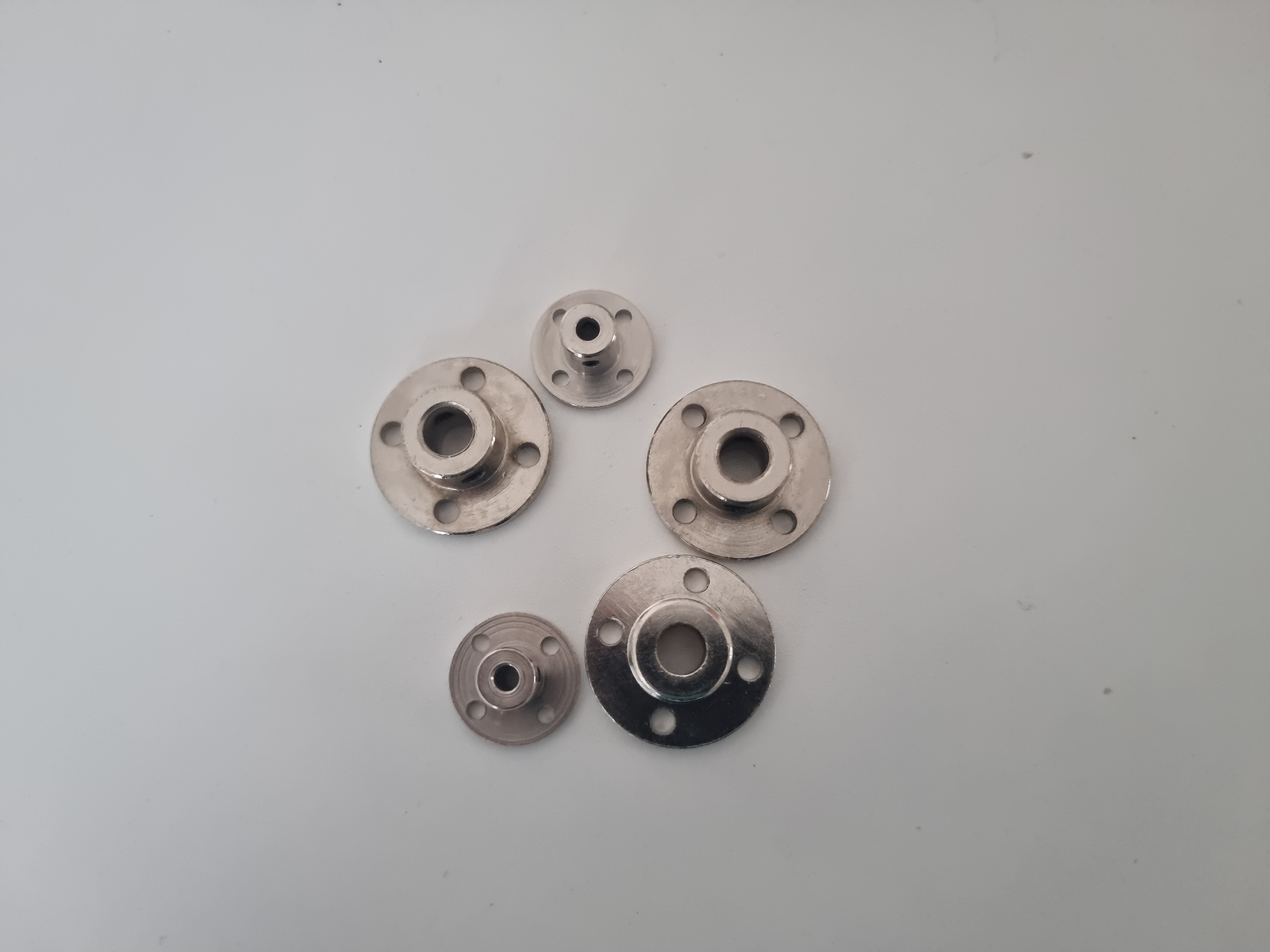
Raccordi Albero di Trasmissione Motore per Tamburi Rotanti
Nota: Con questo Sistema di Auto Feed sarà sempre richiesto il Caricamento Ordinato dei Bossoli.
Per il corretto funzionamento sarà necessario realizzare diversi Tamburi in relazione al Calibro in Ricottura.
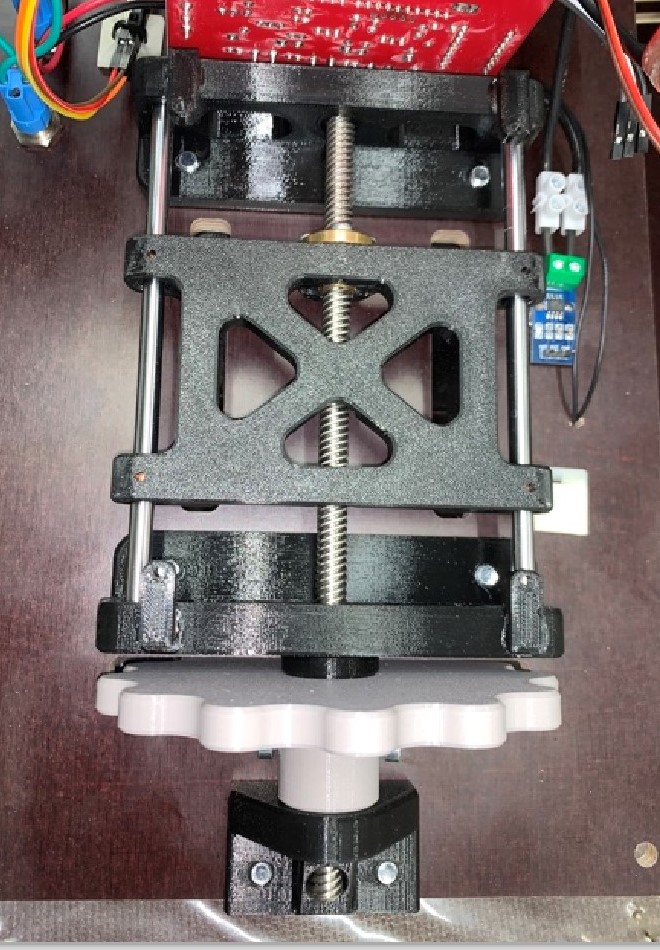
Sistema per Regolare la Profondità di Immersione nella Bobina
Per ottimizzare le Operazioni di Ricottura sarà necessario realizzare un Sistema per Regolare la Profondità di Immersione nella Bobina in relazione al Calibro del Bossolo.
La Corretta impostazione di questo Parametro consente, oltre a limitare la Corrente Assorbita, di circoscrivere la Ricottura al solo Colletto.
Solitamente nel Sistema di Scarico per i Bossoli viene integrata la possibilità di Calibrare la Bobina.
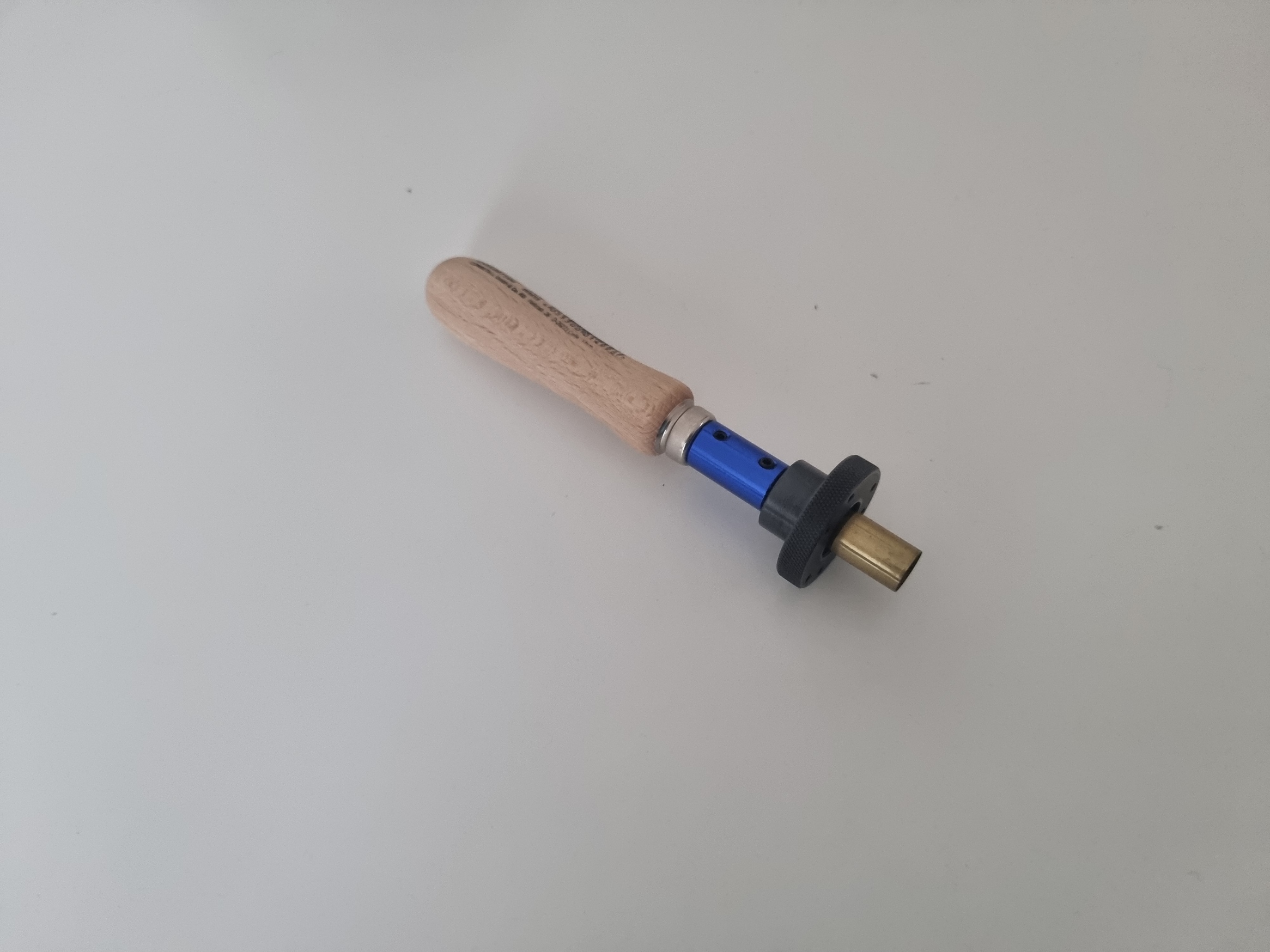
Annealer Shell Holder
Attualmente non disponendo di un Sistema di Scarico Automatico dei Bossoli utilizzo uno Shell Holder Universale.
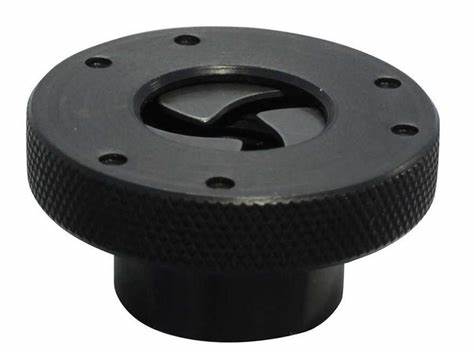
3 Jaw Chuck Shell Holder
Per la costruzione di questo dispositivo ho utilizzato il 3 Jaw Chuck della Lee Precision applicato ad un Manico in Legno.
Attualmente il Sistema per la Calibrazione consiste in una semplice Forcella a V Regolabile in Altezza.
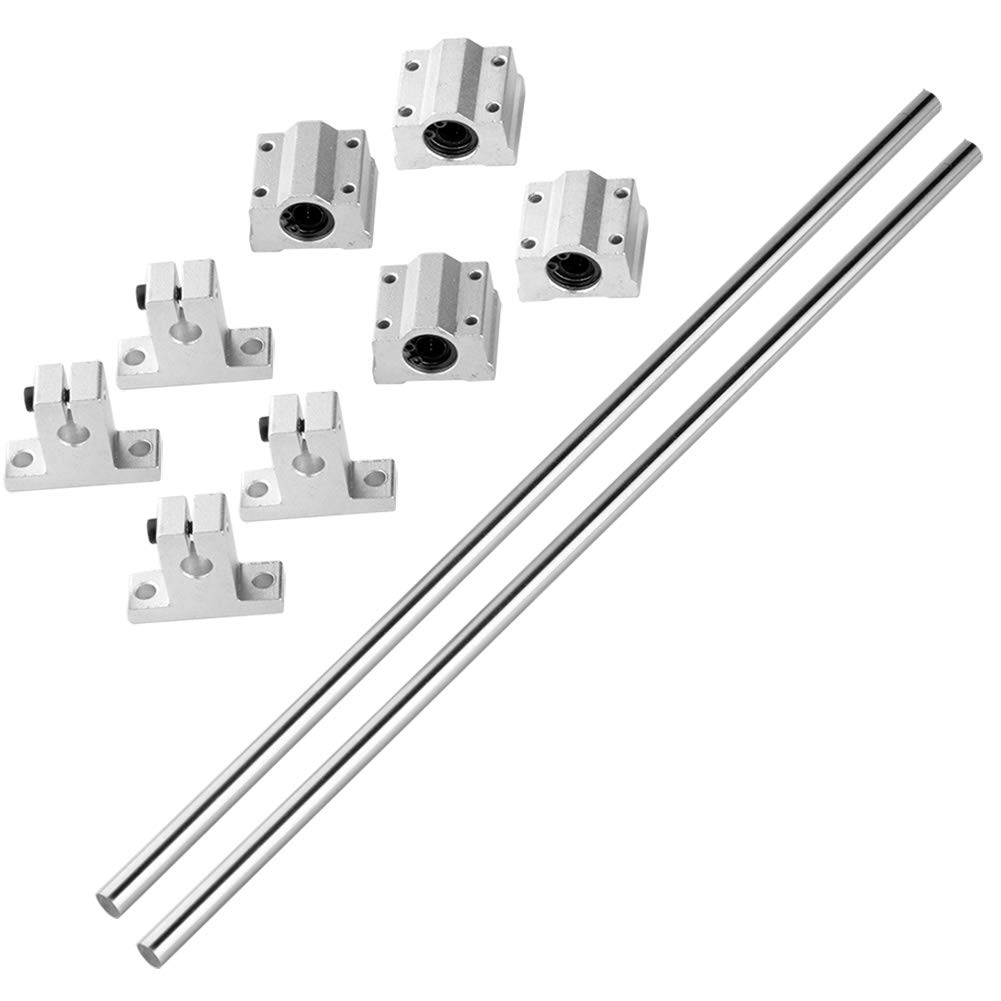
Guide Lineari da 200mm per Stampante 3D
Poiché tale Dispositivo non garantisce una Regolazione Fine della Profondità di Immersione della Bobina ho deciso di realizzare un Carrello Motorizzato utilizzando delle Guide Lineari (Max 200mm) per Stampanti 3D.
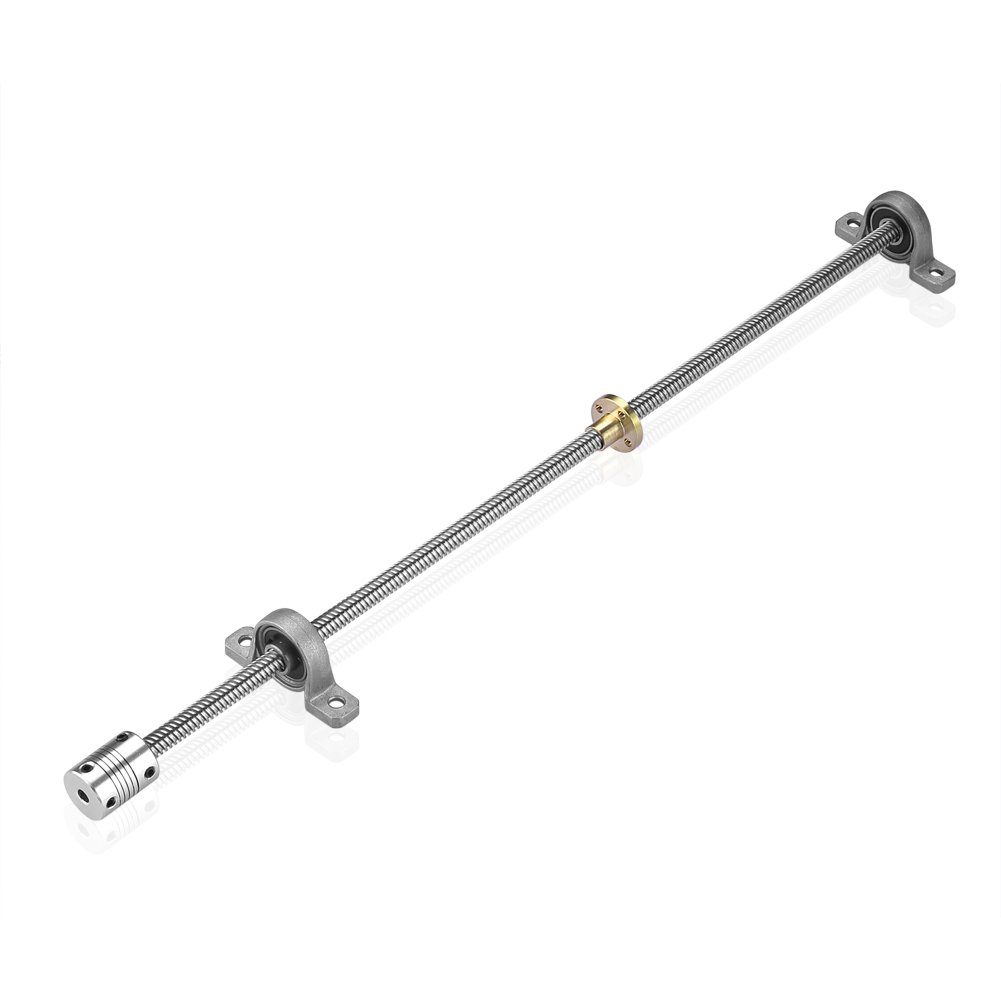
Vite Senza Fine da 200mm con Supporti per Stampante 3D
Mentre per la movimentazione, scartata l'ipotesi di un Motore Passo-Passo, ho optato per una Vite senza Fine con un MotoRiduttore a 12Vcc.
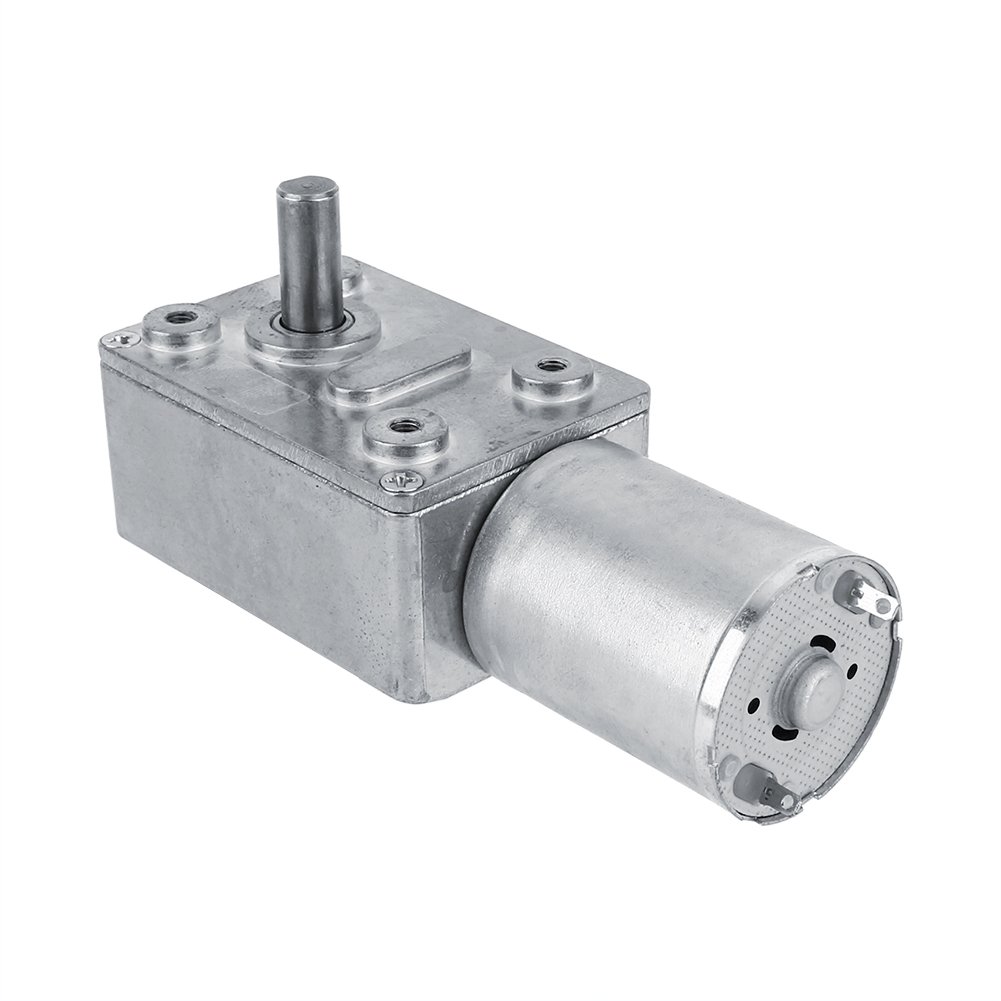
MotoRiduttore 2 RPM da 12Vcc
In prima istanza avevo valutato la possibilità di Regolare la Calibrazione sul Sistema di Carico & Scarico.

Sistema di Regolazione sulla Profondità di Immesione nella Bobina
Successivamente ho deciso di Regolare la Calibrazione direttamente sulla Scheda PCB.
A tal fine ho dovuto procedere alla completa Riprogettazione dello Chassis.
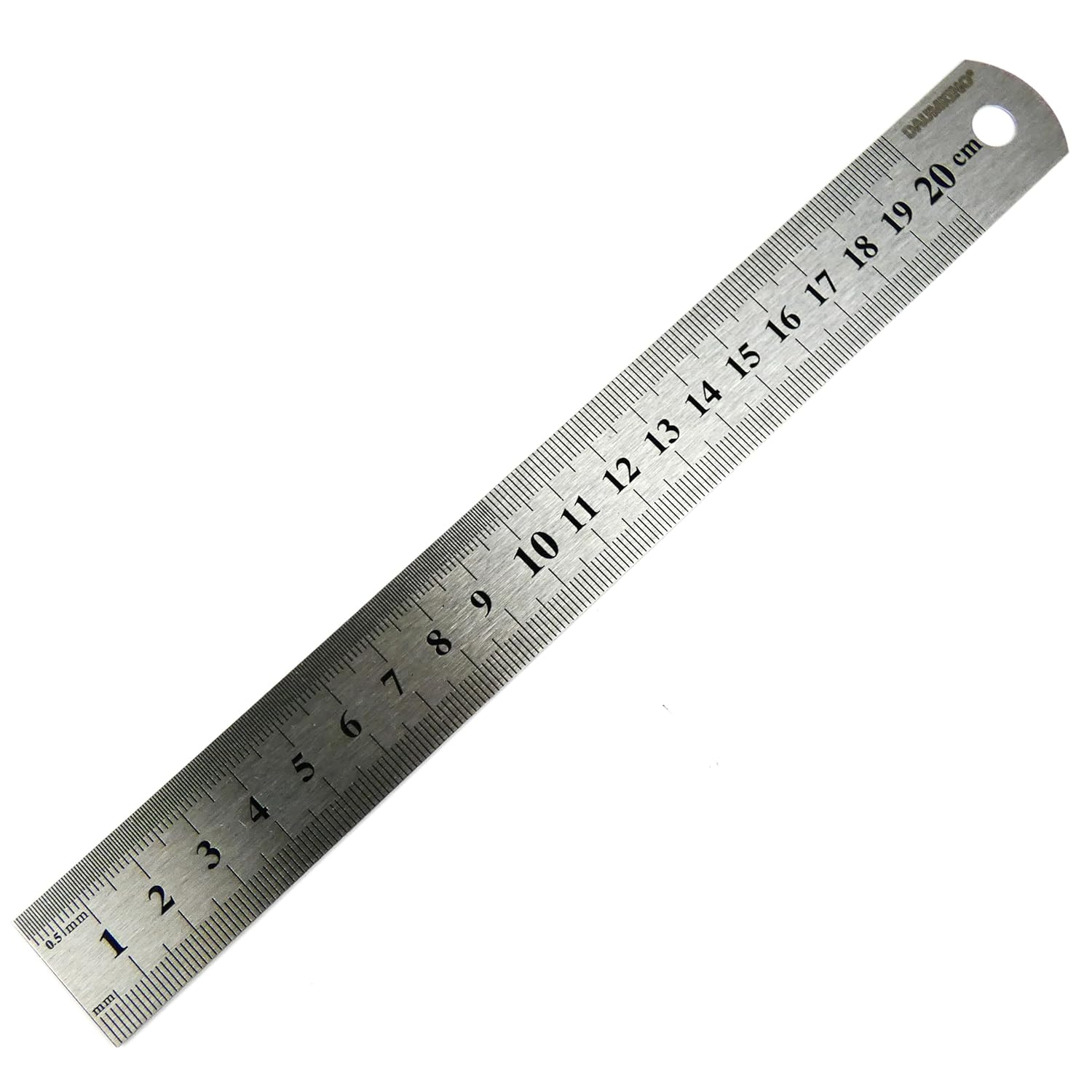
Barra Graduata di Riferimento
Per facilitare la Cabribrazione per le Operazioni ricorrenti ho aggiunto un Barra Graduata Inox sulla Scheda PCB.
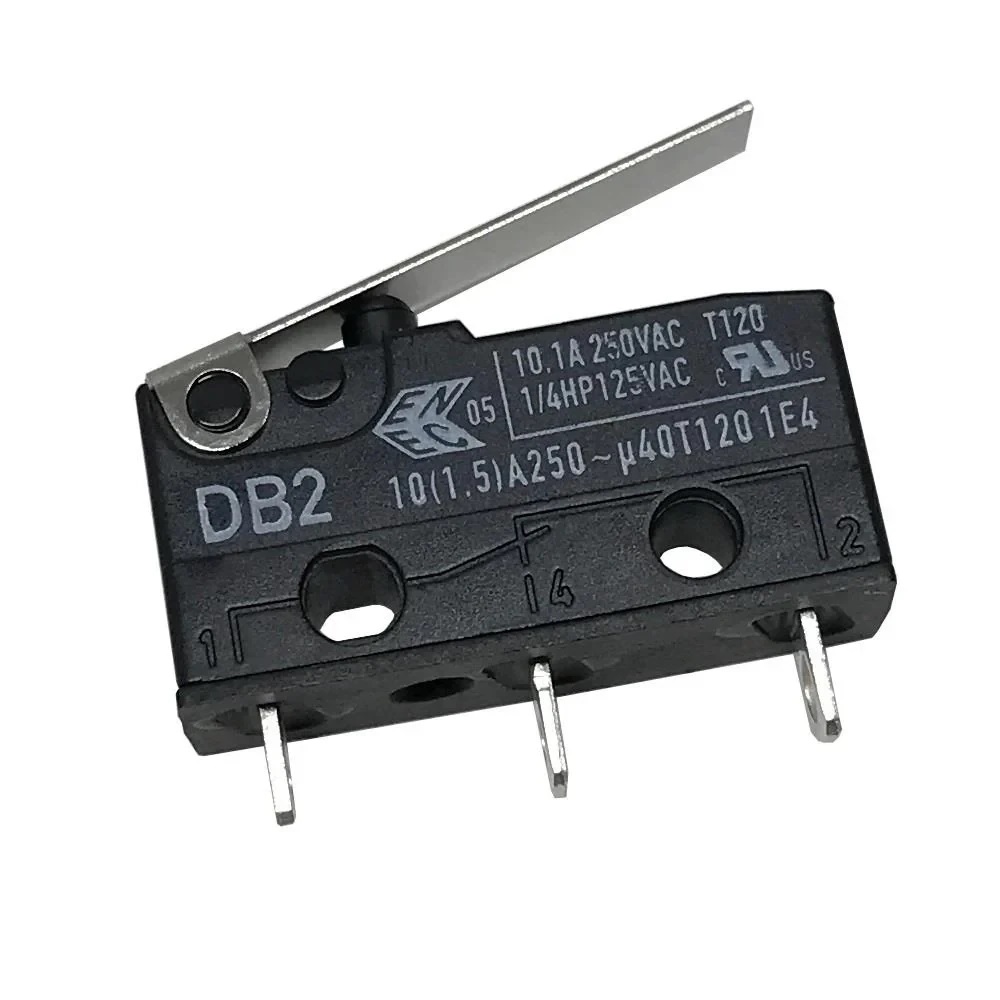
Sistema di Fine Corsa con MicroSwitch
A protezione del MptoRiduttore sono stati aggiunti dei MicroSwitch con Funzione di Fine Corsa.
Indispensabili per implementare i diversi Sistemi di Caricamento poiché la Calibrazione a Zero avviene alle 2 Estremità in relazione al Modalità Operativa.
Schema Elettroco relativo ai Fine Corsa Meccanici a protezione del MotoRiduttore.
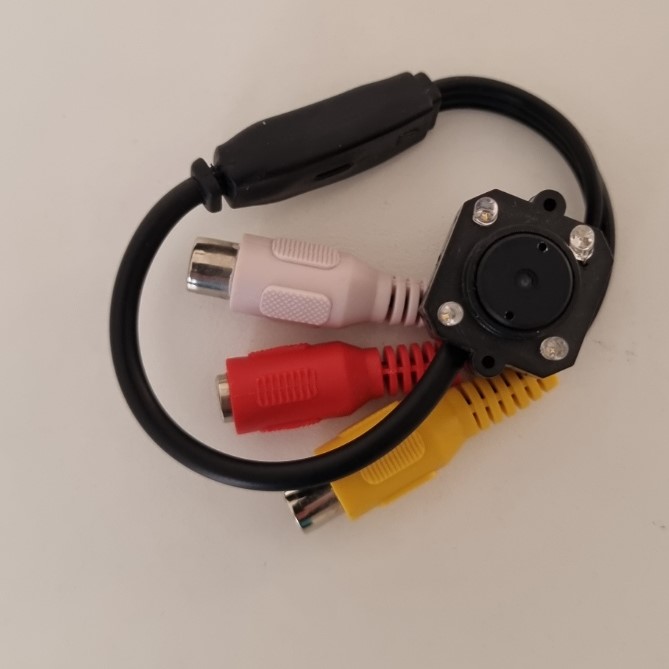
Micro Camera
Avendo aptato per realizzare un Annealer con Bobina chiusa all'Interno dello Chassis ho installato una Micro Camera Interna per controllare il Processo di Ricottura sul Colletto del Bossolo.
Durante la Fase di Realizzazione ho optato per implementare 3 distinti Sistemi di Caricamento:
Sistema Manuale con Shell Holder
In questo Sistema l'Immersione dei Bossoli nella Bobina viene realizzata utilizzando uno Shell Holder.
Al termine del Processo di Ricottura sarà necessario rimuovere Manualmente i Bossoli.
Ottima Soluzione per la Ricottura di Piccoli Lotti.
Nota: Azzeramento per il Sistema di Calibrazione all'Estremità Superiore.
Sistema Manuale con Scarico Automatico
In questo Sistema l'Immersione dei Bossoli nella Bobina viene realizzata Manualmente senza Shell Holder.
Al termine del Processo di Ricottura i Bossoli saranno Scaricati in Modo Automatico mediante l'ausilio di un Solenoide.
Ottima Soluzione per la Ricottura di Lotti Medi.
Nota: Azzeramento per il Sistema di Calibrazione all'Estremità Inferiore.
Sistema di Carico & Scarico con Auto Feeder
In questo Sistema l'Immersione dei Bossoli nella Bobina viene realizzata utilizzando l'Auto Feeder.
Al termine del Processo di Ricottura i Bossoli saranno Scaricati in Modo Automatico mediante l'ausilio di un Solenoide.
Ottima Soluzione per la Ricottura di Grandi Lotti.
Nota: Azzeramento per il Sistema di Calibrazione all'Estremità Inferiore.
Nonostante l'Annealer integri il Sistema per il Controllo dell'Auto Feeder, questo non sarà implementato finché non saranno completate alcune modifiche meccaniche.
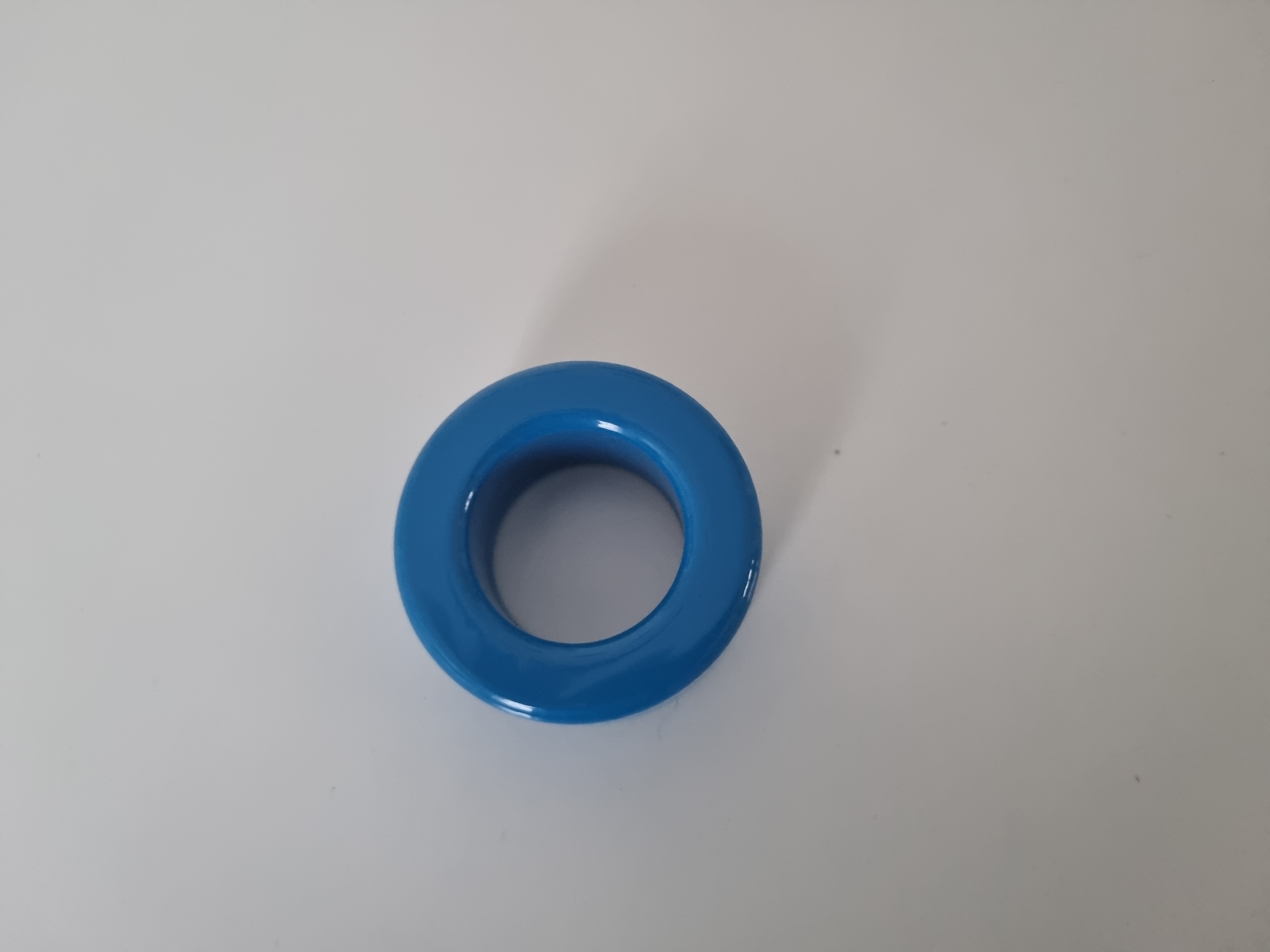
Nucleo Ferro Magnetico
Al fine di migliorare le Prestazioni dell'Annealer avevo intenzione di realizzare una Bobina con Nucleo Ferro Magnetico.
Nelle Bobine Ferro Magnetiche, con la Finestra di Immersione Inferiore ai .575″, non sarà richiesto alcun Sistema di Raffreddamento a Liquido.
Solitamente il 90% delle Cartucce Standard richiede una Finestra Minima di .625″ mentre per le Magnum una Finestra di .875″.
A differenza di una Bobina Standard viene spesso richiesta una Rotazione di 90° per ottenere una Ricottura Uniforme nei Calibri Magnum.
La Soluzione con Nucleo Ferro Magnetico viene spesso utilizzati come Upgrade per gli Annealer a Gas.
Avvertenza: Con Cicli di Lavoro Superiori ai 5 Secondi, al fine di garantire una maggiore Produttività, sarà richiesto un Sistema di Raffreddamento a Liquido.
Attenzione: Utilizzare un Liquido Refrigerante con un inibitore di Corrosione per mantenere Radiatore & Bobina privi di Ossidi.
Solitamente Alluminio & Rame sono Materiali Resistenti alla Corrosione ma in presenza di Acqua avremo:
- Corrosione Rapida dell'Alluminio quando il Ph non sarà Neutro.
- Produzione di Ossidi da parte del Rame che potrebbe condurre l'Ostruzione della Bobina realizzata con un Tubo di Rame da 3mm.
Al fine di ovviare a questo Problema utilizzare dei Filtri nei Punti di Transizione fra i Tubi aventi un Diverso Diametro in modo da garantire l'efficienza del Radiatore.
Avvertenza: Sostituire completamente il Liquido di Raffreddamento almeno una volta all’anno per mantenerne l’efficienza.
Nota: Non riuscendo a reperire un Nucleo Ferro Magnetico (aperto o Chiuso) adeguato ho deciso di accantonare questa Soluzione ed optare per una Bobina Isolata a Doppio Avvolgimento.
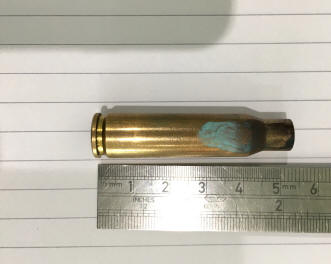
Marcatore Termico "Tempilaq" su Bossolo 308W
Prima di ogni Sessione di Ricottura sarà necessario procedere alla Calibrazione dell’Annealer per determinare, in relazione al Calibro, i seguenti Parametri:
- Profondità di Immersione nella Bobina;
- Tempo di Ricottura.
Per l’Operazione di Calibrazione procedere nel modo seguente:
- Applicare il Marcatore Termico come illustrato nel Paragrafo "Ricottura".
- Inserire la Cartuccia nella Bobina in modo che la Ricottura possa estendersi fino ad 1/4” al di sotto della Spalla.
- Impostare sul Timer Sestos un Tempo di Ricottura di 30 Secondi.
- Avviare l'Operazione di Ricottura utilizzando il Pulsante di START.
Avvertenze: Utilizzando l’Amperometro applicato sulla Linea di Alimentazione verso la Scheda PCB monitorare la Corrente Assorbita.
Qualora la Corrente Assorbita ecceda i 20A premere il Pulsante di STOP.
Solitamento dovrebbe intervenire il Disgiuntore a 20A di Protezione per Alimentatore & Scheda PCB. - Al raggiungimento della Temperatura di Riferimento di 750°F (399°C), quando il Marcatore Termico cambierà colore, premere il Pulsante di STOP.
Solitamente il Tempi di Ricottura, con Alimentare da 36V, sono compresi fra 5 e 10 Secondi in relazione al Calibro. - Impostare sul Timer Sestos per ottenere una Corretta Ricottura del Colletto.
Nota: Tempo ottenuto sottraendo ai 30 Secondi il volore registrato alla pressione del Pulsante di STOP. - Verificare sulla Cartuccia che l’Operazione di Ricottura si estenda fino ad 1/4” al di sotto della Spalla.
Nota: Ampiezza nella variazione di colazione sulla Striscia Longitudinale del Marcatore Termico applicato sulla Cartuccia. - Se la Profondità di Inserimento nella Bobina risulti Corretta Procedere all’Operazione di Ricottura.
In caso contrario procedere alla Regolazione della Profondità di Inserimento prima della Sessione di Ricottura.
Avvertenze: Procedere sempre all’Operazione di Calibrazione per ogni Calibro prima di ogni Sessione di Ricottura.
In presenza di Bossoli realizzati da diverse Manifatture procedere sempre alla Calibrazione per Lotti Uniformi poiché Lega & spessori potrebbero presentare variazioni significative.
Procede all’Operazione di Calibrazione anche in presenza di un nuovo Lotto della medesima Manifattura.
Nota: Registrare, per ogni Calibro & Manifattura, le Impostazioni di Profondità e Tempo necessari per la Corretta Ricottura.
Manual & 3D CAD File
Auto Feeder
- CAD File Auto Feeder per Caricamento Bossoli
Auto Case
- CAD File Auto Case per Scarico Bossoli
Case Height Adjustment
- CAD File Case Height Adjustment
Timer B3S-2R-24
- Manuale Sestos Timer B3S-2R-24
Counter C2S-R-24
- Manuale Sestos Counter C2S-R-24
Temperature Control D1S-2R-24
- Manuale Sestos Temperature Control D1S-2R-24
Timer Delay H3Y-4
- Manuale Omron Timer Delay H3Y-4